Introduction
Air filtration is an essential aspect of modern industrial processes. It helps to ensure a safe and clean working environment while also reducing the impact on the environment. The traditional method of air filtration has relied on air filters made of materials like fiberglass, polyester, and other synthetic fibers. Due to the market dynamics and advancement in technology, other new cutting edge solutions have come up in the dust extraction field.
Polyester anti-static air filters
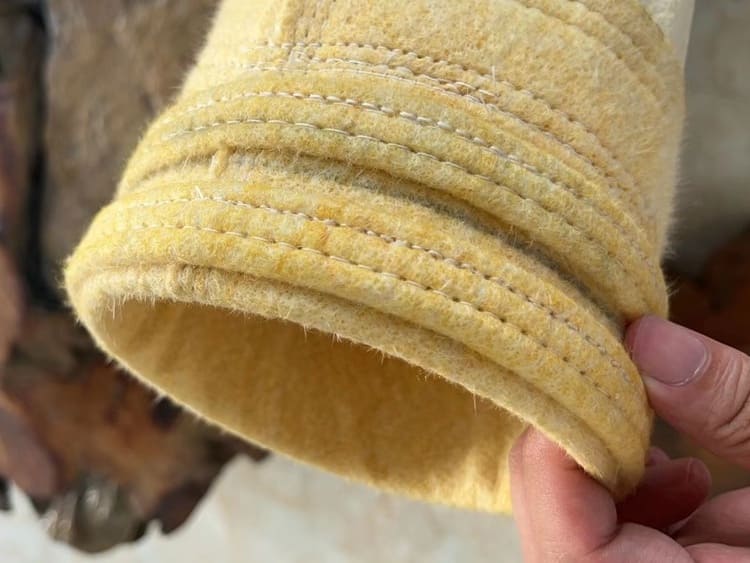
One such solution is the use of Polyester anti-static filter bags. Polyester anti-static filter bags are a type of air filters used in dust collection systems, such as baghouses. These filter bags are made of polyester material that is specially treated to provide anti-static properties. This means that they are able to resist the buildup of static electricity, which can cause dust particles to adhere to the surface of the filter bag and reduce its efficiency.
The anti-static treatment applied to polyester filter bags can be achieved through a broad range of methods, including the use of anti-static agents, conductive fibers, or electrostatic discharge (ESD) materials. Anti-static agents are typically added to the polyester material during the equipment manufacturing process, and are designed to dissipate static electricity as it builds up on the surface of the filter bag.
Conductive fibers, on the other hand, are integrated into the fabric of the filter bag itself. These fibers are typically made of materials such as carbon or stainless steel, and are able to conduct static electricity away from the filter bag and offers protection from the buildup of pollutants.
Another technology used to ensure the effectiveness of polyester anti-static filter bags is ESD materials. These materials are designed to dissipate static electricity through a process of ionization. This success is achieved by using a combination of materials that are highly conductive and have low electrical resistance, such as carbon fiber or stainless steel.
In addition to these technologies, there are also other measures that can be taken to enhance the effectiveness of polyester anti-static filter bags. For example, the use of needle felted nonwoven fabrics can provide additional strength and durability to the filter bag, helping to ensure that it remains effective even in harsh industrial environments. Additionally, the use of high-temperature resistant materials, such as P84 Polyimide, can help to prevent the filter bag from breaking down or losing its anti-static properties under high-temperature conditions.
Needle felting

Needle felting technology is widely used in the manufacture of dust collector filter bags, as it provides a number of key benefits over other forms of filter media. Needle felting is a process where fine fibers are interlocked using a series of needle punches, creating a dense and durable nonwoven fabric. This fabric can then be used to create filter bags that are highly effective at capturing and retaining pollutants. Needle felted filter bags are also known for their high porosity, allowing for excellent air flow and maximum dust collection.
First, needle felted nonwoven fabrics are highly durable and resistant to abrasion, making them ideal for use in harsh industrial environments where dust and other particles are present. This increased durability helps to extend the life of the filter bag and reduce the need for frequent replacement.
Second, needle felted nonwoven fabrics are able to capture and retain dust particles effectively, thanks to their dense and cohesive structure. This results in a filter bag that is highly efficient at removing dust from the air stream and providing clean and safe working environments.
In addition to these benefits, needle felted nonwoven fabrics are also highly resistant to high-temperature conditions. This means that they can be used in a variety of commercial and industrial applications, from woodworking and metal processing to food processing and pharmaceuticals, where high temperatures may be encountered.
Furthermore, needle felted nonwoven fabrics are highly flexible and can be easily molded into a range of shapes and sizes to accommodate different types of dust collector filter bags and filter cages. This versatility makes needle felting an ideal solution for a wide range of industrial applications, providing maximum efficiency and effectiveness in dust filtration.
P84 Polyimide
P84 Polyimide is another material that is being used to revolutionize dust filtration. P84 Polyimide is a high-temperature resistant synthetic fiber that is often used in high-temperature applications, such as those found in the metal processing and smelting industries. P84 Polyimide filter bags are known for their excellent heat resistance, making them ideal for use in applications where the temperature of the air stream is high.
The use of P84 Polyimide in dust collector filter bags provides a number of key benefits over other types of filter media. Firstly, its high heat resistance means that it can withstand temperatures up to 450°C without breaking down or losing its effectiveness, making it ideal for use in high-temperature processes such as welding, metal processing, and cement production.
In addition to its heat resistance, P84 Polyimide also provides excellent mechanical strength and abrasion resistance. This means that it is able to withstand the rigors of continuous use in harsh industrial environments, helping to extend the life of the filter bag and reduce the need for frequent replacement.
P84 Polyimide is also highly resistant to chemical degradation, making it ideal for use in applications where corrosive chemicals may be present. This chemical resistance helps to prevent the filter bag from breaking down or losing its effectiveness, even in the presence of harsh industrial chemicals.
Finally, P84 Polyimide is an environmentally friendly material that is free from hazardous substances and has a low environmental impact. This makes it an ideal choice for companies looking to reduce their environmental footprint and implement more sustainable solutions in their operations.
Fiberglass for industrial filters

Fiberglass is a traditional material that has been used in dust filtration for many years. Fiberglass filter bags are known for their strength and durability, making them ideal for use in harsh industrial environments. Fiberglass is a commonly used material in the manufacture of dust collector filter bags. This material is made from high-strength glass fibers and is known for its strength, durability, and versatility.
Fiberglass is used in the manufacture of dust collector filter bags due to its high temperature resistance and ability to withstand harsh industrial environments. It can withstand temperatures up to 550°C without breaking down or losing its effectiveness, making it ideal for use in high-temperature processes such as welding, metal processing, and cement production.
In addition to its heat resistance, fiberglass also provides excellent mechanical strength and abrasion resistance. This means that it is able to withstand the rigors of continuous use in harsh industrial environments, helping to extend the life of the filter bag and reduce the need for frequent replacement.
Fiberglass is also highly resistant to chemical degradation, making it ideal for use in applications where corrosive chemicals may be present. This chemical resistance helps to prevent the filter bag from breaking down or losing its effectiveness, even in the presence of harsh industrial chemicals.
Finally, fiberglass is an environmentally friendly material that is free from hazardous substances and has a low environmental impact. This makes it an ideal choice for companies looking to reduce their environmental footprint and implement more sustainable solutions in their operations.
It is a versatile and effective material that is widely used in the manufacture of dust collector filter bags. Its high temperature resistance, mechanical strength, abrasion resistance, and chemical resistance, combined with its environmental friendliness, make fiberglass a safe, effective, and sustainable solution for the removal of dust from the air stream in a variety of industrial applications.
The filter cage
The filter cage is another critical component of the air cleaners. The filter cage provides support for the filter bag and helps to ensure that the filter bag remains in place during operation. Filter cages are typically made of metal, such as aluminum or stainless steel, and are designed to withstand the harsh industrial environments in which they are used. In addition, the filter cage plays an important role in the performance of the dust filtration system, as it helps to distribute the air flow evenly across the filter bag and prevent the filter bag from collapsing.
To ensure efficient dust collection, the filter cage must be carefully designed and manufactured to meet the specific requirements of each application. The design of the filter cage will depend on factors such as the type of contaminants being collected, the operating conditions, and the physical properties of the filter bag.
One of the key technologies used to ensure efficient dust collection using filter bags is the use of optimized cage design. The cage design must allow for an even distribution of airflow across the entire surface of the filter bag, ensuring that all of the dust is captured and filtered. To achieve this, the cage may be shaped in a specific way or equipped with specially designed components to help distribute the airflow evenly.
Another important technology used to ensure efficient dust collection is the use of high-quality materials in the construction of the filter cage. The cage must be able to withstand the harsh conditions of the industrial environment, including high temperatures, corrosive chemicals, and mechanical stress. High-quality materials such as stainless steel or aluminum are often used in the manufacture of filter cages, providing the necessary durability and resistance to harsh conditions.
Finally, the technology of baghouse systems plays an important role in ensuring efficient dust collection. A baghouse system typically consists of a series of filter bags housed within a larger chamber. The air stream containing the dust is passed through the filter bags, where the dust is captured and filtered. The cleaned air is then exhausted back into the environment, while the collected dust is disposed of in a safe and controlled manner.
Baghouses for air filtration systems

Baghouses, also known as dust collectors, are the main components of a dust filtration system. Baghouses consist of a series of filter bags that are housed in a large chamber. The dust-laden air is drawn into the baghouse and passed through the filter bags, where the dust particles are captured and retained. The clean air is then exhausted back into the environment. Baghouses are typically made of metal, such as aluminum or stainless steel, and are designed to be highly durable and withstand the harsh industrial environments in which they are used.
One of the key benefits of baghouses is their ability to handle large volumes of air and dust. This makes them ideal for use in a variety of industrial applications, from woodworking and metal processing to food processing and pharmaceuticals. Baghouses are also known for their efficiency, as they can remove up to 99% of dust particles from the air stream.
In recent years, there have been many advances in the design and construction of baghouses, leading to a range of new and innovative solutions for dust filtration. For example, pulse-jet baghouses have been developed, which use pulses of compressed air to clean the filter bags and prevent the buildup of dust on the surface of the filter bags. This results in a baghouse that is more efficient and requires less maintenance than traditional baghouses.
Another innovation in baghouse design is the use of modular construction. Modular baghouses are made up of individual sections, or modules, that can be easily added or removed to accommodate changes in the volume of air and dust being processed. This allows for a highly flexible and scalable solution that can be easily adapted to meet the needs of a wide range of industrial applications.
Conclusion
In conclusion, the field of dust filtration is constantly evolving, with new and innovative solutions being developed all the time. From the use of Polyester anti-static filter bags to the development of pulse-jet baghouses, the focus is on creating more effective and efficient solutions for the removal of dust from the air stream.
Whether it is the use of needle felted nonwoven fabrics or the application of high-temperature resistant materials like P84 Polyimide, the goal is always the same – to provide safe and clean working environments while minimizing the impact on the environment. With the continued development of new and innovative technologies, the future of dust filtration looks bright, and the possibilities for revolutionizing the field are endless.
At Sofilt, a lot of research and innovation has been put into our filter bags and baghouses. We’re constantly striving to develop new and improved products that are more efficient, reliable, and cost-effective. We believe in providing our customers with the best and highest quality dust filtration solutions, no matter their needs and requirements. For more information about our products, please don’t hesitate to contact us. We look forward to helping you improve your dust filtration system.
