Introduction

Industrial dust collectors play a crucial role in maintaining the health and safety of workers in various industries. These machines collect dust and other particulate matter, preventing them from being released into the air and causing harm to human health or the environment.
However, like any piece of machinery, dust collectors require regular maintenance and troubleshooting to ensure they operate at peak efficiency and prevent breakdowns. We will discuss in detail the maintenance and troubleshooting of industrial dust collectors, including their components, common problems, and best practices for upkeep.
Components of Industrial Dust Collectors
Before discussing maintenance and troubleshooting, it’s essential to understand the components of industrial dust collectors. While there are several types of dust collectors, they all share common parts that work together to capture and contain dust and other airborne particles.
Inlet and Ductwork
The inlet and ductwork are the entry points for dust and other airborne particles into the dust collector. Inlet configurations vary depending on the type of dust collector, and the ductwork connects the inlet to the main body of the collector. These components are responsible for the proper functioning of the dust collection system, which is essential for maintaining a safe and healthy working environment in many industries.
The inlet should be designed to provide a smooth and uniform flow of air to the dust collector. It should also be positioned in a way that minimizes the amount of turbulence in the air stream. This is because turbulence can cause the dust particles to become re-entrained in the air, reducing the efficiency of the dust collection system.
The ductwork is the network of pipes that carries the contaminated air from the inlet to the dust collector. The ductwork should be designed to provide a consistent and even flow of air to the dust collector. It should also be made of materials that are suitable for the type of dust being collected. For example, if the dust is abrasive, the ductwork should be made of materials that can withstand abrasion.
The design of the inlet and ductwork is crucial for the proper functioning of the dust collection system. If these components are poorly designed, they can cause problems such as excessive turbulence, which can reduce the efficiency of the system, or leaks, which can lead to a buildup of dust in the workplace.
Collector Body
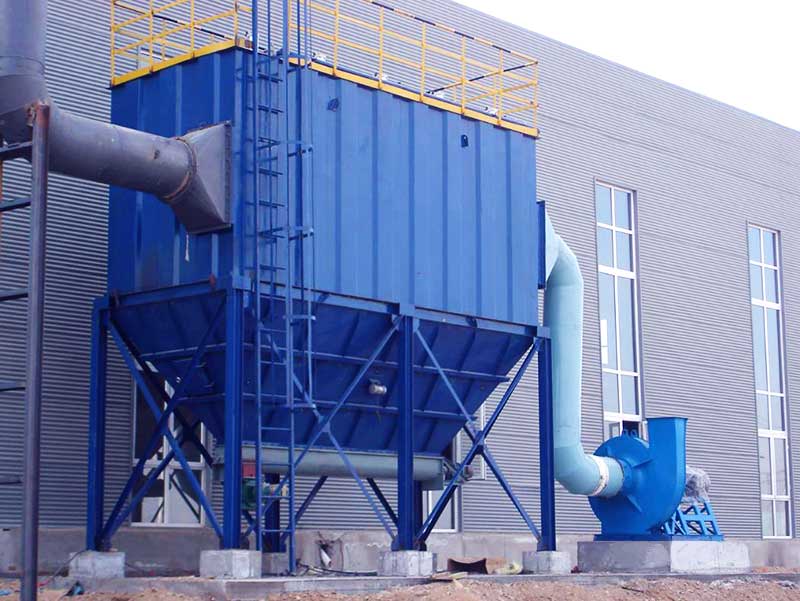
The collector body is the main housing unit of the dust collector, where the particulate matter is separated from the air. The collector body houses the filters, which capture the dust and prevent it from escaping into the environment. It is part of the dust collector that collects and stores the dust and other particulate matter that is removed from the contaminated air.
The collector body is typically a large, cylindrical container that is made of metal, such as steel or aluminum. The size of the collector body can vary depending on the application and the amount of dust that needs to be collected. In some cases, multiple collector bodies may be used to handle larger volumes of dust.
It is designed to provide a large surface area for the dust to settle on. This is typically achieved through the use of filter bags or cartridges that are suspended inside the collector body. The contaminated air is forced through the filter bags or cartridges, and the dust particles are trapped on the outside surface of the filter media.
Once the dust has been collected, it needs to be removed from the collector body. This is typically done through a discharge mechanism, such as a rotary valve or an auger, that moves the collected dust out of the collector body and into a storage container or bin.
The collector body plays a critical role in the overall efficiency and effectiveness of the dust collection system. If the collector body is not designed properly, it can lead to issues such as clogging of the filter bags or cartridges, which can reduce the efficiency of the system. It is also important to properly maintain the collector body to ensure that it is operating at peak efficiency and to prevent any safety hazards.
Filters
Filters are the heart of the dust collector, responsible for capturing and containing dust and other airborne particles. There are several types of filters, including fabric filters, pleated filters, cartridge filters, and bag filters. They are responsible for removing dust and other particulate matter from the contaminated air that is being collected. The choice of filter depends on the specific application and type of dust being collected.
Bag filters are typically made of a woven or felted fabric, while cartridge filters are made of a pleated paper or synthetic material. Pleated filters have a larger surface area than a bag or cartridge filters, allowing them to capture more dust and extending their lifespan.
The effectiveness of a filter depends on a number of factors, including the type of filter, the size and shape of the dust particles being collected, and the airflow through the filter. Filters that are not properly sized or designed for the specific application can become clogged or overloaded, reducing the efficiency of the dust collection system.
Proper maintenance of the filters is essential for ensuring the efficient and effective operation of the dust collector. This can include regular cleaning or replacement of the filters, as well as periodic inspections to check for any signs of wear or damage.
In addition to removing dust and other particulate matter, filters can also play a role in capturing hazardous materials or preventing them from being released into the environment. For example, HEPA filters are capable of capturing very small particles, including bacteria and viruses, making them an important component of air filtration systems in hospitals and other healthcare settings.
Cleaning System

The cleaning system is responsible for removing the collected dust from the filters, ensuring they remain effective at capturing dust. There are several types of cleaning systems, including pulse-jet, reverse air, and shaker systems.
The cleaning system can be divided into two main types: offline cleaning and online cleaning. Offline cleaning systems shut down the dust collector to clean the filters, while online cleaning systems clean the filters while the dust collector is still in operation.
Offline cleaning systems typically use mechanisms such as shaking or reverse airflow to remove accumulated dust from the filters. This process can be automated, with the cleaning system being programmed to activate at set intervals or when the pressure drop across the filter reaches a certain level.
Online cleaning systems use mechanisms such as pulse-jet or sonic cleaning to remove accumulated dust from the filters while the dust collector is still in operation. These systems can be programmed to clean the filters on a regular basis or can be set up to respond to changes in the pressure drop across the filter.
Proper design and maintenance of the cleaning system are critical for ensuring the efficient and effective operation of the dust collection system. If the cleaning system is not designed properly or is not maintained regularly, it can lead to issues such as clogging of the filters, reduced efficiency of the system, and safety hazards such as fires or explosions.
Discharge Mechanism
The discharge mechanism is the component responsible for removing the collected dust from the collector body and transferring it to a storage container or bin. Discharge mechanisms vary depending on the type of collector and may include rotary valves, screw conveyors, or other devices.
The most common types of discharge mechanisms include:
- Rotary valves
- screw conveyors
- pneumatic conveying systems
Rotary valves are the most commonly used discharge mechanism and consist of a rotating rotor that moves the collected dust out of the collector body and into a storage container or bin. Screw conveyors use a rotating screw to move the dust, while pneumatic conveying systems use air pressure to transfer the dust from the collector body to a storage container or bin.
The discharge mechanism must be properly designed and sized to handle the volume of dust being collected by the dust collector. If the discharge mechanism is undersized or improperly designed, it can lead to issues such as clogging, reduced efficiency, and safety hazards such as fires or explosions.
Proper maintenance of the discharge mechanism is also essential for ensuring the efficient and effective operation of the dust collector. This can include regular cleaning or replacement of the discharge mechanism components, as well as periodic inspections to check for any signs of wear or damage.
In addition to removing collected dust from the collector body, the discharge mechanism can also play a role in preventing the release of dust into the environment. For example, rotary valves can be fitted with seals or other mechanisms to prevent dust from leaking out during the transfer process.
Common Problems with Industrial Dust Collectors
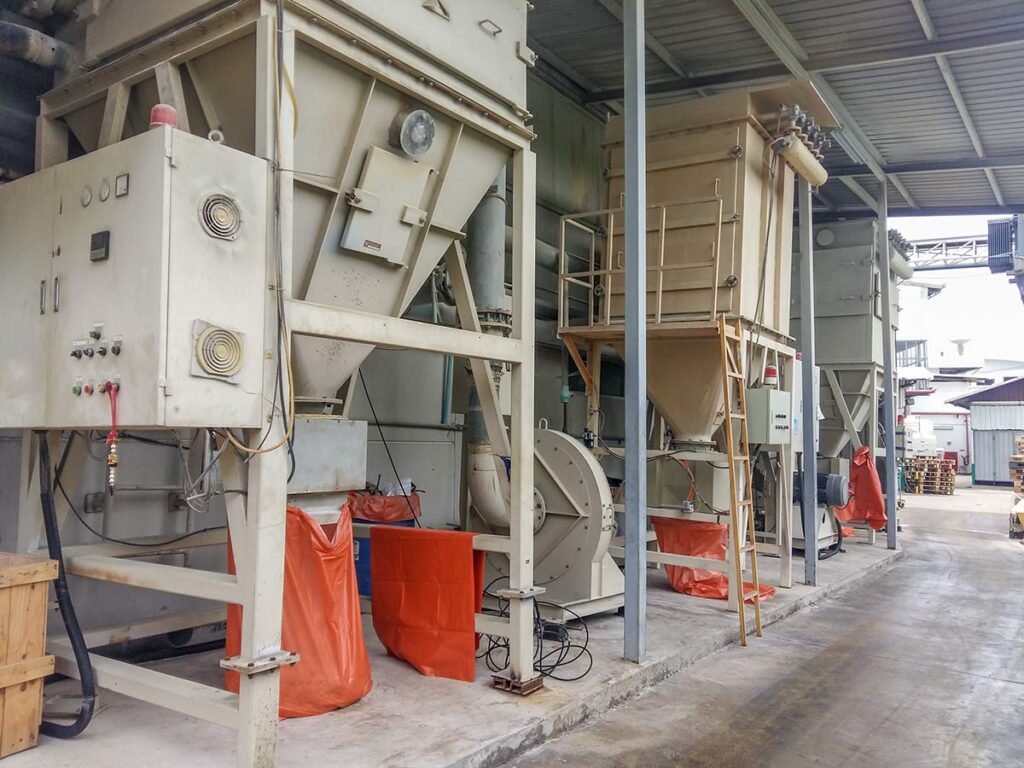
While dust collectors are designed to operate effectively and efficiently, several common problems can arise. Some of the most common problems include:
Poor Airflow
Poor airflow is a common problem with industrial dust collectors and can be caused by several factors. One cause is clogged filters, which restrict airflow and reduce the efficiency of the dust collector. Another cause is inadequate ductwork, which can lead to turbulence and uneven airflow or differential pressure. The size and layout of the dust collection system can also affect airflow, as an improperly sized or designed system can reduce the efficiency of the collector.
Dust Leakage
Dust leakage occurs when dust escapes from the collector and enters the workplace or the environment. Dust leakage can be caused by a variety of factors, including poorly fitting ductwork, compressed air pressure, damaged filters, and malfunctioning cleaning systems. The discharge mechanism can also play a role, as improperly designed or sized components can lead to dust leaking out during the transfer process. A poorly fitted ductwork can also lead to dust leakage.
Excessive Noise
Excessive noise can be a problem with dust collectors, especially in larger systems. The noise can be caused by several factors, including high airflow rates, turbulence in the ductwork, and malfunctioning cleaning systems. Turbulence in the ductwork can be caused by incorrect sizing or design, while malfunctioning cleaning systems can lead to increased noise due to vibration.
Malfunctioning Cleaning System
A malfunctioning cleaning system can lead to poor dust collection efficiency and reduced filter life. Malfunctioning cleaning systems can be caused by clogged or damaged nozzles, malfunctioning solenoids, and inadequate cleaning frequency. if the solenoids are not functioning correctly, the cleaning system may not be able to adequately clean the filters. Improperly sized or damaged nozzles can also reduce the cleaning efficiency of the system. In addition, improper nozzle selection or insufficient cleaning frequency can lead to inadequate filter cleaning and reduced dust collection efficiency
Safety Hazards
Safety hazards can arise from the use of dust collectors, including fires and explosions. Dust particles can accumulate in the collector and can become combustible if not removed. Fires and explosions can be caused by inadequate cleaning, damaged ductwork, or malfunctioning components. Regular maintenance and inspections can help to ensure that dust collectors are functioning safely.
Maintenance of Industrial Dust Collectors

Proper maintenance is crucial for the efficient and safe operation of industrial dust collectors. Regular maintenance can prevent breakdowns, improve performance, and extend the life of the collector. Some of the key maintenance tasks include:
Regular Inspections
Dust collector maintenance checklists are essential for identifying potential problems before they become serious. Inspections should include a visual check of the collector body, filters, cleaning system, ductwork, and discharge mechanism. Any damage or signs of wear should be addressed promptly to prevent further damage. If necessary, the collector should be shut down for repairs.
Filter Maintenance
Filters are a critical component of industrial dust collectors, and their maintenance is crucial for ensuring the efficient operation of the collector. The filters should be cleaned or replaced regularly, depending on the type of filter and the application. In some cases, filters may require cleaning on a daily basis, while in others, they may only need to be replaced once or twice a year. Regular filter maintenance can prevent clogging and prolong the life of the filters.
Cleaning System Maintenance
The cleaning system is responsible for removing the collected dust from the filters, and its maintenance is crucial for ensuring the efficient operation of the collector. The cleaning system should be inspected regularly for clogs, damage, or other issues.
Cleaning system nozzles should be cleaned or replaced as needed, and the system should be checked for proper operation. Inadequate cleaning frequency or malfunctioning cleaning systems can lead to reduced filter life and poor dust collection efficiency.
Ductwork Maintenance
Ductwork is responsible for transporting dust and other particulate matter from the inlet to the collector body. Proper ductwork design and maintenance are crucial for ensuring efficient dust collection.
Ductwork should be inspected regularly for damage or leaks, and any issues should be addressed promptly to prevent dust leakage or poor airflow. Proper ductwork design can also reduce turbulence and promote even airflow, improving dust collection efficiency.
Discharge Mechanism Maintenance
The discharge mechanism is responsible for removing the collected dust from the collector body. Regular maintenance of the discharge mechanism can prevent clogging and ensure proper operation.
The discharge mechanism should be inspected regularly for damage or wear, and any issues should be addressed promptly. Proper discharge mechanism maintenance can prevent dust buildup, reduce downtime, and improve the efficiency of the collector.
Troubleshooting Industrial Dust Collectors
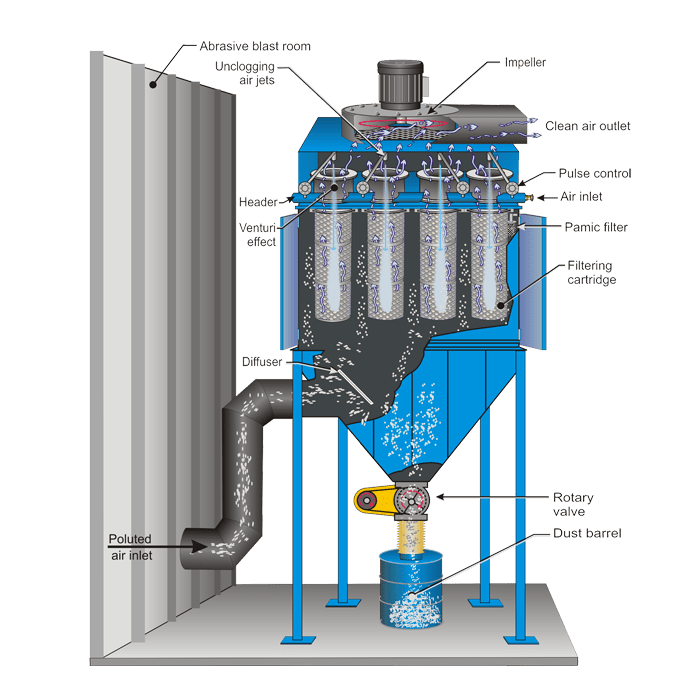
When problems arise with industrial dust collectors, troubleshooting can help identify and resolve the issue. With careful diagnosis and follow-up maintenance, most issues can be corrected quickly. Some of the most common troubleshooting steps include:
Identify the Problem
The first step in troubleshooting an industrial dust collector is to identify the problem. Common problems include poor airflow, dust leakage, excessive noise, and malfunctioning cleaning systems. These problems can be caused by a variety of factors, such as clogged filters, worn or damaged components, improper ductwork design, and inadequate cleaning frequency.
Inspect the Collector
Once the problem is identified, the collector should be inspected to determine the cause of the issue. The inspection should include a visual check of the collector body, filters, cleaning system, ductwork, and discharge mechanism. Any damage or signs of wear should be addressed promptly to prevent further damage and ensure proper operation.
Check Filters and Cleaning System
If poor airflow or dust leakage is the issue, the filters and cleaning system should be checked for clogs, damage, or malfunction. The filters may need to be cleaned or replaced, and the cleaning system may require maintenance or repair.
Adjust Ductwork
Improper ductwork design can lead to poor airflow or dust leakage, so the ducts should be inspected to ensure they are installed correctly. If necessary, the ducts can be adjusted to reduce turbulence and promote even airflow.
Check Ductwork
If poor airflow or dust leakage is the issue, the ductwork should be checked for damage or leaks. Any issues should be addressed promptly to prevent dust leakage or poor airflow. The ducts should also be inspected to ensure they are installed correctly and do not obstruct airflow.
Check the Discharge Mechanism
If the discharge mechanism is causing the issue, it should be checked for clogs, damage, or malfunction. Proper maintenance and cleaning of the discharge mechanism can prevent dust buildup, reduce downtime, and improve the efficiency of the collector.
Best Practices for Industrial Dust Collector Maintenance

To ensure the efficient and safe operation of industrial dust collectors, several best practices should be followed:
Regular Maintenance Schedule
A regular maintenance schedule should be established and followed to prevent breakdowns, improve performance, and extend the life of the collector. Regular inspections, filter maintenance, cleaning system maintenance, ductwork maintenance, and discharge mechanism maintenance should be part of the maintenance schedule.
Proper Training
Personnel responsible for maintaining and troubleshooting industrial dust collectors should receive proper training to ensure they understand the equipment, its operation, and maintenance requirements.
Proper Equipment Selection
Proper equipment selection is critical for ensuring efficient dust collection. The equipment should be selected based on the type of dust, its properties, and its application.
Proper Installation
Proper installation of industrial dust collectors is crucial for efficient and safe operation. The collector should be installed in a suitable location, and ductwork should be properly designed and installed to ensure efficient dust collection.
Safety Precautions
Industrial dust collectors can pose safety hazards if not properly maintained and operated. Proper safety precautions should be taken, including wearing appropriate personal protective equipment (PPE), following lockout/tag-out procedures, and ensuring proper grounding of electrical equipment.
Conclusion

Industrial dust collectors play a critical role in maintaining clean and safe working environments in various industries. Proper maintenance and troubleshooting of these collectors are crucial for ensuring their efficient operation and preventing safety hazards.
Regular maintenance of industrial dust collectors, including filter maintenance, cleaning system maintenance, ductwork maintenance, and discharge mechanism maintenance, can prevent breakdowns, improve performance, and extend the life of the collector.
Buying quality and reliable equipment, proper training of personnel responsible for maintenance and troubleshooting, and following safety precautions can also help ensure the efficient operation of industrial dust collectors. With the proper maintenance and troubleshooting procedures, industrial dust collectors can provide a clean and safe working environment for many years.
The end goal of all maintenance and troubleshooting procedures should be to ensure the efficient operation of the dust collector, prevent safety hazards, and maintain a clean and safe working environment. That is why here at Sofilt, we pay a lot of attention to the quality of both the fabric for the filter bags and the dust collector equipment.
All our products are designed and manufactured to the highest quality standards for durability, efficiency, safety, and ease of use. We strive to provide our customers with the best possible products and services to help ensure their operations are running smoothly.
We understand how important it is for industrial dust collectors to be properly maintained and troubleshot, which is why we take great care in ensuring the quality of our products. Our team of experts is always available to answer any questions or concerns you may have, and we can provide support with troubleshooting, maintenance, and installation. Contact us today to learn more about our dust collector products and services.