Introduction

Filter bags are an essential component in many industrial processes, as they are used to remove contaminants and impurities from liquids, dust, gases, and other materials. However, these bags can have a limited lifespan and need to be replaced frequently, which can be costly and time-consuming. To extend the lifespan of filter bags, there are several steps that can be taken. These include:
Regular maintenance
Regularly cleaning or replacing filter bags can help ensure that they are not clogged with debris, which can reduce their effectiveness and shorten their lifespan.
Regular maintenance is one of the most important steps in increasing the lifespan of filter bags. This includes regularly cleaning or replacing the filter bags to ensure that they are not clogged with debris, which can reduce their effectiveness and shorten their lifespan.
Cleaning filter bags can be done by either shaking or pulsing the bags to remove any loose debris, or by using compressed air to blow the debris out of the bags. However, if the bags are heavily clogged or damaged, it may be necessary to replace them.
It’s also important to check the filter bags for any signs of wear or damage, such as holes, tears, or frayed edges. These can weaken the structure of the filter bag and make it more prone to failure. If any of these issues are found, the filter bag should be replaced immediately.
Note that the frequency of cleaning or replacement depends on the specific application and the conditions the filter bag is exposed to. For example, filter bags in an application with high-temperature or abrasive materials may need to be cleaned or replaced more frequently than those in an application with lower temperatures and less abrasive materials.
Always have a schedule for regular maintenance, this can be done by keeping records of the last time the filter bags were cleaned or replaced, and scheduling the next maintenance accordingly.
Regular maintenance is important in increasing the lifespan of filter bags. It includes cleaning or replacing filter bags on a regular schedule, checking for signs of wear or damage and having a schedule for regular maintenance. This can help to ensure that the filter bags are functioning at their best, and can help to extend their lifespan.
Proper installation
Properly installing filter bags in equipment can help prevent damage from vibration or improper alignment, which can extend their lifespan. It involves ensuring that the filter bags are properly installed in the equipment and are not exposed to any damage from vibration or improper alignment.
When installing filter bags, you should make sure they are securely fastened to the equipment. This can be done by using a metal cage or other support structure to hold the filter bag in place. A filter bag cage can help prevent the filter bag from collapsing and can help to distribute the weight of the filter bag more evenly, which can help to extend its lifespan.
Another important aspect of proper installation is making sure that the filter bag is properly aligned with the equipment. This includes making sure that the filter bag is centered in the equipment and that the inlet and outlet ports are properly aligned to ensure that the liquid or gas flows through the filter bag correctly.
Improper alignment can cause the filter bag to wear unevenly, or can cause the filter bag to collapse, which can shorten its lifespan. The filter bags should be installed in such a way that it should be easily removable for cleaning or replacement. Ensure that the filter bags are not exposed to any damage from vibration. This can be done by installing vibration dampers or other types of isolation devices to reduce the amount of vibration that the filter bags are exposed to. Vibration can cause the filter bag to wear out more quickly, so it’s important to minimize it as much as possible.
Use the right filter bag
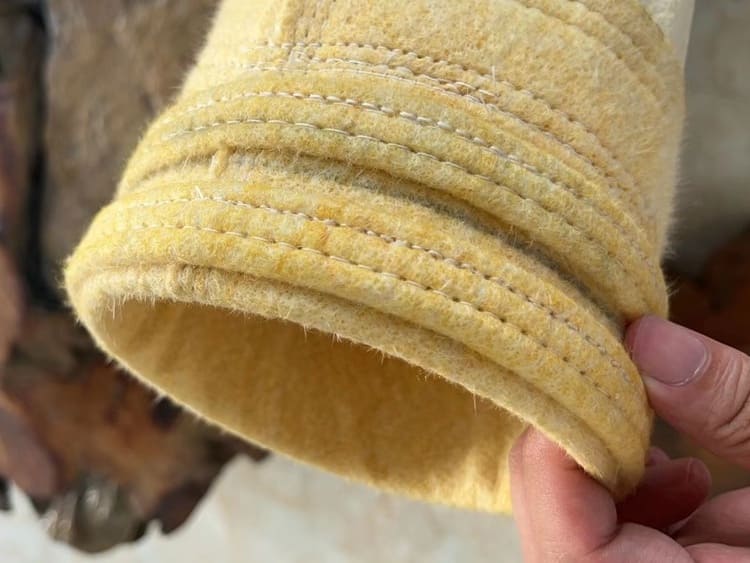
Using the correct type of filter bag for the specific application can help increase its lifespan. It ensures that the filter bag is designed to handle the specific contaminants and conditions that it will be exposed to, which can help to extend its lifespan.
There are different types of filter bags available, each designed for specific applications. Some common types of filter bags include:
- Polypropylene filter bags: These are commonly used in a wide range of industrial applications and are resistant to chemicals and high temperatures.
- Nylon filter bags: These are often used in applications that require a high level of strength and durability. They are also resistant to chemicals and high temperatures.
- Polyester filter bags: These are often used in applications that require a high level of filtration accuracy. They are resistant to chemicals and high temperatures.
- PTFE (Teflon) filter bags: These are often used in applications that require a high level of chemical resistance. They are also resistant to high temperatures.
Consider the size and shape of the filter bag, as well as the type of filter media that is used. For example, some filter bags use pleated media, which can increase the filter area and improve the efficiency of the filter. Others use a depth filter media, which can remove smaller particles.
You must also consider the conditions that the filter bag will be exposed to, such as the temperature, pressure, and chemical composition of the liquid or gas that is being filtered. This will help to ensure that the filter bag is suited for the specific application and will help to increase its lifespan.
Avoid high-temperature
High-temperature can cause filter bags to degrade faster, so it is recommended to avoid exposing them to high-temperature, or use filter bags that are specifically designed to withstand high-temperature.
If you are going to use filter bags in high-temperature applications, it’s important to make sure that the filter bags are made of a material that can withstand the temperature. Some filter bags, such as those made of PTFE (Teflon), can withstand high temperatures up to 500°F, while others may only be able to withstand temperatures up to 250°F.
The filter bags should be installed in a way that will minimize the amount of heat they are exposed to. This can include installing insulation around the filter bags, or using a cooling system to reduce the temperature of the liquid or gas before it enters the filter bags.
Monitor the temperature of the filter bags during operation, and to make sure that the temperature does not exceed the maximum recommended level for the specific filter bag. If the temperature does exceed this level, take the necessary steps to reduce the temperature, such as turning off the equipment or adjusting the process.
Avoid chemical attack
Avoiding chemical attack is an important step in increasing the lifespan of filter bags. Chemical attack can occur when the filter bags are exposed to chemicals that are not compatible with the material of the filter bag, which can cause the filter bag to degrade or fail.
When using filter bags in chemical applications, it’s important to make sure that the filter bags are made of a material that is compatible with the chemicals that they will be exposed to. For example, filter bags made of polypropylene and polyester are resistant to many chemicals, while filter bags made of nylon and PTFE (Teflon) are more resistant to a wide range of chemicals.
It’s also important to ensure that the filter bags are installed in a way that minimizes the amount of chemical exposure they are exposed to. This can include installing a barrier or shield around the filter bags, or using a system to neutralize or remove the chemicals before they enter the filter bags.
You should also check the filter bags for any signs of chemical attack during operation, such as discoloration, swelling, or cracking. If any of these signs are observed, it’s important to take steps to reduce the chemical exposure, such as adjusting the process or replacing the filter bags.
Always check the chemical compatibility of filter bags with the chemical that is going to be filtered, this can be done by checking the chemical resistance chart or consulting the manufacturer.
Avoid abrasive materials

Some filter bags are more prone to wear and tear than others, so it is recommended to use a filter bag that can handle abrasive materials.
When using filter bags in applications where abrasive materials are present, it’s important to make sure that the filter bags are made of a material that is resistant to abrasion. Some filter bags, such as those made of polyester or nylon, are more resistant to abrasion than others, such as those made of polypropylene.
The filter bags must be installed in a way that minimizes the amount of abrasion they are exposed to. This can include installing a pre-filter or other type of mechanical filter before the filter bags to remove larger particles or debris that can cause abrasion.
Monitor the filter bags closed to see if there are any signs of abrasion during operation. This includes holes, tears, or thinning of the filter media. If any of these signs are observed, it’s important to take steps to reduce the abrasion, such as adjusting the process or replacing the filter bags. Take note of the type of abrasive materials that may be present in the liquid or gas being filtered, for example some materials may be more abrasive than others.
Avoiding abrasive materials is an important step in increasing the lifespan of filter bags. It includes making sure that the filter bags are made of a material that is resistant to abrasion, installing the filter bags in a way that minimizes the amount of abrasion, monitoring the filter bags for any signs of abrasion during operation, and taking steps to reduce abrasion if necessary. These steps can help to ensure that the filter bags are functioning at their best and for a long period of time.
Avoid high-pressure
High-pressure can cause filter bags to degrade faster, so it is recommended to avoid high-pressure or use filter bags that are specifically designed to withstand high-pressure. High pressure can cause the filter bags to rupture or fail, which can shorten their lifespan.
When using filter bags in high-pressure applications, it’s important to make sure that the filter bags are designed to withstand the pressure they will be exposed to. The maximum recommended pressure for a filter bag will depend on the specific filter bag and its construction, such as the type of filter media, stitching or gluing used to hold the filter media together and the type of filter bag material.
Install the filter bags in a way that will reduce the amount of pressure they are being exposed to. This can include installing a pressure relief valve or other type of pressure regulation system to keep the pressure within the recommended range for the filter bags.
During operation, keep monitoring the pressure of the filter bags during operation, and ensure that the pressure does not exceed the maximum recommended level for the specific filter bag. If the pressure does exceed this level, it’s important to take steps to reduce the pressure, such as adjusting the process or replacing the filter bags.
Proper storage
Proper storage of filter bags can help increase their lifespan by preventing damage from moisture or extreme temperatures and prolong their lifespan. When storing filter bags, it’s important to make sure that they are stored in a clean, dry place. This can help to prevent the filter bags from becoming contaminated with dust, debris, or other particles that can shorten their lifespan.
Store the filter bags are stored in a way that reduces the amount of stress or pressure on the filter bags. You can do this by storing the filter bags in a flat position, rather than folded or rolled, which can help to prevent creasing or damage to the filter media.
Store them at a place and in a way that they are not exposed to environmental factors, such as extreme temperatures or humidity, which can cause the filter bags to degrade or warp. Always check the filter bags for any signs of damage or wear before using them, and to replace any filter bags that are damaged or worn. This can help to ensure that the filter bags are functioning at their best and can help to extend their lifespan.
Use pre-filters
By using pre-filters, you can remove larger particles from the liquid before it reaches the filter bag, which can help reduce the amount of wear and tear on the filter bag and increase its lifespan. When using pre-filters in conjunction with filter bags, it’s important to make sure that the pre-filters are designed to remove the specific type of particles or debris that are present in the liquid or air being filtered. This can include using pre-filters made of different types of materials, such as metal or plastic, to remove different types of particles or debris.
The pre-filters should be installed in a way that will increase their efficiency. You can do this installing the pre-filters in a location that will capture the majority of particles or debris before they reach the filter bags, and installing the pre-filters in a way that ensures a good flow rate through the pre-filters.
Keep checking closely the pre-filters and filter bags during operation, and to clean or replace the pre-filters as needed. This will ensure that the pre-filters are functioning at their best and can help to extend the lifespan of the filter bags.
Use a filter bag cage

Using a filter bag cage can help support the filter bag and prevent it from collapsing, which can help increase its lifespan. A filter bag cage is a support structure that is placed around the filter bag to hold it in place and protect it from damage.
When using filter bag cages, it’s important to make sure that the cage is made of a material that is compatible with the filter bag and the liquid or gas being filtered. This can include using cages made of materials such as stainless steel, aluminum or plastic. The filter bag cage should be of the right size as the filter bag being used. The cage should be snug enough to hold the filter bag securely in place, but not so tight that it causes damage to the filter bag.
The filter bag cage should be installed in a location that will protect the filter bag from damage. The installation should also ensure that there is good flow rate through the filter bag. This ensures that the bag attains its maximum efficiency. Keep monitoring the filter bag and the cage during operation, and replace the cage or the filter bag if any of them shows any signs of wear or damage.
Conclusion
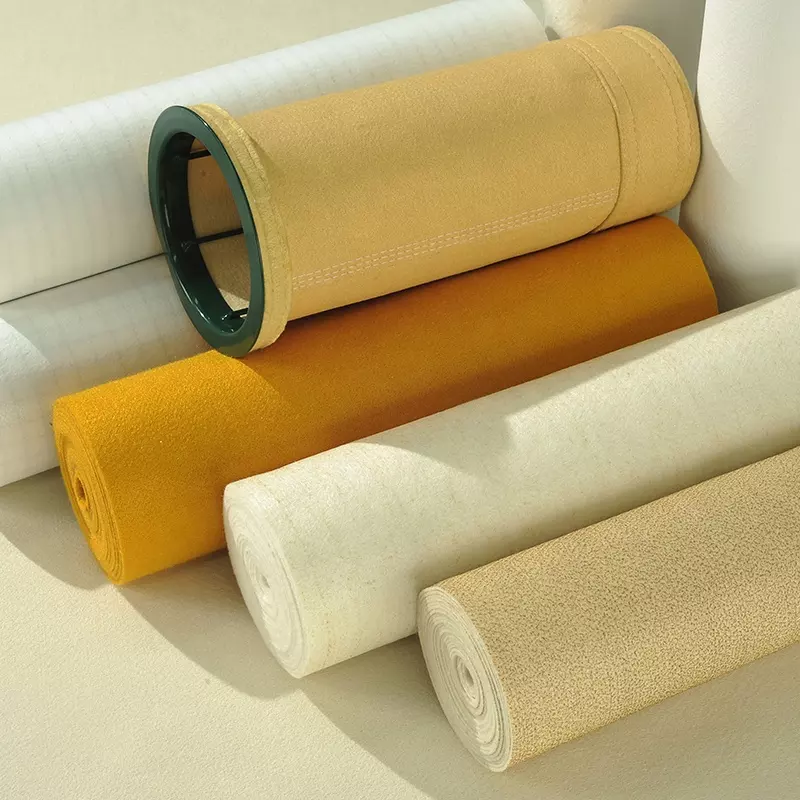
The lifespan of filter bags is important in that t ensures that there is a consistent and efficient filtering of the liquids or gases being filtered. By following the steps outlined above, you can help to extend the lifespan of your filter bags, which can help to reduce the cost of your filtration operations. Whenever you realize that the filter bags are damaged or worn, replace them immediately to avoid damaging your filtering system.
Failure to this will not only reduce the efficiency of your filtration process, but also result in higher costs. Therefore, proper care and maintenance is a must for extending the lifespan of your filter bags. Whenever you need filter bags for replacement or for you new filtration system, you can trust Sofilt to provide the best quality and durable filter bags.
For over 15 years, Sofilt has been a leading supplier of filter bags for industrial and manufacturing applications around the world. With Sofilt, you can get the best quality products at the most competitive prices.Contact our team today for a free quote and enjoy the best quality filter bags in the market.