Introduction

A cartridge dust collector is a type of air-cleaning system that is used to remove dust and other particulate matter from the air. These systems are typically used in industrial settings, such as factories and workshops, where large amounts of dust and debris are produced. The basic principle of a cartridge dust collector is that it captures dust and debris on a filter media and then periodically cleans the filter media to remove the collected dust and debris.
The process of capturing and cleaning the dust and debris is accomplished through a combination of mechanical and pneumatic systems. In this article, we will discuss in detail the various components and processes involved in a cartridge dust collector and how they work together to effectively remove dust and debris from the air.
The working of a dust collector
Components of a cartridge dust collector
Properly installing filter bags in equipment can help prevent damage from vibration or improper alignment, which can extend their lifespan. It involves ensuring that the filter bags are properly installed in the equipment and are not exposed to any damage from vibration or improper alignment.
When installing filter bags, you should make sure they are securely fastened to the equipment. This can be done by using a metal cage or other support structure to hold the filter bag in place. A filter bag cage can help prevent the filter bag from collapsing and can help to distribute the weight of the filter bag more evenly, which can help to extend its lifespan.
Another important aspect of proper installation is making sure that the filter bag is properly aligned with the equipment. This includes making sure that the filter bag is centered in the equipment and that the inlet and outlet ports are properly aligned to ensure that the liquid or gas flows through the filter bag correctly.
Improper alignment can cause the filter bag to wear unevenly, or can cause the filter bag to collapse, which can shorten its lifespan. The filter bags should be installed in such a way that it should be easily removable for cleaning or replacement. Ensure that the filter bags are not exposed to any damage from vibration. This can be done by installing vibration dampers or other types of isolation devices to reduce the amount of vibration that the filter bags are exposed to. Vibration can cause the filter bag to wear out more quickly, so it’s important to minimize it as much as possible.
The functions of a cartridge dust collector are accomplished by several different components. These components include:
1. Filter media

The filter media is the most important component of a cartridge dust collector as it is responsible for capturing particulate matter from the air. It typically consists of a synthetic fabric or felt material that is shaped into cylindrical cartridges. The filter media is designed to be highly efficient at capturing particulate matter, while also being durable and long-lasting.
The filter media is designed to be highly efficient at capturing particulate matter, while also being durable and long-lasting. The filter media is typically made of synthetic fibers such as polyester, polypropylene, or a blend of these materials. These fibers are woven or felted into a fabric or felt material. The filter media can also be made of natural fibers such as cotton or cellulose. The filter media is then shaped into cylindrical cartridges and installed in the dust collector.
The filter media is designed to be highly efficient at capturing particulate matter, while also being durable and long-lasting. It is made of synthetic fibers such as polyester, polypropylene, or a blend of these materials. These fibers are woven or felted into a fabric or felt material. The filter media can also be made of natural fibers such as cotton or cellulose. It is then shaped into cylindrical cartridges and installed in the dust collector.
The filter media is designed with a certain level of porosity, which allows air to flow through the media while capturing particulate matter. The fiber diameter, the fiber density, and the thickness of the media determine the porosity of the filter media. A filter media with a higher fiber density and smaller fiber diameter will have a higher porosity, which will result in a higher airflow rate and a lower pressure drop.
The filter media is also designed to be durable and long-lasting. The filter media is typically treated with a coating or finish that makes it resistant to abrasion and chemicals. This helps to prolong the life of the filter media and reduce the need for frequent replacement.
2. Pulse-jet cleaning system
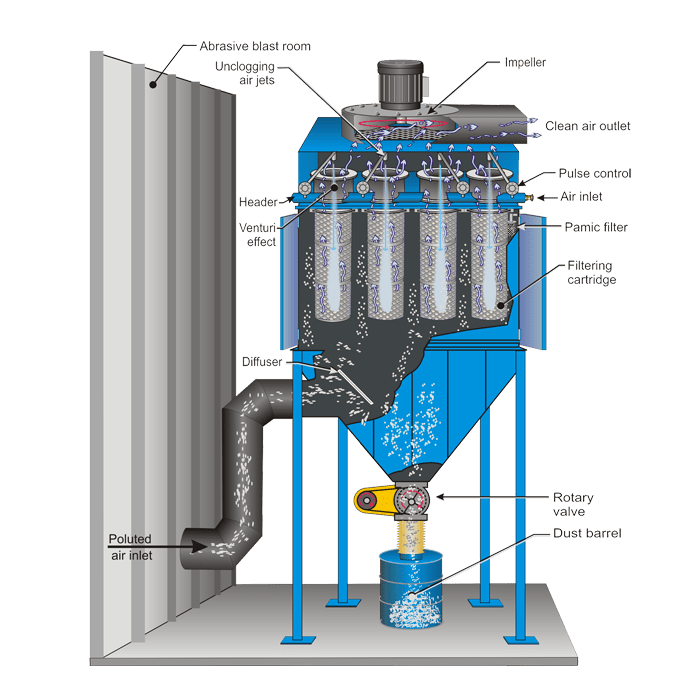
The pulse jet cleaning system is a component of a cartridge dust collector that is responsible for removing collected particulate matter from the filter media. It works by introducing a burst of compressed air into the filter media, which causes the filter media to vibrate and release the collected particulate matter. The pulse jet cleaning system is essential for maintaining the performance of a cartridge dust collector.
The pulse jet cleaning system typically consists of a series of diaphragm valves and a compressed air supply. The diaphragm valves are located at the base of each filter cartridge and are controlled by a timer or a pressure differential sensor. When a pulse of compressed air is introduced into the filter media, the diaphragm valves open, allowing the compressed air to enter the filter media. The compressed air causes the filter media to vibrate and release the collected particulate matter. The released particulate matter is then collected in a hopper and disposed of properly.
The pulse jet cleaning system is designed to be highly efficient and automatic. The cleaning process is typically triggered by a timer or a pressure differential sensor, which ensures that the filter media is cleaned at regular intervals. It is also designed to be gentle, so as not to damage the filter media.
The pulse jet cleaning system is also designed to be low maintenance. The diaphragm valves are typically made of durable materials and are designed to last for a long time. The compressed air supply is also designed to be low maintenance, as it only needs to be refilled with compressed air occasionally.
3. Fan or blower
The fan or blower is a component of a cartridge dust collector that is responsible for creating the airflow that pulls contaminated air into the dust collector and pushes the cleaned air out. It is considered one of the most important components in the dust collector system as it determines the airflow rate and pressure drop, which are essential for the dust collector to function properly.
The fan or blower is located at the clean air side of the dust collector and can be either centrifugal or axial type. The centrifugal fan uses an impeller with radial blades to move the air, while the axial fan uses a propeller-like design to move the air. The choice of fan type depends on the specific application and the required airflow rate.
The fan or blower is typically driven by an electric motor and is connected to the dust collector by ductwork. The fan or blower can be designed to be either direct or belt-driven. Direct-drive fans are more efficient and require less maintenance, but are typically more expensive. Belt-driven fans are less expensive but require more maintenance.
The fan or blower is typically designed to be highly efficient and low maintenance. The fan or blower must be able to produce the necessary airflow rate and pressure drop to effectively pull contaminated air into the dust collector and push the cleaned air out. It should also be designed to operate efficiently and to last for a long time with minimal maintenance.
4. Inlet
The inlet, also known as the dirty air inlet, is a component of a cartridge dust collector that is responsible for bringing contaminated air into the dust collector for filtration. It is typically located at the front of the dust collector and is connected to the fan or blower by ductwork. The inlet is designed to evenly distribute the contaminated air across the filter cartridges for more efficient filtration.
The inlet can be designed in a variety of ways depending on the specific application and the type of dust being collected. Some inlets are designed to be adjustable, allowing the user to change the airflow rate and distribution as needed. Other inlets are designed to be fixed, with the airflow rate and distribution determined by the design of the dust collector.
The inlet is typically designed to be low maintenance and to last for a long time. The inlet should be designed to be durable and resistant to wear and tear. It also should be easy to access for cleaning and maintenance.
The inlet is crucial for the proper functioning and maintenance of the dust collector as it is responsible for bringing contaminated air into the dust collector for filtration. The inlet needs to be designed to evenly distribute the contaminated air across the filter cartridges for more efficient filtration. It also needs to be designed to be low maintenance and to last for a long time. The inlet plays a significant role in the dust collector’s ability to filter and trap dust particles effectively.
5. Outlet
The outlet, also known as the clean air outlet, is a component of a cartridge dust collector that is responsible for releasing the cleaned air back into the atmosphere. The outlet is located at the back of the dust collector and is connected to the fan or blower by ductwork. It is designed to release the cleaned air at a safe distance from the dust collector to prevent recirculation of the contaminated air.
The outlet can also be designed in a variety of ways depending on the specific application and the type of dust being collected. Some outlets are adjustable, thus allowing the user to change the airflow rate and distribution as needed. Other outlets are designed to be fixed, with the airflow rate and distribution determined by the design of the dust collector.
The outlet is also made to be of low maintenance and to last for a long time. It should be durable and resistant to wear and tear. It also should be easy to access for cleaning and maintenance.
The outlet is important for the proper functioning and maintenance of the dust collector as it is responsible for releasing the cleaned air back into the atmosphere. It should be designed to release the cleaned air at a safe distance from the dust collector to prevent recirculation of the contaminated air. The outlet also plays a role in the dust collector’s ability to filter and trap dust particles effectively.
6. Collection hopper

ion hoppers are designed to be removable, allowing the user to easily empty the collected dust and debris. Other collection hoppers are designed to be fixed, with the collected dust and debris being removed by a conveyor system.
The collection hopper is typically designed to be low maintenance and to last for a long time. It should be designed to be durable and resistant to wear and tear, and also be easy to access for cleaning and maintenance. The collection hopper also should be designed to prevent dust and debris from escaping during the removal process.
The collection hopper is essential for the proper functioning and maintenance of the dust collector as it is responsible for collecting and storing the dust and debris that is filtered out of the contaminated air. The collection hopper needs to be designed to be low maintenance and to last for a long time. The collection hopper also plays a role in the dust collector’s ability to filter and trap dust particles effectively. It should be designed to be durable and resistant to wear and tear, and also be easy to access for cleaning and maintenance.
7. Control panel
The control panel is a component of a cartridge dust collector that is responsible for controlling and monitoring the various functions of the dust collector including the fan speed, pulse jet cleaning intervals, and alarm settings. The control panel is typically located at the front of the dust collector and includes various switches, buttons, and displays that allow the user to control the dust collector’s operation.
The control panel typically includes a power switch that turns the dust collector on and off, a filter cleaning switch that initiates the pulse jet cleaning system, a fan speed control that allows the user to adjust the fan or blower’s speed, and a display that shows the status of the dust collector’s operation. Some control panels also include additional features such as alarms and automatic controls that can be programmed to perform specific tasks.
It is designed in a user-friendly and easy-to-use manner. It is clearly labeled and has simple, intuitive controls that make it easy for the operator to understand and operate the dust collector. The control panel also should be designed to be durable and resistant to wear and tear.
8. Pre-filters or after-filters
These optional components provide additional filtration and improve the overall performance of the dust collector. They can be added to a cartridge dust collector to improve its overall performance. These filters are located either before or after the main filter cartridges and are designed to capture larger particles of dust and debris that may not be effectively captured by the main filters.
Pre-filters are located before the main filter cartridges and are designed to capture larger particles of dust and debris before they reach the main filters. This helps to extend the life of the main filters by reducing the amount of dust and debris that they need to capture. Pre-filters can be made from a variety of materials, such as mesh, metal, or synthetic fibers, and can be cleaned or replaced as needed.
After-filters, on the other hand, are located after the main filter cartridges and are designed to capture any remaining dust particles that may not have been effectively captured by the main filters. This helps to ensure that the air being released from the dust collector is as clean as possible. After-filters can be made from a variety of materials, such as activated carbon, HEPA filters, or ULPA filters, and can be cleaned or replaced as needed.
Pre-filters and after-filters are important for the proper functioning and maintenance of the dust collector as they help to improve the overall performance of the dust collector by capturing larger particles of dust and debris that may not be effectively captured by the main filters. They help to extend the life of the main filters, and also help to ensure that the air being released from the dust collector is as clean as possible.
9. HEPA filters

HEPA (High-Efficiency Particulate Air) filters are a type of air filter that is designed to capture extremely small particles of dust and debris, such as those found in industrial and laboratory settings. HEPA filters are made from a mat of very fine fibers, such as glass or synthetic fibers, that are arranged in a way that creates a labyrinth of pathways for air to flow through. As air flows through these pathways, particles of dust and debris are captured on the fibers, effectively purifying the air.
HEPA filters are considered highly efficient at capturing dust and debris particles, with a minimum efficiency rating of 99.97%. This means that they are able to capture at least 99.97% of particles that are 0.3 microns or larger in size. This makes HEPA filters ideal for use in environments where very fine particles of dust and debris are present, such as in laboratories, hospitals, and clean rooms.
HEPA filters are also often used as after-filters in cartridge dust collectors. These filters are typically located after the main filter cartridges and are designed to capture any remaining dust particles that may not have been effectively captured by the main filters. This helps to ensure that the air being released from the dust collector is as clean as possible and that the dust collector is meeting the necessary safety standards.
HEPA filters are important for the proper functioning and maintenance of the dust collector as they help to improve the overall performance of the dust collector by capturing extremely small particles of dust and debris, such as those found in industrial and laboratory settings. This makes HEPA filters ideal for use in environments where very fine particles of dust and debris are present, such as in laboratories, hospitals, and clean rooms.
All these components work together to ensure that the dust collector is able to effectively remove particulate matter from the air, while also providing low maintenance, high efficiency, and flexibility.
Conclusion

In conclusion, a cartridge dust collector is a highly effective and efficient way to remove dust and debris from the air in industrial settings. The basic principle of a cartridge dust collector is that it captures dust and debris on a filter media and then periodically cleans the filter media to remove the collected dust and debris. The process of capturing and cleaning the dust and debris is accomplished through a combination of mechanical and pneumatic systems.
The various components and processes involved in a cartridge dust collector work together to effectively remove dust and debris from the air. In particular, the filter media is one of the most important components of the dust collector as it is responsible for capturing the dust and debris in the air. Therefore, it is crucial to use high-quality filter media to ensure the proper functioning of the dust collector.
Overall, a cartridge dust collector is an essential piece of equipment for any industrial setting where dust and debris are present. It is important to choose a high-quality dust collector and filter media to ensure the proper functioning of the dust collector and the safety of the workers.
Sofilt is one of the most reliable manufacturers of dust collector filter bags and offers a variety of filter media and materials to choose from. Our filter bags provide superior filtration performance and are designed to effectively capture various sizes of particles. Moreover, our filter media are also designed to be highly durable and long lasting, making them the ideal choice for a variety of industrial and commercial applications.
If you’re looking for the best filter media and dust collector bags, then look no further than Sofilt! Contact us today to learn more about our products and services. We look forward to helping you find the perfect filtration solution for your needs.