Introduction
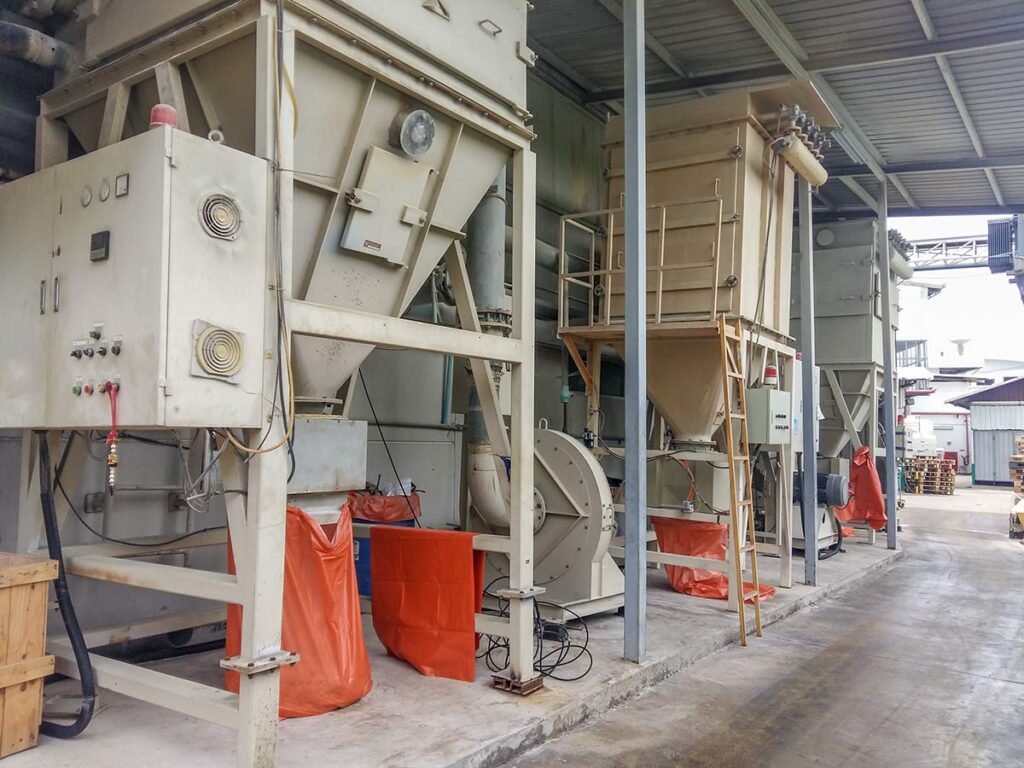
In today’s world, companies are constantly searching for ways to improve their manufacturing processes and reduce their impact on the environment. One of the biggest challenges in the manufacturing industry is controlling airborne pollutants and particulate matter. Fortunately, our advanced baghouse technologies are here to help.
Baghouse filter bags play a critical role in controlling air pollution in manufacturing facilities. They are an essential component of baghouse systems, which are used to remove particulate matter from industrial processes before it enters the atmosphere. The filter bags are designed to trap and hold the particulate matter inside the bag, keeping it from escaping into the environment.
Use of latest materials and designs to improve filter bag performance and increase bag life
Our advanced baghouse technologies use the latest materials and designs to improve filter bag performance and increase bag life. Our baghouse dust collector filters are made from a variety of materials, including woven and non-woven fibers, to ensure they can handle the unique demands of different manufacturing processes. Additionally, our filters are engineered with high-quality construction techniques, ensuring they will not tear or break down over time thus increasing the filter life.
The materials and designs used in advanced baghouse technologies are crucial in improving filter bag performance and increasing bag life. These materials and designs have been developed over time in response to the growing need for more efficient and effective air pollution control solutions. Here are a few ways in which the latest materials and designs improve filter bag performance and increase filter life:
- Improved Material Strength: One of the most important aspects of a filter bag is its strength. The latest materials used in advanced baghouses are engineered to be stronger and more durable, ensuring that the filter bags can withstand the harsh conditions of the manufacturing process without tearing or breaking down. For example, the materials used in advanced baghouses include aramid and PTFE fibers, which are known for their high strength and durability.
- Improved Surface Area: The surface area of the dust collector filter bag plays a critical role in its ability to capture and retain particulate matter. The modern designs in advanced baghouses use multiple layers and special coatings to increase the surface area of the filter bag, improving its overall performance and increased output. These multiple layers and coatings help to increase the area available for particulate matter to adhere to, allowing the filter bag to capture more particulate matter and improve the overall collection efficiency of the baghouse system.
- Enhanced Dust Release Properties: The ability of a filter bag to release captured particulate matter is also critical to its performance. The latest materials and designs used in advanced baghouses have been developed to improve dust release properties, ensuring that the filter bags can easily release captured particulate matter when they are cleaned or changed. This helps to improve the overall efficiency of the baghouse system and reduce the frequency of maintenance thus lowering operating cost.
- Improved Resistance to High Temperatures: Many manufacturing processes generate high temperatures, which can cause traditional filter dust collector filter bags to break down and release particulate matter into the environment. The latest materials used in advanced baghouses, such as ceramic and metallic fibers, have been developed to be highly resistant to high temperatures, ensuring that they can maintain their effectiveness even in the harshest of conditions.
Handle high temperature applications

One of the key benefits of our advanced baghouse dust collectors technologies is their ability to handle high temperature applications. Many manufacturing processes generate high temperatures, which can cause traditional baghouse filters to break down and release particulate matter into the environment. Our baghouse pleated filters are specifically designed to withstand high temperatures, ensuring they will maintain their effectiveness even in the harshest of conditions.
In baghouses, the dust collector filter bags play a crucial role in capturing and retaining the dust particles produced during the manufacturing process and to allow proper airflow with increased output. However, in high temperature applications, the filter bags are exposed to extremely high temperatures, which can cause them to degrade and even fail, leading to the release of dust into the environment.
To address this issue, our advanced baghouses use high temperature applications technology to provide enhanced resistance to heat. This technology involves the use of materials like PTFE (polytetrafluoroethylene) and aramid that have high temperature resistance properties. The filter bags made from these materials can withstand temperatures up to 260°C, ensuring reliable and consistent performance in high temperature applications thus minimizing downtime for better airflow.
Additionally, modern day baghouses also use techniques like needling and thermal bonding to further enhance the heat resistance of the filter bags. Needling involves piercing the filter media with high-pressure needles to increase the mechanical strength and durability of the bags, while thermal bonding involves using heat and pressure to bond the filter media layers together, creating a stronger, more heat-resistant bag.
High temperature applications technology has revolutionized the dust collection industry, providing improved performance, superior filtration efficiency, reliability, and safety in high temperature applications. This innovative filter has allowed industries to reduce the emission of dust particles into the environment, thus promoting a cleaner and safer work environment.
Increased collection efficiency of the baghouse dust collectors
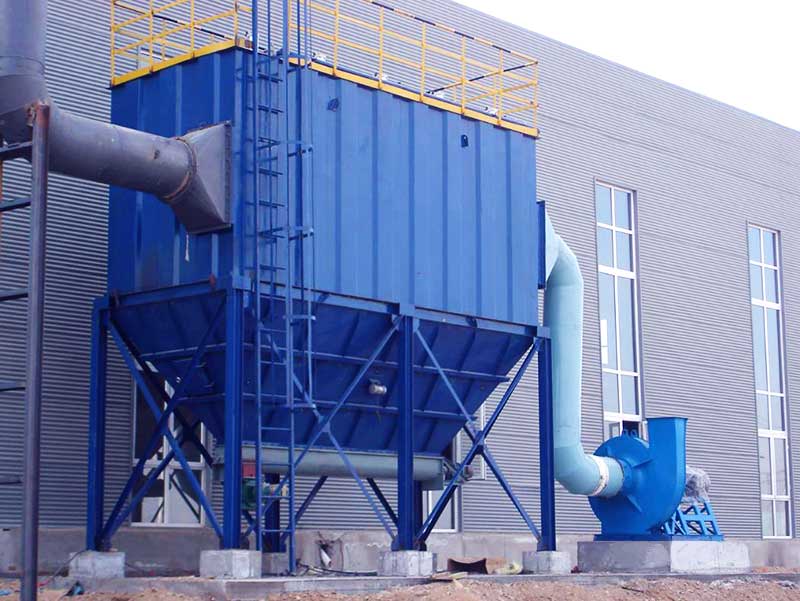
Another important feature of our baghouse technologies is their ability to increase collection efficiency. Our bags are designed with special features, such as multiple layers and special coatings, to increase the surface area available for particulate matter to adhere to. This means that our bags are able to collect more particulate matter, improving the overall performance of the baghouse system and lower operating costs.
The following are some of the advanced technology used to increase the efficiency of the baghouse dust collectors:
- Pulse-jet cleaning systems: Advanced baghouse dust collector use pulse-jet cleaning systems to clean the filter bags. This system uses compressed air to create pulses of high-pressure air that travel through the filter bags, dislodging the accumulated dust particles and causing them to fall into the hopper for collection. Pulse-jet cleaning systems provide a more efficient and effective cleaning process compared to traditional shaking or rapping methods.
- Improved filter media: The filter media is the key component of the dust collection process, and advanced baghouses use specialized filter media to increase efficiency. The use of high-efficiency filter media such as nanofiber or ePTFE (expanded polytetrafluoroethylene) enhances the filtration process, improved compressed air consumption, providing finer particle collection and higher collection efficiency.
- Modulated inlet flow: Modulated inlet flow involves adjusting the flow rate of the compressed air consumption to the baghouse. This helps to regulate the compressed air usage across the filter bags, reducing the amount of dust that escapes the collection process.
- Automated filter monitoring: Advanced baghouse dust collectors use automated filter monitoring systems to monitor the operating differential pressure and pressure drop across the filter bags. This helps to detect when the bags need cleaning, reducing the risk of dust escape or efficient dust control and improving collection efficiency.
- Improved bag design: Advanced baghouse dust collector uses specialized bag designs that improve the dust collection process. The use of V-shaped or pleated filter bags, for example, increases the surface area available for filtration, providing more efficient collection and longer filter life.
Smart Controls

Smart controls are the use of computerized control systems in baghouse dust collector for effective dust collection. These systems are designed to monitor and adjust cleaning patterns based on changes in process conditions, improving the overall performance of the baghouse dust collector and reducing energy consumption.
Smart controls use sensors and algorithms to determine the most appropriate cleaning schedule for the current process conditions. For example, if the dust loading on the bags is low, the smart control system may delay cleaning until the dust loading reaches a certain level. Conversely, if the dust loading is high, the smart control system may initiate a cleaning cycle more frequently to maintain the performance of the baghouse.
They also allow for real-time monitoring of baghouse dust collector performance and emissions, providing valuable data for process optimization and compliance with emissions regulations. Additionally, smart controls can be integrated with other plant systems, such as the plant’s control system, cartridge to provide a more comprehensive view of plant operations and performance.
Smart controls have significantly improved the effectiveness of baghouses for effective dust collection in several ways. They help to reduce energy consumption by optimizing the cleaning schedule and reducing unnecessary cleaning cycles. They also improve collection efficiency by ensuring that cleaning cycles are initiated at the appropriate time, preventing the buildup of dust on the bags.
They provide valuable data for process optimization and troubleshooting, allowing plant operators to identify and resolve issues with the baghouse system more quickly and efficiently. This leads to improved overall performance and reduced maintenance costs, making baghouses with smart controls a cost-effective and environmentally-friendly solution for particulate control.
Electrically-enhanced filtration
Electrically-enhanced filtration is a technology that applies an electrical charge to the particulate to increase its attraction to the filter media, leading to improved collection efficiency. Our baghouses dust collectors are equipped with electrically-enhanced filtration, the particulate is charged as it enters the baghouse and then attracted to the positively charged filter media, where it is captured and held until the bags are cleaned.
This has improved the effectiveness of our baghouses for effective dust collection in several ways. Firstly, it has increased the collection efficiency of the baghouse, as the electrically-charged particulate is more strongly attracted to the filters, reducing the amount of particulate that escapes capture.
This can also improve the collection efficiency of the baghouse for smaller particles, which are typically more difficult to capture. This is because the electrical charge helps to overcome the diffusion and thermophoretic forces that would otherwise cause these particles to escape capture.
It also reduces the frequency of bag cleaning required, as the charged particulate is captured more effectively and builds up on the filter more slowly. This leads to reduced energy consumption, as the cleaning cycles are initiated less frequently, and reduced maintenance costs, as the bags require less frequent cleaning and replacement.
Finally, electrically-enhanced filtration can improve the overall performance and longevity of the baghouse system, as it reduces the amount of particulate that is accumulated on the bags, reducing the risk of bag failure and improving the overall performance of the baghouse.
Electrically-enhanced filtration is a highly effective technology for improving the performance of our baghouses for effective dust collection, and its use has become increasingly popular in industrial processes where particulate control is a key concern.
Continuous emission monitoring systems (CEMS)

Continuous Emission Monitoring Systems (CEMS) are monitoring devices used in industrial processes to continuously monitor and measure the emission levels of pollutants from various sources such as chimneys, stacks, and vents. These systems are designed to provide real-time data on the emission levels of pollutants and help facilities to comply with air quality regulations set by governing bodies.
Baghouses are one of the most commonly used air pollution control devices for the collection of particulate matter, including dust, from industrial processes. In the past, the effectiveness of baghouses was primarily determined by visual inspections and manual measurements, which were both time-consuming and unreliable. The introduction of CEMS has significantly improved the effectiveness of baghouses by providing real-time, continuous data on the emissions levels of pollutants.
CEMS provides data on the amount of particulate matter emitted from a facility and can detect any changes in the particulate matter concentration in real-time. This data is then used to determine the efficiency of the baghouse and make any necessary adjustments to improve its performance including energy savings. For example, if the CEMS data shows that the emissions levels of pollutants are increasing, the facility can make adjustments to the baghouse to reduce the emissions levels.
CEMS also provides an accurate and reliable means of verifying the compliance with air quality regulations, reducing the risk of penalties and other legal consequences for non-compliance. Additionally, CEMS provides a historical record of the emissions levels of pollutants, which can be used to demonstrate the facility’s commitment to environmental sustainability and to track the progress made over time.
Biodeposition filtration
Biodeposition filtration is a method of air filtration that utilizes microorganisms to degrade particulate matter in the air. This approach to filtration has improved the effectiveness of our baghouses, a type of air filtration system commonly used in industrial settings, by reducing the amount of dust that needs to be captured and disposed of, and by increasing the service life of the filter bags.
In a biodeposition filtration system, air is drawn through a biological filter medium, such as compost or a biofilter, where microorganisms degrade the particulate matter into organic compounds. The microorganisms then use these organic compounds as a food source to grow and reproduce, effectively removing the particulate matter from the air stream.
The benefits of biodeposition filtration in baghouses include:
- Improved collection efficiency: The use of biological processes to degrade particulate matter means that less dust is captured in the filter bags, leading to improved collection efficiency and reduced maintenance requirements.
- Longer filter bag life: The reduced amount of dust captured in the filter bags means that the bags are exposed to less wear and tear, leading to longer service life.
- Lower disposal costs: The reduced amount of dust captured in the filter bags means that disposal costs are lower, as there is less waste to dispose of.
- Improved indoor air quality: Biodeposition filtration leads to improved indoor air quality, as it reduces the amount of particulate matter in the air.
- Lower energy consumption: Biodeposition filtration systems typically consume less energy compared to traditional baghouses, as they do not require the use of fans or blowers to move air through the filter medium.
Finally, our advanced baghouse dust collector technologies are designed to be easy to install and maintain. Our filter cloth is simple to replace, reducing the time and cost associated with maintenance. Additionally, our baghouse systems are designed to be highly efficient, using less energy and reducing operation costs.
Conclusion

Our advanced baghouse technologies offer a reliable and effective solution for controlling particulate matter in manufacturing facilities. Our filter bags are designed to handle high temperatures, increase collection efficiency, and reduce maintenance costs, making them the ideal choice for companies looking to protect their manufacturing environment. Contact us today to learn more about how our advanced baghouse technologies can help you improve your manufacturing processes and protect the environment.
With more than 15 years of experience in the dust collection filter industry, Sofilt is determined to provide the best and most cost-effective filtration solutions. Our experienced team of engineers is committed to working with our customers to develop effective and efficient air filtration systems for their specific applications, allowing them to protect their workers, improve air quality, and reduce their environmental impact.
Whether you are in the Cement plants, Pharmaceutical Industry, Woodworking, Mining, or Metal Processing, our team of experts is here to help. Our competent team of experts will be able to provide you with the best solutions for your specific application. Contact us today to find out how our advanced baghouse technologies can help you improve your manufacturing processes and protect the environment.