Introduction
Dust control is a critical aspect of manufacturing operations. Dust can be generated from various sources in the manufacturing process, including raw materials, processing equipment, and finished products. Dust poses a significant risk to workers’ health and can lead to respiratory problems, allergic reactions, and even cancer. In addition, dust can also cause equipment damage, product contamination, and environmental pollution. Therefore, it is essential to optimize dust control in manufacturing to minimize the risks associated with dust exposure.
In this comprehensive guide, we will discuss various strategies for optimizing dust control in manufacturing, including identifying sources of dust, implementing engineering controls, adopting administrative controls, and utilizing personal protective equipment. We will also examine the benefits of implementing a comprehensive dust control program and how to measure its effectiveness.
Identifying Sources of Dust
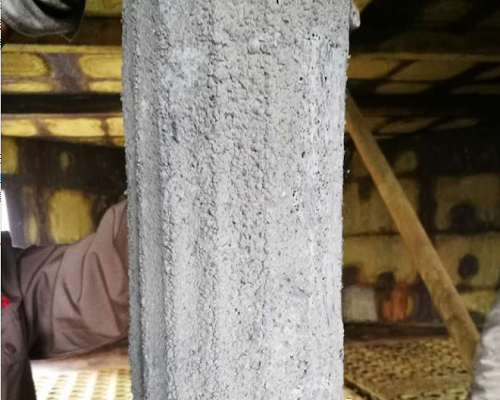
The first step in optimizing dust control in manufacturing is identifying the sources of dust. Dust can be generated from many sources, including:
- Raw Materials: Raw materials, such as wood, metals, and plastics, can generate dust during handling and processing.
- Processing Equipment: Equipment, such as grinders, saws, and sanders, can generate dust during use.
- Finished Products: Finished products, such as coatings, paints, and adhesives, can generate dust during manufacturing and application.
- Workplace Surfaces: Dust can accumulate on workplace surfaces, such as floors, walls, and ceilings.
- Outdoor Sources: Outdoor sources, such as construction activities, traffic, and windblown dust, can also contribute to indoor dust levels.
Once the sources of dust have been identified, it is essential to determine the extent of dust generation and the pathways through which the dust can be dispersed. This information can be used to develop an effective dust collection system.
Implementing Engineering Controls
Engineering controls are physical measures that can be implemented to control dust at its source or during the transmission of dust produced. The most effective engineering controls are those that eliminate or minimize the source of dust. Some examples of engineering controls include:
Local Exhaust Ventilation (LEV)
Local exhaust ventilation (LEV) is an engineering control that is commonly used to control dust and other airborne contaminants in manufacturing environments. LEV involves capturing the dust at the source of the generation using a hood or capture device and then conveying it to a dust collector or other dust collection system. By capturing the dust particles at the source of generation, LEV can effectively toxic dust emissions and reduce worker exposure to airborne contaminants. The design of an LEV system is critical to its effectiveness.
The system must be designed to ensure that the air velocity of the hood is sufficient to capture the dust at the source of generation. The hood should be positioned as close as possible to the source of the dust generation to ensure that the dust is effectively captured. The size and shape of the hood should also be designed to match the characteristics of the dust load being generated. The hood should be positioned to provide a clear and unobstructed path for the dust to be conveyed to the dust collector or other air-cleaning device.
The choice of industrial dust collectors or air cleaning devices is also important in the design of an LEV system. Different types of dust control systems and air-cleaning devices are available, including baghouses, cyclones, electrostatic precipitators, and wet scrubbers. The choice of the type of dust collector or air cleaning device will depend on the characteristics of the dust being generated, the volume of dust being generated, and the specific needs of the manufacturing process.
The effectiveness of an LEV system depends on a number of factors, including the design and layout of the manufacturing process, the type and characteristics of the dust being generated, and the effectiveness of the hood and dust collection system. The system should be regularly inspected and maintained to ensure that it is operating effectively and efficiently. Regular monitoring and testing should also be conducted to verify the effectiveness of the system in controlling dust emissions and worker exposure to airborne contaminants.
LEV systems can be integrated into the manufacturing process in a number of ways. In some cases, they may be integrated into the design of the manufacturing process from the outset. In other cases, they may be retrofitted into existing manufacturing processes to control toxic dust emissions and worker exposure to airborne contaminants. In all cases, the design and operation of the LEV system should be tailored to the specific needs of the manufacturing process.
There are a number of benefits to using LEV systems to control dust emissions in manufacturing environments. By capturing dust at the source of generation, LEV systems can effectively control dust emissions and reduce worker exposure to airborne contaminants. This can help to protect workers’ health and safety and reduce the risk of occupational illnesses, such as lung disease and respiratory problems. LEV systems can also help to improve the quality of the work environment by reducing the amount of dust and other airborne contaminants in the air. This can improve the overall health and well-being of workers and improve the quality of the products being manufactured.
Wet Methods for dust collector

Wet methods are a type of engineering control used to control dust and other airborne contaminants in manufacturing environments. Wet methods involve the use of water or other liquids to suppress the dust and prevent it from becoming airborne. Wet methods are commonly used in industries such as construction, demolition, and mining, as well as in other manufacturing processes that generate large amounts of dust.
There are a number of different wet methods that can be used to control dust in manufacturing environments. One common method is the use of water sprays. Water sprays can be used to suppress dust emissions at the source of generation, or they can be used to wet down surfaces and prevent dust from becoming airborne. Water sprays can be applied using a variety of different equipment, including handheld sprayers, hoses, and automated spray systems. The choice of equipment will depend on the specific needs of the manufacturing process and the characteristics of the dust being generated.
Another wet method that can be used to control dust in manufacturing environments is the use of misting systems. Misting systems generate a fine mist of water or other liquid that is sprayed into the air to suppress dust emissions. Misting systems can be used in a variety of different manufacturing processes, including material handling, grinding, and cutting. Misting systems can be used in combination with other engineering controls, such as LEV systems, to provide a more comprehensive approach to dust control.
In addition to water sprays and misting systems, other wet methods that can be used to control dust in manufacturing environments include the use of foam, wetting agents, and dust suppressants. These materials can be applied to surfaces or to the dust itself to prevent it from becoming airborne. The choice of material will depend on the specific needs of the manufacturing process and the characteristics of the dust being generated.
There are a number of benefits to using wet methods to control dust in manufacturing environments. Wet methods are effective at suppressing dust emissions and preventing dust from becoming airborne. This can help to reduce worker exposure to airborne contaminants and protect workers’ health and safety. Wet methods are also relatively low cost and easy to implement, making them a practical solution for many manufacturing processes.
There are also some challenges associated with the use of wet methods in manufacturing environments. Wet methods can increase the humidity in the work environment, which can create discomfort for workers and potentially affect the quality of the products being manufactured. In addition, wet methods can increase the risk of slip and fall accidents, particularly if the wet surfaces are not properly marked or if workers are not provided with appropriate personal protective equipment.
Dust Collection System
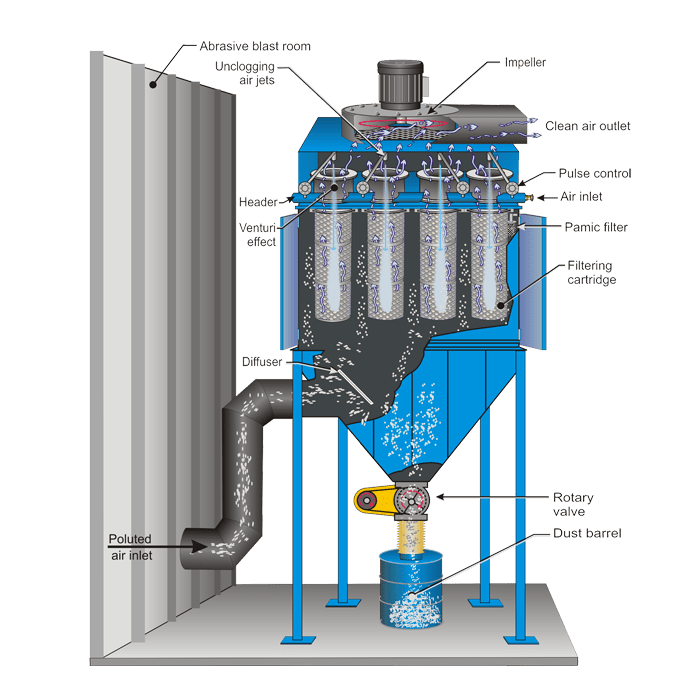
Dust collection systems are an essential engineering control used to optimize dust control in manufacturing environments. These systems are designed to capture and remove dust and other airborne contaminants from the air, helping to reduce worker exposure to these harmful substances.
Dust collection systems typically consist of several components, including a hood or enclosure that captures the dust at the source of generation, a duct system that transports the dust to a collection device, and a collection device that separates the dust from the air stream. The collection device may use a variety of different technologies, including filters, cyclones, and electrostatic precipitators, to remove the dust from the air.
There are a variety of different types of dust collection systems that can be used in manufacturing environments, including central systems, portable systems, and hybrid systems. Central systems are typically used in larger manufacturing operations, where dust is generated in multiple locations. These systems are designed to collect the dust at each source of generation and transport it to a central collection device.
Portable systems, on the other hand, are designed to be moved to different locations within a manufacturing facility, making them ideal for smaller operations or for areas where dust is generated on an occasional basis. Hybrid systems combine elements of both central and portable systems, allowing for maximum flexibility and efficiency.
Dust collection systems can provide a number of benefits for manufacturing operations. These systems help to reduce worker exposure to airborne contaminants, protecting workers’ health and safety. Dust collection systems can also help to reduce the risk of fires and explosions, as combustible dust can accumulate and become a potential hazard in some manufacturing processes. In addition, dust collection systems can help to improve product quality, as dust and other contaminants can have a negative impact on the quality of the products being manufactured.
There are some challenges associated with the use of dust collection systems in manufacturing environments. These systems require regular maintenance and cleaning to ensure that they are functioning properly and providing effective dust control. In addition, dust collection systems can be expensive to install and operate, particularly for larger manufacturing operations.
Enclosures and Barriers

Enclosures and barriers are another engineering control used to optimize dust control in manufacturing environments. These controls work by enclosing the source of dust generation, preventing the dust from escaping into the surrounding environment and exposing workers to harmful substances.
Enclosures can take a variety of different forms, depending on the manufacturing process and the type of dust being generated. For example, in some cases, enclosures may be large rooms or buildings that contain the entire manufacturing process, while in other cases, enclosures may be small hoods or booths that are placed over individual machines or workstations.
In addition to preventing the escape of dust, enclosures and barriers can also help to reduce noise levels and control temperature and humidity, which can be particularly important in some manufacturing processes.
One potential challenge associated with the use of enclosures and barriers is that they can limit access to the manufacturing process, making it more difficult for workers to interact with the machines or perform necessary tasks. However, this challenge can often be addressed by incorporating access doors or windows into the enclosures, or by designing the enclosures to be easily disassembled or reconfigured as needed.
Overall, enclosures and barriers are an effective engineering control that can help to optimize dust control in manufacturing environments. By enclosing the source of dust generation, these controls can prevent the escape of dust into the surrounding environment, protecting workers from harmful substances and improving overall air quality in the workplace.
Material Substitution
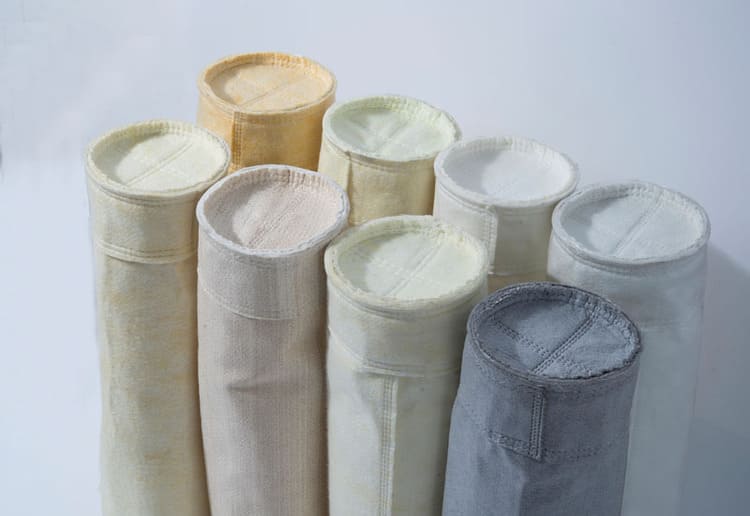
Material substitution is another approach that can be used to optimize dust control in manufacturing environments. This approach involves replacing hazardous materials with less hazardous or non-hazardous materials that can perform the same function. By using less hazardous materials, it is possible to reduce the amount of dust generated during manufacturing processes, thereby reducing worker exposure to harmful substances.
There are many different types of hazardous materials that may be used in manufacturing, including chemicals, metals, and organic materials. Each of these materials has its own unique set of hazards, and the specific hazards associated with a particular material will depend on the manufacturing process and the type of material being used.
One example of material substitution in manufacturing is the use of water-based paints and coatings, which can replace solvent-based paints and coatings. Water-based paints and coatings are generally less hazardous than solvent-based alternatives, and they can be just as effective at providing a high-quality finish. Similarly, in the construction industry, the use of engineered wood products, such as laminated veneer lumber, can replace traditional solid wood products, reducing worker exposure to wood dust.
Material substitution can provide many benefits for manufacturing operations. By using less hazardous materials, it is possible to reduce the amount of dust generated during manufacturing processes, protecting workers’ health and safety. In addition, the use of less hazardous materials can often reduce the risk of fires and explosions, as many hazardous materials are also flammable or explosive.
Some of the challenges associated with the use of material substitution in manufacturing include less hazardous materials may be more expensive than their more hazardous counterparts, which can increase the cost of manufacturing. In addition, it may be more difficult to find suitable alternatives for some materials, particularly in cases where the hazardous material is essential for the manufacturing process.
In general material substitution is an effective approach that can be used to optimize dust control in manufacturing environments. By replacing hazardous materials with less hazardous alternatives, it is possible to reduce worker exposure to harmful substances and improve overall air quality in the workplace. However, it is important to carefully evaluate the benefits and challenges of material substitution for each specific manufacturing process to determine whether it is a viable option.
Implementing Administrative Controls

Administrative controls are measures that are implemented to change the way work is performed or to modify the work environment. These measures are typically used when engineering controls are not feasible or effective. Some examples of administrative controls include:
- Work Practices: Work practices involve changing the way work is performed to minimize dust generation. For example, using wet methods when cutting or grinding, or cleaning work areas frequently to remove accumulated dust.
- Training: Workers should be trained on the hazards associated with dust exposure and the measures that are in place to control dust. Workers should also be trained on the proper use of personal protective equipment (PPE).
- Maintenance and Inspection: Regular maintenance and inspection of processing equipment are important to ensure that they are operating efficiently and not generating excess dust. Maintenance and inspection can also identify worn or damaged parts that may need replacement.
- Housekeeping: Regular cleaning of the work environment is important to prevent dust accumulation and prevent dust explosions in the work environment. Housekeeping measures can include sweeping, vacuuming, and wet mopping.
Job Rotation: Job rotation involves rotating workers between different tasks to reduce their exposure to dust beyond permissible exposure limits. This can be especially effective in tasks that generate a significant amount of dust.
Utilizing Personal Protective Equipment
Personal protective equipment (PPE) is a final line of defense against dust exposure. PPE should only be used after engineering and administrative controls have been implemented to minimize the risk of dust exposure. Some examples of PPE that can be used to protect workers from dust exposure include:
- Respirators: Respirators are the most common type of PPE used to protect workers from dust exposure. Respirators can be either filtering facepieces (such as N95 masks) or powered air-purifying respirators (PAPRs).
- Gloves: Gloves can be used to protect workers’ hands from exposure to dust.
- Eye and Face Protection: Eye and face protection, such as goggles and face shields, can be used to protect workers’ eyes and face from dust exposure.
- Protective Clothing: Protective clothing, such as coveralls, can be used to protect workers’ skin from dust exposure.
Benefits of Implementing a Comprehensive Dust Control Program
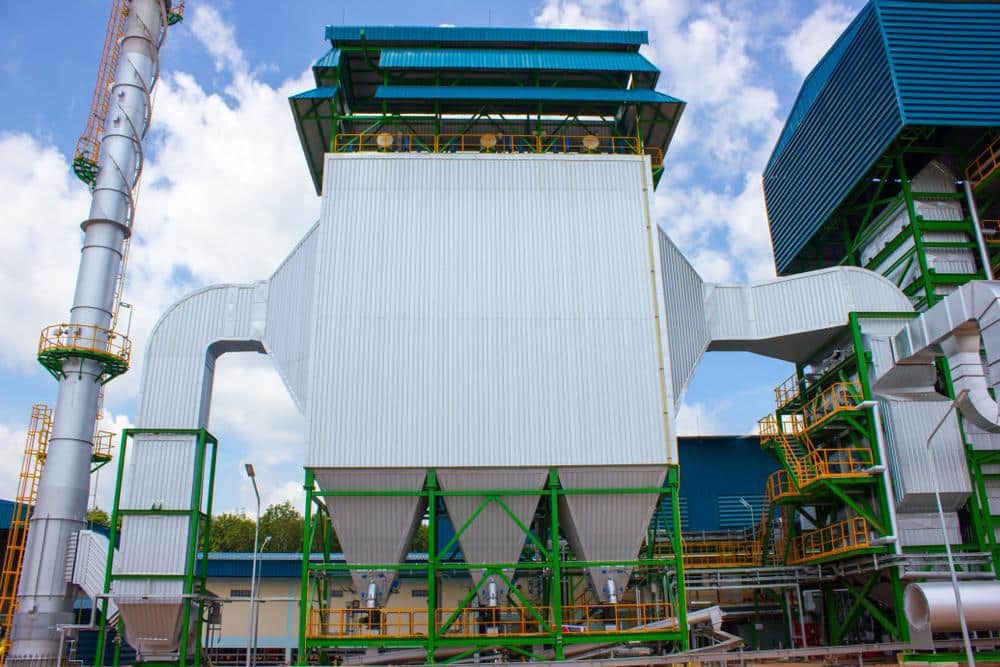
Implementing a comprehensive dust control program can provide numerous benefits, including:
- Improved Health and Safety: The primary benefit of implementing a dust control program is to protect workers’ health and safety. A comprehensive dust control program can significantly reduce workers’ exposure to dust and the associated health risks.
- Increased Productivity: Dust can cause equipment damage, product contamination, and downtime. A comprehensive dust control program can reduce these issues, leading to increased productivity.
- Compliance with Regulations: Many regulatory agencies, such as the Occupational Safety and Health Administration (OSHA), require employers to implement dust control measures to protect workers’ health and safety.
- Positive Public Image: Implementing a comprehensive dust control program demonstrates a commitment to health and safety and can improve the public image of the organization.
Measuring the Effectiveness of a Dust Control Program
Measuring the effectiveness of a dust control program is essential to ensure that the program is providing the desired level of protection for workers. Some measures that can be used to assess the effectiveness of a dust control program include:
- Dust Monitoring: Dust monitoring can be used to measure the amount of dust in the work environment before and after implementing dust control measures. This can help to determine the effectiveness of the measures.
- Air Quality Monitoring: Air quality monitoring can be used to measure the levels of airborne contaminants in the work environment. This can help to identify potential health risks to workers.
- Worker Exposure Monitoring: Worker exposure monitoring can be used to measure the levels of dust exposure among workers. This can help to identify areas where additional dust control measures may be needed.
- Incident Reports: Incident reports can be used to track the number and severity of incidents related to dust exposure. This can help to identify areas where additional dust control measures may be needed.
Conclusion

In conclusion, optimizing dust collectors in manufacturing is essential to protect workers’ health and safety and to prevent equipment damage, product contamination, and environmental pollution. Employers should regularly review and update their dust control program to ensure that it is meeting the changing needs of their business and their workers.
Implementing a comprehensive dust control program requires a commitment from employers and employees to create and maintain a safe work environment. Employers should provide training and education to workers to help them understand the risks associated with dust exposure and the importance of implementing dust control measures. Employers should also involve workers in the development and implementation of a dust control program to ensure that the program is effective and feasible for their work environment.
In summary, optimizing dust control in manufacturing is a complex process that requires a multi-faceted approach as per the national fire protection association guidelines. Employers should take a systematic approach to identifying sources of dust, implement engineering and administrative controls, utilize personal protective equipment, and maintain regular monitoring and inspection of the work environment.
By implementing a comprehensive dust control program, employers can protect their workers’ health and safety, increase productivity, comply with regulations, and enhance their public image. Ultimately, a safe and healthy work environment benefits everyone, from workers to employers and the wider community.