Introduction
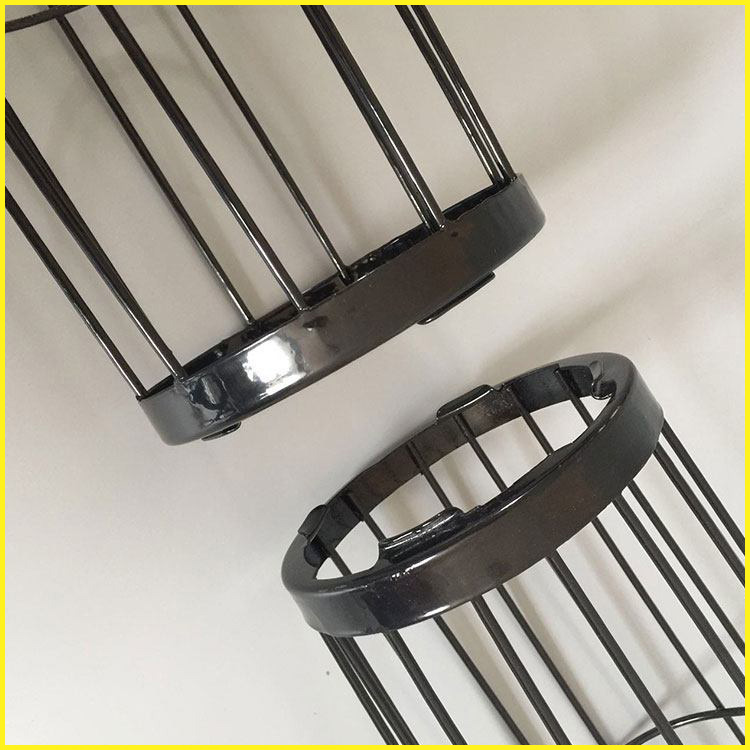
Filter bags are an integral part of any industrial filtration system. They are designed to trap and remove dust and other particles from a wide range of industrial processes. Filter bags are available in various materials and designs, and they work by capturing dust particles and fine dust that flow through them while allowing clean air to pass through.
They play a crucial role in maintaining a clean and safe working environment in various industries, including pharmaceuticals, food processing, and manufacturing. They are essential for preventing dust and other harmful particles from escaping into the atmosphere, protecting workers’ health, and complying with environmental regulations.
Filter bags are subjected to harsh conditions, including high temperatures, corrosive chemicals, and abrasive materials. As a result, they are prone to wear and tear, which can lead to a decrease in filtration efficiency and increased maintenance costs. To ensure maximum durability and longevity of filter bags, it is crucial to choose the right filter bag frame solution.
We will discuss the common problems associated with filter bags for dust collectors and explore the various frame solutions available, including wire cages, self-cleaning, top load, bottom load, and pulse jet. Additionally, we will examine the factors to consider when choosing a filter bags frame, such as the type of dust and particle size, the chemical composition of the dust, airflow, operating temperature, and maintenance requirements. By the end of this article, you will have a clear understanding of the various filter bag frame solutions available and be able to make an informed decision on which solution is best suited for your specific industrial filtration needs.
Common Problems with Filter Bags
Wear and Tear
Dust collection systems are critical in maintaining a safe and healthy work environment in various industries. These systems work by collecting dust and debris generated during industrial processes before it becomes airborne and inhaled by workers. Industries such as woodworking, metalworking, and construction generate a high volume of dust, which can be dangerous if not adequately collected. A dust collection system is essential in maintaining a clean and safe working environment for employees.
The potential hazards of poor dust collection systems
Wear and tear is one of the most common problems associated with filter bags. This problem occurs when filter media are subjected to continuous use and exposure to harsh conditions, such as high temperatures, corrosive chemicals, abrasive materials, and moisture. Over time, this exposure causes the filter bag material to deteriorate, resulting in holes, tears, or rips that compromise the filter’s effectiveness and efficiency.
When filter bags are compromised, they can allow dust particles to bypass the air filtration system, leading to increased air pollution, decreased air quality, and potential safety hazards in the workplace. Additionally, wear and tear can cause the filter bag to collapse or distort, leading to further problems such as dust bypass, decreased filtration efficiency, and increased maintenance costs.
To address the problem of wear and tear, it is crucial to choose the right filter bag frame solution that maximizes durability and can withstand the harsh conditions of industrial processes. For example, some filter bag frames, such as wire cages, are designed to provide structural support to the filter bag, preventing it from collapsing or distorting under the weight of the dust particles it captures. Other filter bag frames, such as pulse jet, are designed to periodically clean the filter bag, preventing the buildup of dust cake that can lead to wear and tear.
Regular maintenance of filter bags is also crucial in preventing wear and tear. This can include regularly cleaning the filter media and inspecting them for signs of wear and tear. If wear and tear is detected, it is important to replace the filter bag as soon as possible to prevent further damage to the filtration system.
Corrosion
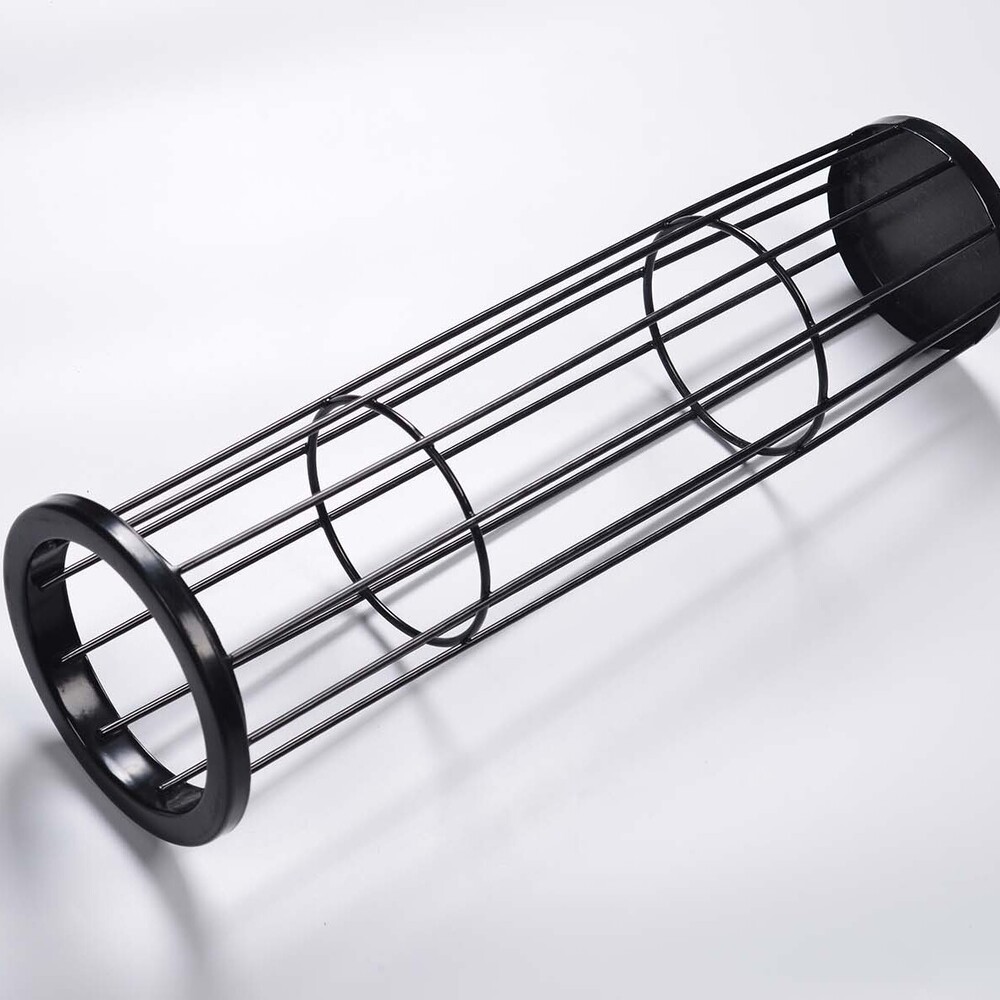
Corrosion is another common problem associated with filter bags that can lead to decreased filtration efficiency and potential safety hazards in the workplace. Corrosion occurs when filter bags and frames are exposed to corrosive chemicals or substances, such as acids or alkalis, which can attack and weaken the filter bag material and frame.
When filter bags are corroded, the filter bag material can become brittle or disintegrate, causing holes and tears that allow dust particles to bypass the filtration system. This can result in increased air pollution and decreased air quality in the workplace. Additionally, the weakened filter bag frame can break or lose its structural integrity, leading to potential safety hazards and increased maintenance costs.
In order to prevent the issue of corrosion, it is important to choose the right filter bag frame solution that can withstand the corrosive conditions of industrial processes. For example, some filter bag frames are made from materials that are resistant to corrosion, such as stainless steel or galvanized steel. These frames can provide the necessary structural support to the filter bag and prevent it from collapsing or distorting under the weight of the dust particles it captures.
Another solution to prevent corrosion is to implement regular maintenance practices that include cleaning the filter bags and inspecting them for signs of corrosion. If corrosion is detected, it is important to replace the filter bag and frame as soon as possible to prevent further damage to the filtration system.
Abrasion
Abrasion is another common problem associated with filter media that can lead to decreased filtration efficiency and potential safety hazards in the workplace. Abrasion occurs when bag filters and frames are subjected to abrasive materials, such as sand or gravel, which can wear down the filter bag material and frame.
When filter bags are subjected to abrasion, the filter bag material can become thin and weakened, causing holes and tears that allow dust particles to bypass the filtration system. This can result in increased air pollution and decreased air quality in the workplace. Additionally, the weakened filter bag frame can break or lose its structural integrity, leading to potential safety hazards and increased maintenance costs.
The issue of abrasion can be avoided by choosing the right filter bag frame solution that can withstand the abrasive conditions of industrial processes. For example, some filter bag frames are made from materials that are resistant to abrasion, such as carbon steel or aluminum. These frames can provide the necessary structural support to the filter bag and prevent it from collapsing or distorting under the weight of the dust particles it captures.
Another way of preventing abrasion is to implement regular maintenance practices that include inspecting the filter bags and frames for signs of abrasion. If abrasion is detected, it is important to replace the filter bag and frame as soon as possible to prevent further damage to the filtration system.
Chemical Degradation
Chemical degradation is another common problem associated with filter bags that can lead to decreased filtration efficiency and potential safety hazards in the workplace. Chemical degradation occurs when bag filters and frames are exposed to chemical substances that can cause the filter bag material to degrade over time.
When filter bags are exposed to chemical degradation, the filter bag material can become weak and brittle, causing holes and tears that allow dust particles to bypass the filtration system. This can result in increased air pollution and decreased air quality in the workplace. Additionally, the weakened filter bag frame can break or lose its structural integrity, leading to potential safety hazards and increased maintenance costs.
To address the problem of chemical degradation, it is important to choose the right filter bag material and frame solution that can withstand the chemical conditions of industrial processes. For example, some filter bag materials are made from chemically resistant materials, such as Teflon or fiberglass, that can withstand exposure to corrosive chemicals. Additionally, some filter bag frames are made from materials that are resistant to chemical degradation, such as stainless steel or polypropylene.
You can also prevent chemical degradation by implementing regular maintenance practices that include inspecting the filter bags and frames for signs of chemical degradation. If chemical degradation is detected, it is important to replace the filter bag and frame as soon as possible to prevent further damage to the filtration system.
In general, these common problems with filter bags can lead to decreased filtration efficiency, increased maintenance costs, and potential safety hazards in the workplace. To address these issues, it is crucial to choose the right filter bag frame solution that maximizes durability and can withstand the harsh conditions of industrial processes.
Top Frame Solutions for Filter Bags

Choosing the right filter bag frame solution is essential to maximizing the durability and efficiency of dust filters. Here are the top filter bag frame solutions for various industrial applications:
Wire Cages
Wire cages are a common and cost-effective solution for supporting filter bags. These cages are typically made from galvanized steel wire and are designed to fit snugly around the filter bag. They provide a reliable and sturdy support structure for filter bags.
They are easy to install and replace and can withstand high temperatures and abrasive environments. Wire cages can sometimes cause abrasion and wear on the filter bag material, leading to decreased filtration efficiency over time.
Self-Cleaning
Self-cleaning filter bag frames are designed to shake or vibrate the filter media periodically to remove dust buildup or dust cake and prevent clogging. Self-cleaning frames can significantly extend the lifespan of filter bags by reducing the frequency of manual cleaning and maintenance. They can also improve filtration efficiency and prevent clogs that can damage the filter bags.
Top Load
Top load frames are designed to load bag filters from the top and are typically used in applications where dust collection is not continuous. They are easy to install and replace and provide a reliable support structure for filter They are also suitable for applications where dust collection is intermittent. Top load frames can be difficult to access and replace when located in hard-to-reach areas, such as high elevations or confined spaces.
Bottom Load
Bottom load frames are designed to load filter bags from the bottom and are typically used in applications where dust collection is continuous. Bottom load frames are easy to access and replace, making them suitable for applications where frequent maintenance is required.
They also provide a sturdy support structure for filter bags. Bottom load frames can be more expensive than other frame solutions and may require additional maintenance to prevent clogs and ensure proper operation.
Pulse Jet
Pulse jet frames use compressed air or reverse air to pulse clean the filter bags, removing dust buildup and preventing clogging. Pulse jet frames are highly efficient and can significantly extend the lifespan of filter bags by reducing the frequency of manual cleaning and maintenance. They can also improve filtration efficiency and prevent clogs that can damage the filter bags.
Choosing the right filter bag frame solution is crucial to maximizing the filter life and efficiency of dust filters. Wire cages, self-cleaning frames, top load frames, bottom load frames, and pulse jet frames are all effective solutions that can meet the unique needs of various industrial applications. By selecting the right filter bag frame solution, it is possible to maintain a clean and safe working environment while minimizing maintenance costs and downtime.
Factors to Consider When Choosing a Filter Bag Frame
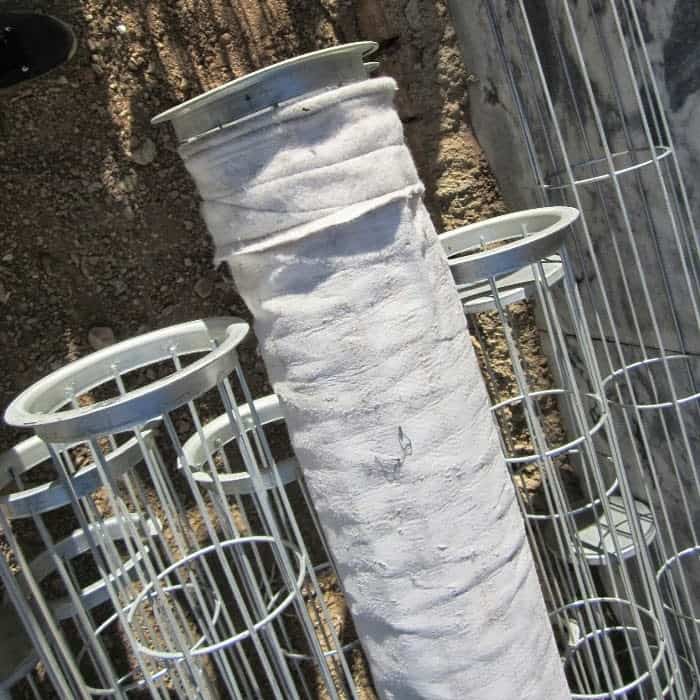
Selecting the right filter bag frame is crucial to maximizing the durability and efficiency of dust filters. Here are the key factors to consider when choosing a filter bag frame:
Type of Dust and Particle Size
The type of dust and particle size is a critical factors to consider when choosing a filter bag frame. Different types of dust have varying particle sizes, shapes, and characteristics that can affect filtration efficiency. For example, fine powders such as cement dust have small particle sizes and require a tight weave filter bag that can capture small particles. In contrast, larger particles such as wood chips have irregular shapes and require a more open weave filter bag that can accommodate larger particles.
To determine the appropriate filter bag frame, it is important to understand the particle size distribution and composition of the dust. The particle size distribution refers to the range of particle sizes present in the dust. The composition of the dust refers to the type of material that makes up the dust, such as organic or inorganic materials, and whether it is abrasive or non-abrasive.
For example, in a foundry that produces metal castings, the type of dust generated is usually a mixture of metallic and non-metallic particles of various sizes. A bag filter that is used to capture this type of dust should be able to withstand the abrasive nature of the particles and have a suitable pore size to capture the particles.
In the food industry, the type of dust generated may be organic and non-abrasive. A bag filter used in this application should be made from materials that are approved for food contact and have a suitable pore size to capture the particles. The choice of filter bag frame depends on the type of dust and particle size, as well as the operating conditions of the system.
For example, in high-temperature applications, such as in a cement plant, filter bag frames made from high-temperature alloys may be required to withstand the harsh operating conditions. In contrast, in low-temperature applications, such as in a woodworking facility, a self-cleaning filter bag frame may be more suitable to prevent clogging.
Overall, understanding the type of dust and particle size is crucial in determining the appropriate filter bag frame. By selecting the right filter bag frame, the filtration efficiency can be maximized, and maintenance costs and downtime can be minimized.
Chemical Composition of the Dust
The chemical composition of the dust is another crucial factor to consider when choosing a filter bag frame. The chemical properties of the dust can affect the filtration efficiency of the filter bag and its lifespan. Dust can be acidic, alkaline, or neutral, and it can also contain corrosive substances that can degrade the filter bag material.
For example, in a chemical processing facility that produces acidic dust, the filter bag frame should be made from materials that are resistant to corrosion, such as stainless steel or a special alloy. In contrast, in a pharmaceutical facility that produces neutral or non-corrosive dust, the filter bag frame material can be less robust.
It is important to consider the chemical composition of the dust because certain materials can react with the dust, causing it to stick to the filter bag or degrade the filter bag material. This can result in reduced filtration efficiency, increased pressure drop, and ultimately, the need for frequent filter bag replacements.
Moreover, some chemicals can be toxic, and they may pose a health hazard to workers. Therefore, it is important to choose a filter bag frame that can effectively capture the dust and minimize the risk of exposure to workers.
When selecting a filter bag frame based on the chemical composition of the dust, it is important to work closely with a filter bag supplier who can provide expert advice on the best materials to use. The supplier can help determine the appropriate material, pore size, and filtration efficiency required for a specific application.
The chemical composition of the dust is a crucial factor to consider when selecting a filter bag frame. By selecting the right filter bag frame material, the filter bag’s lifespan can be extended, the filtration efficiency can be maximized, and the risk of exposure to hazardous chemicals can be minimized.
Airflow
Airflow is a critical factor to consider when selecting a filter bag frame for dust filters. Airflow affects the filtration efficiency, pressure drop, and energy consumption of the dust collection system. The airflow requirements can vary depending on the application, and they are affected by factors such as the dust particle size, air to cloth ratio, the concentration of dust in the air, and the volume of air to be filtered.
When selecting a filter bag frame, it is essential to consider the airflow requirements to ensure that the dust collector can operate efficiently. If the airflow is too low, the dust collector may not effectively capture the dust particles, leading to decreased filtration efficiency and increased pressure drop. If the air flow is too high, the system may use excessive energy, and the filter bag may experience premature wear and tear.
The airflow rate is typically measured in cubic feet per minute (CFM), and it is important to match the airflow rate with the capacity of the dust collector. The capacity of the dust collector can be determined by the application’s dust generation rate, the concentration of dust in the air, and the volume of air to be filtered. By matching the airflow rate with the dust collector’s capacity, the system can operate effectively and efficiently.
Moreover, the filter bag frame’s design can affect the airflow rate and pressure drop. For example, some filter bag frames have a more open design, which can increase the airflow rate but may result in lower filtration efficiency. Other filter bag frames have a more restrictive design, which can decrease the airflow rate but may improve filtration efficiency.
Airflow is a critical factor to consider when selecting a filter bag frame for dust filters. By matching the airflow rate with the dust collector’s capacity and selecting a filter bag frame that balances airflow rate and filtration efficiency, the system can operate effectively and efficiently.
Operating Temperature

Choosing a filter bag frame material that can withstand high temperatures is essential to ensuring the longevity and efficiency of the filter bags. For example, filter bag frames made from stainless steel or other high-temperature alloys are suitable for high-temperature applications. The temperature of the gas stream being filtered can have a significant impact on the filter bag’s performance and durability.
High-temperature applications, such as those found in the cement and power generation industries, require filter bag frames that can withstand extreme temperatures. For these applications, filter bag frames made of high-temperature resistant materials such as ceramic, fiberglass, or PTFE may be required. These materials have excellent thermal stability and can resist temperatures up to 500°C or higher.
Conversely, low-temperature applications may not require such high-temperature resistant filter bag frames. In these applications, filter bag frames made of materials such as polyester or polypropylene may be suitable. These materials have a lower thermal stability but are more cost-effective and can withstand temperatures up to 100°C or 120°C.
The operating temperature can also affect the choice of filter bag frame design. For example, in high-temperature applications, filter bag frames with internal metal support structures may be required to maintain the shape and integrity of the bag at high temperatures. In contrast, filter bag frames for low-temperature applications may not require internal support structures.
Operating temperature is an essential factor to consider when selecting a filter bag frame for dust filters. By choosing a filter bag frame that can withstand the temperature of the gas stream being filtered, the system can operate efficiently and effectively, and the filter bag’s lifespan can be maximized.
Maintenance Requirements
Maintenance requirements are also an important factor to consider when selecting a filter bag frame for dust filters. Different types of filter bag frames require varying degrees of maintenance to keep them operating effectively.
Some filter bag frames, such as wire cages, are relatively easy to maintain and clean. These frames can be cleaned using compressed air, and the bag can be easily removed and replaced as needed. Other frames, such as those used in pulse-jet systems, require more complex maintenance procedures, such as periodic cleaning and replacing of the diaphragms.
Maintenance requirements can also vary based on the type of dust being filtered. For example, abrasive dusts can cause more wear and tear on filter bag frames, resulting in more frequent maintenance requirements. Similarly, corrosive dusts can cause corrosion on the filter bag frame and may require more frequent maintenance to prevent damage.
Another factor to consider is the frequency of bag replacement. Some filter bag frames may require more frequent replacement, which can increase the maintenance requirements of the system. In contrast, other frames may have a longer lifespan, reducing the frequency of replacement and maintenance.
It is essential to consider the maintenance requirements of the filter bag frame when selecting a solution for dust filtration. By choosing a filter bag frame that aligns with the system’s maintenance capabilities and requirements, the system can operate efficiently, effectively, and with minimal downtime due to maintenance needs.
Examples of how these factors affect filter bag frame selection

- A cement plant producing fine powders will require a tight weave filter bag and a wire cage frame that can withstand high temperatures.
- A chemical processing plant producing acidic or alkaline dust will require a filter bag frame made from corrosion-resistant materials such as fiberglass or stainless steel.
- A woodworking facility producing larger particles will require a more open weave filter bag and a self-cleaning frame to prevent clogs.
- A pharmaceutical facility producing highly regulated products will require a filter bag frame that is easy to maintain and clean to prevent contamination.
- A steel mill producing high-temperature gases will require a filter bag frame made from high-temperature alloys such as Inconel or Hastelloy.
Selecting the appropriate filter bag frame requires careful consideration of several factors such as the type of dust and particle size, chemical composition of the dust, airflow, operating temperature, and maintenance requirements. By understanding these factors and choosing the right filter bag frame solution, it is possible to maximize the durability and efficiency of dust filters while minimizing maintenance costs and downtime.
Conclusion

In conclusion, the durability of filter bags is crucial to maintain the effectiveness of dust filtration systems. We have explored the top filter bag frame solutions available in the market, including wire cages, self-cleaning, top load, bottom load, and pulse-jet frames, and their respective benefits and drawbacks.
When selecting a filter bag frame, it is important to consider several factors, such as the type of dust and particle size, the chemical composition of the dust, airflow, operating temperature, and maintenance requirements. By understanding these factors and their impact on filter bag frames, it is possible to select the optimal frame solution for your dust filtration needs.
Wire cages are an excellent option for general-purpose applications, while self-cleaning frames are ideal for high-volume dust filtration. Top load and bottom load frames are suitable for applications requiring easy access for maintenance, while pulse-jet frames are ideal for continuous operation.
Maximizing durability is critical for optimizing the lifespan and performance of your dust filtration system. Choosing the right filter bag frame solution can minimize maintenance requirements, reduce replacement costs, and extend the lifespan of your system.
We encourage you to take action and choose the right frame for your filter bag to maximize durability and ensure your system’s optimal performance. Consult with experts, evaluate the various options, and select the frame that best aligns with your needs and requirements.
Remember, selecting the right filter bag frame solution is a crucial investment in your dust filtration system’s effectiveness and longevity. Choose wisely and ensure the long-term efficiency of your system. Sofilt is the perfect choice for your filter bag frame needs.
We offer the most cost-effective and reliable solutions on the market, backed by decades of experience and an extensive network of suppliers. Contact us today to learn more about the perfect filter bag frame for your needs. We look forward to helping you maximize the durability of your dust filtration system.