Introduction

In the dust filtration market, there are many different types of filter bags to choose from. The increasing demand for industrial filtration solutions has made the variety of options more abundant than ever. To help you narrow down your choices, here is a list of the top 10 heavy-duty filter bags for industrial filtration in 2023:
Nomex Filter Bags
Nomex filter bags are a type of heavy-duty filter bag that is commonly used in industries that require high-temperature resistant filtration of gases and particulate matter. Nomex is a brand name for a flame-resistant aramid material developed by DuPont. It is known for its durability, high strength, and resistance to heat, flame, and chemicals. It is a high-temperature resistant fiber that can withstand temperatures up to 204°C. Nomex filter bags are suitable for filtering hot gases in industries such as cement, steel, and power generation.
Cement industry
One of the industries that commonly use Nomex filter bags is the cement industry. Cement production involves the heating of raw materials to high temperatures, which generates a significant amount of dust and gases. The use of Nomex filter bags helps to capture the dust and particulate matter generated during the cement production process, while also allowing for high-temperature filtration of the gases produced.
Steel industry
Another industry that uses Nomex filter bags is the steel industry. In steel production, high-temperature gases are generated during the smelting process. Nomex filter bags can withstand these high temperatures and effectively capture the particulate matter and dust generated during the steelmaking process.
Power generation

Power generation is another industry that uses Nomex filter bags. Power plants generate a lot of heat and produce large amounts of dust and gases during the combustion process. Nomex filter bags can withstand high temperatures and effectively capture dust and particulate matter, reducing emissions and improving air quality.
In general, Nomex filter bags are an essential component in many industrial processes that require high-temperature filtration. Their durability and resistance to heat, flame, and chemicals make them an ideal choice for applications that require a heavy-duty filter bag.
PPS Filter Bags
PPS (Polyphenylene Sulfide) is also a high-temperature resistant fiber that can withstand temperatures up to 190°C. PPS filter bags are suitable for filtering corrosive gases in industries such as chemical and waste incineration. These bags are made of a synthetic polymer material that has high chemical and thermal resistance, making them suitable for use in high-temperature and corrosive environments. PPS filter bags are widely used in industries such as cement, power generation, stainless steel, production, and incineration.
The following are some examples of how PPS filter bags are used in industrial dust filtration:
Cement Industry
The production of cement involves several processes that generate a large amount of dust. PPS filter bags are used in baghouses to capture and filter the dust particles produced during the production process. These filter bags have excellent dust cake release properties, which means that they can remove the collected dust quickly and efficiently.
Power Generation
Coal-fired power plants generate a significant amount of fly ash and other particulate matter. PPS filter bags are used in baghouses to capture these particles and prevent them from being released into the atmosphere. These bags are highly resistant to the acidic and alkaline conditions found in flue gas streams, making them suitable for use in power generation facilities.
Steel Production
The production of steel involves various processes that produce dust and fumes. PPS filter bags are used in baghouses to capture the particulate matter and fumes produced during these processes. These bags have excellent thermal resistance, which allows them to withstand the high temperatures associated with steel production.
Incineration
Incineration is a process used to burn waste materials, which produces a large amount of smoke and ash. PPS filter bags are used in incinerators to capture the smoke and ash particles produced during the process. These bags have excellent chemical resistance, which allows them to withstand the corrosive conditions found in incinerators.
PPS filter bags are widely used in industrial dust filtration due to their excellent chemical and thermal resistance properties. They can be used in various industries to capture and filter dust particles and prevent them from being released into the atmosphere.
P84 Filter Bags
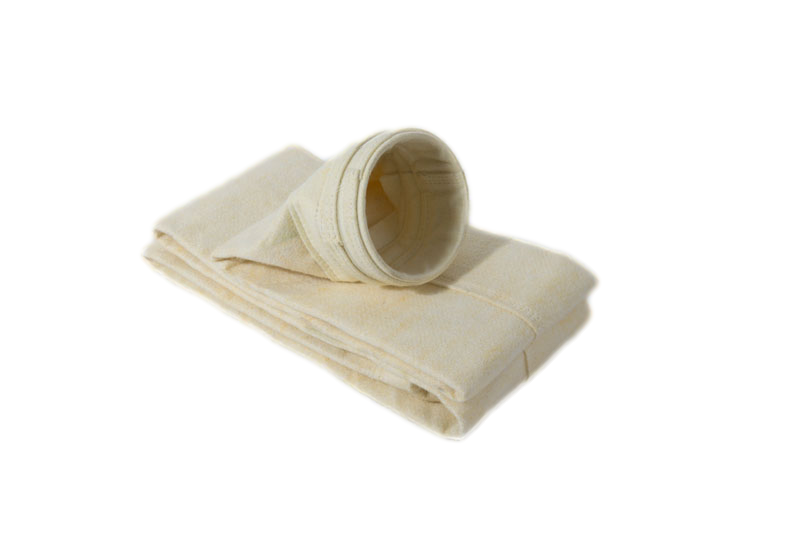
P84 filter bags are a type of filter media used in industrial dust filtration that can withstand temperatures up to 260°C. They are made from a blend of polyphenylene oxide (PPO) and polyamide (PA) fibers that provide excellent filtration efficiency, high-temperature resistance, and good chemical resistance. P84 filter bags are commonly used in applications where high-temperature and chemically aggressive gases and specks of dust are present, such as coal-fired power plants, cement plants, and waste incineration plants.
One of the main advantages of P84 filter bags is their high filtration efficiency. They are capable of capturing small particles down to submicron sizes, which is essential in applications where air quality standards are strict. P84 bag filters also have excellent thermal stability and can withstand temperatures up to 500°C without degrading or melting. This makes them ideal for use in high-temperature applications where other filter media would fail.
Another advantage of P84 filter bags is their good chemical resistance. They can resist the effects of acid and alkali gases, as well as organic solvents and oxidizing agents. This makes them suitable for use in applications where the gas stream may contain corrosive substances.
P84 filter bags are available in various shapes and sizes, including cylindrical bags, envelope bags, and pleated bags. They can be custom designed to fit different types of dust collectors, including pulse-jet, reverse-air, and shaker systems.
For example, in a coal-fired power plant, P84 bag filters may be used in the baghouse to capture fly ash and other particulate matter generated during the combustion process. In a cement plant, P84 filter bags may be used in the kiln to capture dust and other particulate matter generated during the clinker production process. In a waste incineration plant, P84 filter bags may be used in the incinerator to capture hazardous air pollutants and other harmful substances.
P84 bag filters are high-performance filter media used in industrial and commercial dust filtration applications. They offer excellent filtration efficiency, high-temperature resistance, and good chemical resistance, making them suitable for use in a wide range of industries and applications.
Fiberglass Filter Bags
Fiberglass filter bags are a type of filter media used in industrial dust filtration systems to capture fine particles and prevent them from being released into the environment. These bags are made of high-quality fiberglass fibers, which offer excellent filtration efficiency, low resistance to airflow, and resistance to high temperatures, corrosive chemicals and fluid filtration.
They are suitable for filtering high-temperature gases in industries such as foundries, steel mills, and smelters. The use of fiberglass bag filters in industrial dust filtration is quite common, especially in applications where the dust is generated from high-temperature processes such as furnaces, kilns, and boilers. These filters are also widely used in industries such as cement, power generation, and steel production in filter cartridges where large volumes of dust are generated.
The following are some of the advantages of using fiberglass filter bags in industrial dust filtration:
- High Filtration Efficiency: Fiberglass filter bags have a very high filtration efficiency, which means that they can capture even the finest particles. This is crucial in industries where the release of small particles can cause serious health and environmental hazards.
- Low Resistance to Airflow: Fiberglass filter bags have a low resistance to airflow, which means that they do not impede the flow of air through the filtration system. This is important because it ensures that the system operates at optimum efficiency and prevents the buildup of dust that can cause a system failure.
- High-Temperature Resistance: Fiberglass bag filters can withstand high temperatures of up to 500 degrees Celsius, making them ideal for use in applications where high-temperature processes are involved.
- Corrosion Resistance: Fiberglass filter bags are also resistant to corrosive chemicals and gases, which means that they can be used in harsh environments without being damaged.
For example, in a cement plant, large amounts of dust are generated during the production process. The dust contains a mixture of fine particles, which can cause serious health hazards if released into the environment. To prevent this, fiberglass filter bags are used in the dust filtration system to capture the fine particles and prevent their release.
Another example is in a power generation plant. The exhaust gas from the boilers contains a significant amount of fly ash and other fine particles. The fiberglass filter bags are used to capture the fly ash and prevent its release into the environment. The use of these filters ensures that the plant operates in compliance with environmental regulations and prevents air pollution.
Polyester Filter Bags

Polyester filter bags are commonly used in industrial dust filtration to remove particulate matter from the air, such as dust, smoke, and fumes. They are suitable for filtering fine dust particles in industries such as woodworking, food processing, and pharmaceuticals. These bags are made from synthetic fibers that offer several advantages over other materials, including excellent durability, high strength, and resistance to abrasion and chemicals.
Polyester bag filters are manufactured using a variety of techniques, including needle-punching, heat-sealing, and ultrasonic bonding. The process used will depend on the specific requirements and features of the application, such as the size and shape of the bags and the desired filtration efficiency.
One common use of polyester filter bags is in the cement industry, where they are used to capture the fine dust particles that are generated during the production of cement. These bags are typically arranged in rows within a dust collector, which draws air through the bags and captures the dust and dirt particles as they pass through.
Another application of polyester bag filters is in the food processing industry, where they are used to remove airborne contaminants that could potentially contaminate food products. In this case, the bags are typically washed and sterilized between uses to ensure that they remain clean and free of bacteria.
In addition to their use in industrial applications, polyester filter bags can also be used in residential settings to remove dust and allergens from the air. For example, vacuum cleaner bags are often made from polyester fibers and can effectively capture small particles like pet dander and pollen.
Polypropylene Filter Bags
Polypropylene filter bags are suitable for filtering aggressive chemicals and acids in industries such as chemical processing and water treatment due to their excellent filtration performance, durability, and affordability. These bags are made from polypropylene fibers that are tightly woven to form a dense filter media. The high surface area of the filter media allows for the effective capture of fine particles, while the strong construction ensures that the bag can withstand the harsh conditions of industrial processes.
One common use of polypropylene filter bags is in the filtration of cement dust in the cement manufacturing industry. Cement production involves grinding, mixing, and heating raw materials, which generates a significant amount of dust. This dust can be harmful to workers and can cause damage to equipment if not properly controlled. Polypropylene filter bags are an effective solution for capturing cement dust and preventing it from escaping into the environment.
Another application of polypropylene bag filters is in the filtration of metalworking fluids in the metalworking industry. Metalworking fluids are used to cool and lubricate cutting tools during machining processes, but they can become contaminated with metal particles, oil, and other debris. If not properly filtered, these contaminants can cause damage to equipment and affect the quality of the finished products. Polypropylene bag filters and bags are effective at capturing these contaminants and ensuring that the metalworking fluid remains clean and usable.
Polypropylene bags are also used in the filtration of various other types of dust and particulate matter, including silica, coal, and pharmaceutical powders. They can be used in a variety of industrial processes, including mining, power generation, food processing, and pharmaceutical manufacturing.
Polypropylene bag material made of rugged reinforced polypropylene is a reliable and cost-effective solution for industrial dust filtration. Their use in a wide range of industries demonstrates their versatility and effectiveness in capturing various types of dust and particulate matter.
Aramid Filter Bags

Aramid is a high-strength, flame-resistant fiber that can withstand temperatures up to 204°C. Aramid bag filters with higher micron ratings are suitable for filtering high-temperature gases in industries such as asphalt, cement, and incineration.
They are made of aramid fiber, which is a synthetic polymer material with exceptional resistance to heat, chemicals, and abrasion. Aramid fibers have unique properties that make them ideal for industrial applications, particularly in dust filtration systems.
Benefits of Aramid Filter Bags:
- Heat Resistance: Aramid filter bag has excellent heat resistance, making them suitable for use in high-temperature industrial processes such as cement kilns, incinerators, and metallurgical furnaces. They can withstand temperatures up to 250°C (480°F) without any significant degradation in performance.
- Chemical Resistance: Aramid fibers are highly resistant to acids, bases, and most organic solvents. They can resist a wide range of chemicals, making them ideal for filtration applications where chemical exposure is a concern.
- Abrasion Resistance: Aramid fibers are highly resistant to abrasion and wear, making them ideal for applications where the filter bags come in contact with abrasive dust particles.
- Long Life Span: Aramid bag filters have a long life span due to their durability and resistance to heat, chemicals, and abrasion. They require less frequent replacement than other types of filter bags, reducing maintenance costs.
Applications of Aramid Filter Bags:
- Cement Industry: Aramid filter bags are widely used in the cement industry for dust filtration in cement kilns and clinker coolers. The high-temperature resistance and durability of aramid fibers make them ideal for these applications.
- Metallurgical Industry: Aramid filter bags are also used in the metallurgical industry for dust filtration in steel mills, aluminum plants, and other high-temperature industrial processes.
- Incineration: Aramid filter bags are used in incinerators for the filtration of fly ash and other particulate matter. They can withstand the high temperatures and chemical exposure associated with incineration processes.
- Chemical Industry: Aramid filter bags are used in the chemical industry for the filtration of corrosive and hazardous chemicals. They can resist various chemicals, making them ideal for these applications.
Nylon Filter Bags
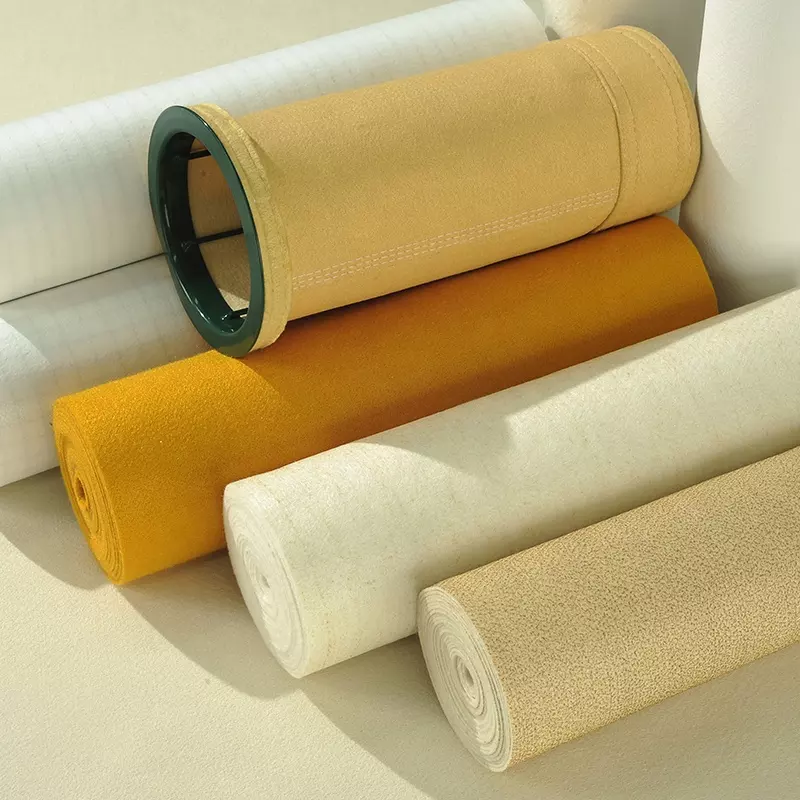
Nylon filter bags are commonly used in industrial dust filtration processes like filtering oils, greases, and other viscous fluids in industries such as food processing, automotive, and paint manufacturing. These bags are made from a synthetic material called nylon, which is known for its strength and durability. Nylon filter bags are used to filter out dust particles from the air in industrial settings.
One of the main advantages of using nylon filter bags is their ability to withstand high temperatures. Nylon can withstand temperatures of up to 300 degrees Fahrenheit, which makes it ideal for use in industrial processes that generate high temperatures, such as metalworking or foundry operations.
Another advantage of nylon filter bags is their resistance to chemical degradation. Nylon is resistant to many chemicals, which makes it suitable for use in industries that involve the use of chemicals, such as pharmaceuticals or food processing.
Nylon filter bags can also be designed to fit different filtration needs. For example, some nylon filter bags are designed to filter out fine particles, such as silica or coal dust. Other nylon filter bags are designed to handle coarser particles, such as sawdust or wood chips.
One common application of nylon filter bags is in the cement industry. Cement production generates a lot of dust, and the use of nylon filter bags can help reduce the amount of dust that is released into the air. Nylon filter bags are also used in the pharmaceutical industry to filter out particles during the production of medicines.
Nylon filter bags are a durable (less bag filter change time) and versatile option for industrial dust filtration. They can withstand high temperatures and resist chemical degradation, making them suitable for a variety of industries. Their ability to be designed to fit different filtration needs also makes them a popular choice for industrial processes including food processing plants.
Cotton Filter Bags

Cotton filter bags are commonly used in industrial dust filtration as they are effective in removing fine dust particles from the air. Cotton is a natural fiber that is biodegradable, sustainable, and widely available, making it a popular choice for use in filter bags.
In industrial settings such as cement plants, power plants, and chemical factories, dust is generated as a byproduct of the manufacturing process. This dust can be harmful to human health and can cause damage to machinery and equipment. Cotton filter bags are used to trap these dust particles, preventing them from entering the air and causing harm.
The cotton filter bags are designed to fit inside a baghouse, which is a large enclosure used to capture dust. The baghouse has a series of compartments where the filter cartridges are installed. As air containing dust passes through the baghouse, the dust particles are trapped by the cotton filter bags, allowing clean air to exit the baghouse.
Cotton filter bags are preferred over synthetic filter bags because they are more breathable and can handle higher temperatures. They are also resistant to chemical degradation, making them suitable for use in harsh industrial environments.
For example, in a cement plant, cotton filter bags are used to capture the dust created during the production process. The cement is made by grinding and heating limestone, clay, and other materials. The grinding process creates fine dust that can be harmful to workers and can damage machinery. The cotton filter bags (filter sock) in the baghouse capture this dust, keeping the air clean and preventing damage to the machinery.
In a power plant, cotton filter bags are used to capture the fly ash created during the combustion of coal. Fly ash is a fine powder that contains toxic substances such as mercury, arsenic, and lead. The cotton filter bags in the baghouse capture this fly ash, preventing it from entering the air and causing harm to the environment.
Cotton filter bags are an essential component in industrial dust filtration systems. They are effective, sustainable, and can withstand higher solid loading in harsh industrial environments. Their ability to capture harmful dust particles makes them crucial in protecting workers’ health and preventing damage to machinery and equipment.
Acrylic Filter Bags

Acrylic filter bags are commonly used in industrial dust filtration for filtering fine dust particles in industries such as pharmaceuticals, plastics, and food processing as they offer superior chemical and temperature resistance compared to other filter bag materials. Acrylic is a synthetic fiber that is widely used in the textile industry and has been adapted for use in filter bags due to its unique properties.
In industrial settings such as chemical factories, metal smelters, and incinerators, dust is generated as a byproduct of the manufacturing process. This dust can contain toxic substances, such as acids and bases, which can cause damage to human health and the environment. Acrylic filter bags are used in open filtration systems to trap these dust particles and prevent them from entering the air.
Acrylic filter bags are designed to fit inside a baghouse, which is a large enclosure used to capture dust. The baghouse has a series of compartments where the filter bags are installed. As air-containing dust passes through the baghouse, the dust particles are trapped by the acrylic filter bags, allowing clean air to exit the baghouse.
Acrylic filter bags are preferred over other filter bags materials such as polyester, polypropylene, and nylon because they can handle higher temperatures and are resistant to chemical degradation. Acrylic filter bags are commonly used in applications where the temperature exceeds 135°C (275°F) and where acids or bases are present.
For example, in a chemical factory, acrylic filter bags are used to capture the dust created during the production process. Chemical reactions can generate fine dust particles that can be harmful to workers and the environment. The acrylic filter bags in the baghouse capture this dust, preventing it from entering the air and causing harm.
In a metal smelter, acrylic filter bags are used to capture the fumes and dust created during the smelting process. The smelting process generates high temperatures and acidic fumes that can cause damage to other filter bag materials. The acrylic filter bags in the baghouse capture these fumes and dust particles, allowing clean air to exit the baghouse.
Acrylic filter bags are an essential component in industrial dust filtration systems. They offer superior chemical and temperature resistance, making them suitable for use in harsh industrial environments. Their ability to capture harmful dust particles and fumes make them crucial in protecting workers’ health and preventing damage to the environment.
Conclusion

The selection of the filter bag depends on various factors, including the type of dust or gas being filtered, the operating temperature, and the specific requirements of the industry. Therefore, it is essential to consult with a filter bag supplier or expert to determine the best filter bag for your particular application. Sofilt will take you through the entire process from planning to installation, ensuring that you get the most cost-effective and efficient filter bag solution. Contact us today to learn more about our filter bag solutions.