Introduction

A baghouse dust collector is an essential piece of equipment for many industrial and commercial operations, as it helps to remove dust and other particulate matter from the air. However, to ensure that a baghouse dust collector is operating at peak efficiency and prolongs its life, regular maintenance is required.
This article will discuss the key maintenance procedures that should be performed to optimize the operations of a baghouse dust collector. By following these procedures, a baghouse dust collector can be kept in good working order, ensuring that it is always operating safely and efficiently.
Filter Media Inspection and Replacement
Filter media inspection and replacement is a critical maintenance procedure for dust collectors to ensure optimal performance and prolong the life of the equipment. The filter media, also known as the filter element or bag, is the component of the dust collector that captures and retains the dust particles. Worn or damaged filter media can lead to increased pressure drop and decreased collection efficiency.
During the filter media inspection, the condition of the filter media should be evaluated for signs of wear, damage, and clogging. The filter media should be inspected for holes, tears, or other forms of damage that can affect the filter’s ability to capture dust particles. The filter media should also be inspected for clogging, which can cause an increase in pressure drop and a decrease in airflow.
If the filter media is found to be damaged or clogged, it should be replaced as soon as possible to restore the optimal performance of the dust collector. The replacement filter media should be of the same type and size as the original filter media to ensure a proper fit and optimal performance.
It is also important to note that filter media replacement intervals will vary depending on the specific dust collector system and the type of dust being collected. For some systems, the filter media may need to be replaced more frequently than others due to the abrasiveness or toxicity of the dust.
In addition to replacing the filter media, it’s also recommended to shake or pulse-jet the filter media to remove the dust that’s trapped in the filter media. This will help to prolong the life of the filter media and ensure optimal performance of the dust collector.
Regular filter media inspection and replacement are essential for optimal dust collector performance and for prolonging the life of the equipment. It’s important to have a schedule for the filter media inspection and replacement and follow it accordingly, to ensure the dust collector is always operating at its best.
Pulse-Jet Cleaning System Maintenance
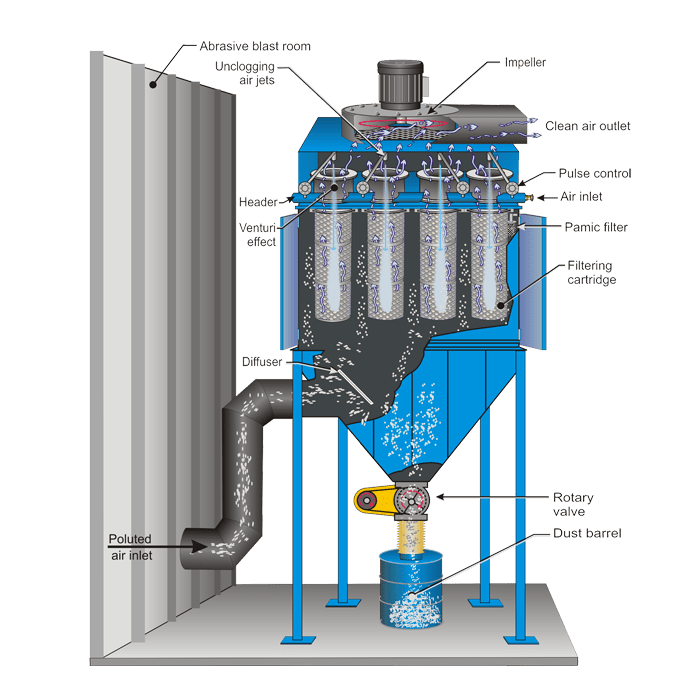
Pulse-jet cleaning systems are used to remove accumulated dust from filter media. Proper maintenance of these systems, including regular cleaning and replacement of worn parts, is necessary to ensure effective cleaning and prolong the life of the filter media.
Pulse-jet cleaning systems are commonly used in baghouse dust collectors to remove accumulated dust from filter media. These systems use pulses of compressed air to forcefully shake the filter bags, causing the collected dust to fall into the hopper for disposal. Proper maintenance of pulse-jet cleaning systems is essential for ensuring effective cleaning and prolonging the life of the filter media.
The following are key maintenance procedures for pulse-jet cleaning systems:
- Regular cleaning of the air supply lines: The air supply lines that supply compressed air to the pulse-jet cleaning system should be cleaned regularly to ensure proper operation. This can be done by blowing out the lines with compressed air, or by physically cleaning them with a brush or other cleaning tool.
- Inspection and replacement of worn parts: The nozzles, diaphragms, and other moving parts of the pulse-jet cleaning system should be inspected regularly for wear and damage. Worn or damaged parts should be replaced as soon as possible to ensure the proper operation of the cleaning system.
- Proper alignment and adjustment of the nozzles: The nozzles of the pulse-jet cleaning system should be properly aligned and adjusted to ensure that the compressed air pulses are directed at the filter bags in the most effective way. Improper alignment or adjustment can lead to decreased cleaning efficiency and increased wear on the filter bags.
- Monitoring and recording of compressed air pressure and flow: The compressed air pressure and flow used for the pulse-jet cleaning system should be monitored and recorded regularly. This will help to identify any issues with the air supply or the cleaning system itself and ensure that the system is operating at optimal levels.
- Regularly check for leaks: Leaks in the compressed air supply lines in the nozzles can lead to decreased cleaning efficiency and increased operating costs. Regularly checking for leaks and fixing them as soon as they are identified is important for maintaining the optimal performance of the cleaning system.
The maintenance of the pulse-jet cleaning system is very important in ensuring the effective cleaning of the filter bags and prolonging the life of the filter media. It’s important to have a schedule for the pulse-jet cleaning system maintenance and follow it accordingly, to ensure that the dust collector is always operating at its best.
Leak Detection and Repair

Leak detection and repair is an important maintenance procedure for dust collectors to ensure optimal performance and prolong the life of the equipment. Leaks in the dust collector system can cause decreased collection efficiency and increased operating costs.
The key steps for leak detection and repair include:
- Conducting Regular Inspections: Regular inspections of the dust collector system, including all components and connections, should be conducted to identify any potential leaks. Visual inspections, as well as pressure drop measurements, can be used to identify leaks.
- Using Leak Detection Tools: There are several specialized tools available for detecting leaks in dust collector systems, such as ultrasonic leak detectors, infrared cameras, and pressure decay testers. These tools can detect leaks that may not be visible during a visual inspection.
- Identifying the Location of Leaks: Once a leak is detected, the location of the leak should be identified as precisely as possible. This will aid in determining the cause of the leak and the appropriate repair method.
- Repairing the Leak: Once the location of the leak is identified, the appropriate repair method should be determined. This may include patching or replacing a section of the ductwork, replacing a damaged gasket, or welding a crack in a metal component.
- Testing the repair: After the repair is complete, the system should be tested to ensure that the leak has been effectively repaired and that the system is operating properly. This can be done by conducting a pressure drop test or by monitoring the system’s performance over time.
It’s important to note that leaks in the dust collector system can occur due to various reasons such as improper installation, corrosion, or damage due to wear and tear. Regular inspections and repairs can help to minimize the risk of leaks and ensure optimal performance of the dust collector system. Always have a schedule for leak detection and repair, and follow it accordingly, to ensure that the dust collector is always operating at its best.
Hopper and Ductwork Inspection
The hopper and ductwork of a dust collector can become clogged with accumulated dust, leading to decreased airflow and increased pressure drop. Regular inspection and cleaning of these components are necessary to maintain optimal performance.
Hopper and ductwork inspection is an important maintenance procedure for optimizing the operations of a baghouse dust collector. The hopper, which is the bottom part of the dust collector where the collected dust is discharged, should be inspected for any build-up of material that could impede the flow of dust. The material buildup inside the hopper can cause the dust collector to work less efficiently, can cause the filter bags to wear out more quickly, and can even cause the dust collector to malfunction. To prevent these issues, the hopper should be inspected regularly, and any build-up of material should be removed.
Ductwork, the piping system that connects the various components of the dust collector, should also be inspected for any blockages or leaks. The ductwork is responsible for carrying the dust-laden air from the source of the dust to the dust collector, and then from the dust collector to the clean air discharge point. If the ductwork is clogged or leaking, the dust collector will not be able to effectively remove dust from the air. To prevent this, the ductwork should be inspected regularly for any blockages or leaks, and any issues should be promptly repaired.
Another important step in hopper and ductwork inspection is to check for proper airflow. The airflow through the hopper and ductwork is critical to the performance of the dust collector. If the airflow is restricted, the dust collector will not be able to effectively remove dust from the air. To check for proper airflow, the hopper and ductwork should be inspected for any areas where the airflow is restricted. This could include areas where the ductwork is pinched or where the hopper is partially blocked.
To ensure that the dust collector is operating at peak efficiency, it is important to have a regular inspection schedule in place. This schedule should include regular inspections of the hopper and ductwork, as well as regular cleaning of the hopper and ductwork. By following this schedule, you can prolong the life of the filter bags, improve the efficiency of the dust collector, and ensure that the dust collector is always operating safely.
Hopper and ductwork inspection is a key maintenance procedure for optimizing the operations of a baghouse dust collector and it should be performed regularly to ensure that the dust collector is operating at peak efficiency, prolong the life of the bags, and ensure the safety of the dust collector.
Electrical and Mechanical Maintenance

Regular maintenance of the dust collector’s electrical and mechanical components, such as motors, fans, and belts, is necessary to ensure proper operation and prolong the life of the equipment.
Electrical maintenance includes tasks such as inspecting and cleaning electrical components, troubleshooting and repairing electrical issues and ensuring that all electrical connections are secure. Some important electrical components to inspect include the motor, control panel, and electrical wiring.
The motor should be checked for proper operation, and the control panel should be checked for any error messages or other indicators of a problem. The electrical wiring should be inspected for any frayed or damaged wires, and all connections should be checked to ensure that they are secure.
Mechanical maintenance includes tasks such as inspecting and cleaning mechanical components, troubleshooting and repairing mechanical issues and ensuring that all mechanical connections are secure. Some important mechanical components to inspect include the fan, filter bags, and support cage. The fan should be checked for proper operation, and the filter bags should be inspected for wear and tear. The support cage, which holds the filter bags in place, should also be inspected for any signs of damage or wear.
The mechanical components of the dust collector system such as the fan drive and the bag cleaning system should be regularly checked for proper operation. If the fan drive is not operating correctly, it can cause the fan to run at the wrong speed and can lead to poor dust collection. The bag cleaning system is responsible for removing dust from the filter bags, so if it is not working properly, the filter bags will not be effectively cleaned and the dust collector will not be able to remove dust from the air.
Regularly scheduled maintenance is crucial to keep the dust collector in good working order. A maintenance schedule should be established to ensure that all electrical and mechanical components are inspected and serviced on a regular basis. This will help to prolong the life of the dust collector and ensure that it is always operating at peak efficiency.
Overall, Electrical and Mechanical maintenance is a key maintenance procedure for optimizing the operations of a baghouse dust collector. Regularly scheduled maintenance, including inspections, cleaning, and repairs, ensures that all electrical and mechanical components are in good working order, prolongs the life of the dust collector, and ensures that the dust collector is always operating at peak efficiency.
Regular inspections
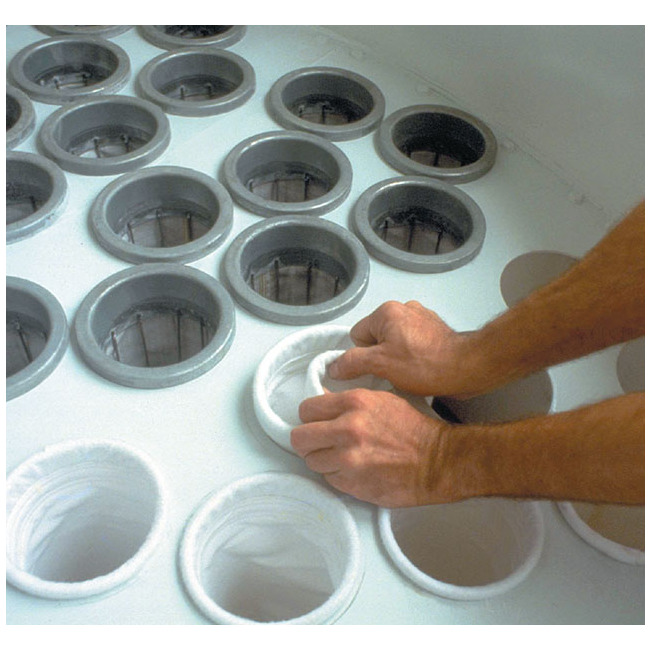
Regular inspections of the entire dust collector system, including all components and connections, are necessary to identify and address any potential issues before they become major problems. These inspections are important for identifying potential issues with the dust collector before they become major problems.
One of the main components of regular inspections is a visual inspection. This involves physically inspecting the dust collector and its components to identify any signs of wear or damage. This includes inspecting the filter bags, the support cage, the fan, and other mechanical and electrical components. If any issues are identified during the visual inspection, they should be addressed promptly to prevent further damage or to fix the problem.
Another important aspect of regular inspections is the measurement of various parameters such as the airflow rate, pressure drop, and the performance of the dust collector. Airflow rate is the amount of air that is flowing through the dust collector, and pressure drop is the difference in pressure between the inlet and outlet of the dust collector. Measuring these parameters can help to identify any issues with the dust collector’s performance, such as clogs or leaks in the ductwork, or issues with the fan.
Regular inspections also include monitoring the dust emissions levels. The emissions should be monitored to ensure that they are within the acceptable levels set by the regulatory bodies. This includes monitoring the dust emissions levels at the inlet and outlet of the dust collector, as well as monitoring the emissions levels at the stack or discharge point.
Regular inspections also include baghouse cleaning. This includes cleaning the filter bags, the support cage, and other components of the dust collector. Cleaning should be done on a regular schedule to ensure that the dust collector is always operating at peak efficiency.
Regular inspections help to identify potential issues with the dust collector before they become major problems, monitor the dust emissions levels, measure various parameters, and keep the dust collector in good working order. Having a regular inspection schedule in place, and following it, is important to ensure that the dust collector is always operating safely and efficiently.
Monitoring and Recording Data
Regular monitoring and recording of key performance data, such as pressure drop and airflow, can help identify potential issues and track progress over time. This is because it helps to identify any issues with the dust collector before they become major problems, and it also helps to track the performance of the dust collector over time.
One of the key data points that should be monitored and recorded is the pressure drop across the dust collector. Pressure drop is the difference in pressure between the inlet and outlet of the dust collector, and it is an important indicator of the dust collector’s performance. If the pressure drop is too high, it can indicate that there is a problem with the dust collector, such as clogs in the ductwork or issues with the fan.
Another important data point that should be monitored and recorded is the airflow rate. The airflow rate is the amount of air that is flowing through the dust collector, and it is an important indicator of the dust collector’s performance. If the airflow rate is too low, it can indicate that there is a problem with the dust collector, such as clogs in the ductwork or issues with the fan.
Another key data point is the dust emissions levels. The dust emissions levels should be monitored and recorded at the inlet and outlet of the dust collector, as well as at the stack or discharge point. This will help to ensure that the dust collector is operating within the acceptable levels set by the regulatory bodies.
Another important aspect of monitoring and recording data is tracking the filter bags life and replacement. This helps to keep track of the filter bags’ age and use, and to know when to replace them, in order to maintain the dust collector’s performance level.
In general, monitoring and recording data is a key maintenance procedure for optimizing the operations of a baghouse dust collector. It helps to identify any issues with the dust collector before they become major problems, and it also helps to track the performance of the dust collector over time. By monitoring and recording data, it will be possible to make informed decisions about the maintenance and operation of the dust collector and ensure that it is always operating at peak efficiency.
Safety and Compliance
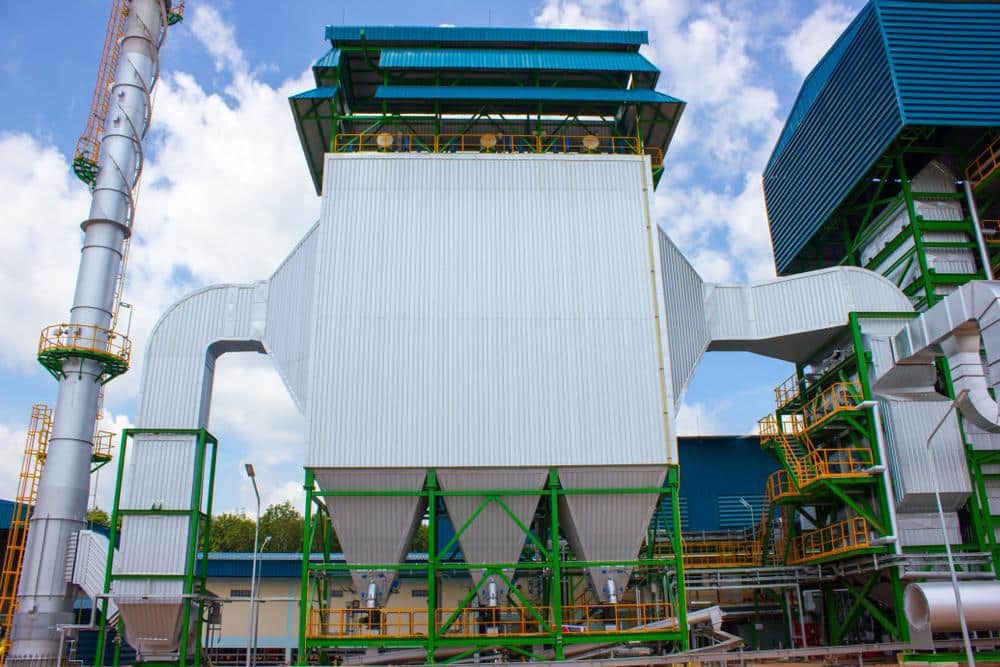
Dust collectors must be maintained to ensure compliance with relevant safety and environmental regulations, and also to ensure that the equipment is operating safely for the workers.
Overall, regular maintenance and inspections are essential for optimal dust collector performance and prolonging the life of the equipment.
These procedures are important for ensuring that the dust collector is operating safely and that it is in compliance with all relevant regulations and industry standards.
One of the key aspects of safety and compliance is ensuring that the dust collector is designed and constructed in accordance with industry safety standards. This includes ensuring that the dust collector is designed to withstand the specific operating conditions and that it is constructed with materials that are appropriate for the type of dust being collected.
Another important aspect of safety and compliance is the regular inspection of the dust collector to ensure that it is in good working order. This includes inspecting the filter bags, the support cage, the fan, and other mechanical and electrical components. If any issues are identified during the inspection, they should be addressed promptly to prevent further damage or to fix the problem.
Another important aspect of safety and compliance is ensuring that the dust collector is in compliance with all relevant regulations and industry standards. This includes ensuring that the dust collector is operating within the acceptable levels set by the regulatory bodies for dust emissions and that it is in compliance with OSHA regulations for workplace safety. Regular monitoring of dust emissions and compliance with OSHA regulations will help to keep the dust collector in good working order.
A critical aspect of safety and compliance is having proper training for the operators and maintenance personnel to ensure that they are aware of the potential hazards associated with the operation and maintenance of the dust collector and know how to properly handle and use the equipment. Regular training and retraining, of the operators and maintenance personnel will help to ensure that the dust collector is being operated and maintained safely.
Safety and Compliance is a key maintenance procedures for optimizing the operations of a baghouse dust collector. Ensuring that the dust collector is designed and constructed to meet safety standards, regular inspection, monitoring, compliance with regulations and industry standards, and proper training for the operators and maintenance personnel will help to ensure that the dust collector is operating safely and in compliance with all relevant regulations and industry standards.
Conclusion

The purpose of a dust collector is to remove dangerous particulate matter from the air, reduce workplace hazards, and ensure compliance with safety and environmental regulations. Regular maintenance and inspections are essential for optimal performance and to prolong the life of the equipment. By conducting regular maintenance procedures such as inspecting the filter bags, support cage, fan, electrical components and monitoring emissions levels, and ensuring proper training and compliance with regulations, a baghouse dust collector can remain safe and in optimal working order.
In summary, it is essential to maintain a regular maintenance schedule for a baghouse dust collector in order to ensure safety, compliance with applicable regulations, and optimal performance. Proper inspection, monitoring, and training of personnel will help to ensure the dust collector is operating safely and in compliance with all applicable regulations.
This article has provided an overview of the importance of safety, compliance regulation and regular maintenance for baghouse dust collectors. It is important for operators, maintenance personnel, and other stakeholders to understand the key aspects of safety, compliance and regular maintenance in order to ensure that the dust collector is in optimal working order and is operating safely.
By following these guidelines, operators can rest assured that their baghouse dust collector is operating safely and in compliance with all applicable regulations. For any more inquiries on the dust collectors and their components, get in touch with Sofilt engineers to get first-hand advice. With our expertise and industry insights, we can ensure your dust collector remains safe, compliant, and operational.