Introduction

Choosing the right high efficiency filter bags is essential for maintaining indoor air quality and protecting equipment and machinery from dust and other airborne particles. Here are some guidelines for selecting the right high efficiency filter bags:
Determine the type of particles that need to be filtered
Different high efficiency air filters are designed to capture different types of particles, such as dust, pollen, mold spores, bacteria, and viruses. Different types of particles can have a significant impact on the filtration process. Here are some common types of particles and how they can affect filtration:
Dust and Fine Particles
Dust and fine particles are small particles that can easily become airborne during industrial processes such as sanding, grinding, and cutting. These particles can be problematic for both human health and equipment maintenance. The smaller the particle size, the more difficult it is to capture. To effectively capture dust and fine particles, high-efficiency filters are needed.
Smoke and Fumes
Smoke and fumes are created during high-temperature industrial processes such as welding or brazing. These particles can be small and difficult to capture, so specialized filters like hvac filters may be required. In addition, smoke and fumes can contain hazardous substances such as heavy metals or carcinogens, so it is important to select a furnace filter that can effectively capture and contain these substances.
Oil and Grease
Oil and grease particles are common in industrial processes such as machining and metalworking. These particles can be difficult to capture because they can quickly saturate the filter and reduce its efficiency. Filters that are specifically designed for oil and grease filtration may be necessary to maintain efficient operation.
Biological and Chemical Contaminants
Biological and chemical contaminants such as bacteria, viruses, and hazardous chemicals can pose a significant risk to human health. To effectively capture these contaminants, specialized filters such as HEPA filters or activated carbon filters may be required to prevent air pollution.
The different types of particles can also have different physical and chemical properties that affect the filtration process. For example, particles with irregular shapes or high moisture content can be more difficult to capture than particles with regular shapes and low moisture content. Similarly, particles with high electrical charges can be attracted to and cling to filters, reducing their efficiency over time.
Understanding the type of particles that need to be filtered is important when selecting the right high efficiency particulate air filter for an industrial air filtration system. Different particles can have different properties that affect filtration efficiency, and selecting the right air filters can help ensure that air quality is maintained and equipment is protected.
Consider the efficiency rating

When selecting high efficiency filter bags for indoor air pollutants, it is important to consider the efficiency rating of the filters. Efficiency rating refers to the ability of the filter to remove particles of a certain size from the dirty air that passes through it. The higher the efficiency rating, the more effective the filter is at capturing small particles.
Efficiency ratings for air purifiers are typically expressed as a percentage of particles removed from the air. For example, a filter with an efficiency rating of 95% will remove 95% of particles that are the size it was designed to capture. The size of particles that a filter can capture is typically measured in microns.
When choosing the right high efficiency filter bags, it is important to consider the specific industrial air filtration needs. Factors such as the size and type of particles that need to be filtered, the volume of air that needs to be filtered, and the operating conditions of the filtration system should all be taken into account.
For example, if the industrial process produces fine particulate matter, such as smoke, dust, or fumes, a filter bag with a high efficiency rating, such as 95% or higher, would be appropriate. If the process produces larger particles, such as chips or debris, a filter bag with a lower efficiency rating may be sufficient.
It is also important to consider the cost of the filter bags when choosing a high efficiency filter. While high efficiency filters may be more expensive upfront, they may provide cost savings over time due to their ability to capture more particles and reduce the need for filter replacements.
Considering the efficiency rating of filter bags is an important guideline for choosing the right high efficiency filter bags for your industrial air filtration needs. Understanding the specific industrial process, the size and type of particles that need to be filtered, and the operating conditions of the filtration system will help to determine the appropriate efficiency rating for the filter bags.
Check the MERV rating
MERV (Minimum Efficiency Reporting Value) rating is a standard used to evaluate the performance of air filters used in HVAC systems (Heating, Ventilation, and Air Conditioning) systems. The MERV rating system ranges from 1 to 20, with higher Merv ratings indicating a higher level of filtration efficiency.
When it comes to choosing the right high-efficiency filter bags for industrial air filtration needs, checking the MERV rating is an essential guideline. The MERV scale helps to determine the filter’s ability to remove airborne contaminants such as dust, pollen, mold spores, and other airborne particles from the air.
It’s important to note that different industrial air filtration needs require different levels of filtration efficiency. For instance, applications in the food and beverage industry require a higher level of filtration than applications in the cement or construction industry.
A MERV rating of 8 to 13 is generally recommended for most industrial air filtration needs. However, for applications that require a higher level of filtration, such as in the pharmaceutical or electronics industry, a MERV rating of 14 to 20 is more appropriate.
It’s important to keep in mind that a higher MERV rating may not always be the best option as it can result in higher air resistance and reduced airflow, which can decrease the overall efficiency of the system. Additionally, it’s important to regularly monitor and maintain the filter bags to ensure they are functioning optimally. It’s important to consider the specific requirements of each application and balance filtration efficiency with system performance to ensure optimal results.
Check the airflow rating

High efficiency filter bags can restrict airflow, which can cause problems with ventilation systems. Make sure to choose filter bags with an airflow rating appropriate for the system’s needs. The airflow rating refers to the maximum amount of air that can pass through the filter bag without causing damage or compromising its filtration efficiency.
Choosing a filter bag with the appropriate airflow rating is critical for ensuring effective air filtration while also maintaining optimal system performance. If the airflow rating is too low, it can result in increased resistance to airflow, which can cause the system to work harder and potentially lead to premature filter failure. On the other hand, if the airflow rating is too high, it may not provide adequate filtration efficiency, allowing harmful contaminants to pass through and compromise air quality.
The airflow rating is typically determined by the type of filter media used, the thickness of the filter media, and the size and shape of the filter bag. Therefore, it’s essential to consider these factors when selecting filter bags for industrial air filtration applications.
In addition to the airflow rating, other important considerations when choosing high-efficiency filter bags for industrial air filtration needs include the size and shape of the filter bag, the type of contaminants being filtered, and the operating conditions of the filtration system. By taking these factors into account, you can select the right filter bags for your specific needs and ensure optimal system performance and air quality.
Check the filter bag material

High efficiency filter bags are typically made of materials like polyester, fiberglass, or polypropylene. Each material has its own advantages and disadvantages, so choose the material that best suits the application. The importance of choosing the right high-efficiency filter bag for industrial air filtration needs to includes;
Filtering Efficiency
The filter bag material plays a crucial role in determining the filtering efficiency of the bag. The right filter bag material can effectively capture airborne pollutants such as dust, dirt, and other contaminants. The wrong filter bag material can allow pollutants to escape into the atmosphere, leading to health and safety hazards for workers and environmental pollution.
Durability
The material should be durable enough to withstand harsh industrial environments. It should resist wear and tear, abrasion, and damage from high temperatures and humidity. A filter bag made from a weak or brittle material may rupture or break, leading to frequent replacements and downtime for the filtration system.
Compatibility
It should be compatible with the specific application and the industrial air filtration system being used. Some applications may require a bag with specific properties, such as resistance to chemicals or flame retardancy. Additionally, the filter bag material must fit properly into the filtration system to ensure effective filtering and prevent leakage.
Maintenance
The material should be easy to maintain and replace. The right filter bag material can be cleaned and reused, reducing operating costs and minimizing waste. A filter bag made from an unsuitable material may be difficult to clean or may require frequent replacements, increasing the overall operating costs of the filtration system.
Environmental impact
The filter bag material should be environmentally friendly and not contribute to pollution. Some filter bag materials are recyclable or made from renewable resources, which can help reduce the environmental impact of industrial air filtration.
Checking the filter bag material is crucial when choosing the right high-efficiency filter bag for industrial air filtration needs. The right filter bag material can ensure effective filtration, durability, compatibility, and ease of maintenance, reducing costs and improving the overall efficiency of the filtration system.
Check the filter bag dimensions

Make sure to choose filter bags that fit properly into the system’s filter housing. Filter bags that are too large or too small can cause airflow problems and reduce filter efficiency. Properly sizing the filter bag is crucial for achieving optimal filtration performance and ensuring efficient airflow.
When selecting filter bags, it is important to choose bags that are compatible with the specific air filtration system being used. This includes ensuring that the filter bag dimensions are appropriate for the dimensions of the filter housing and the airflow rate.
In addition to ensuring proper fit, choosing the correct filter bag dimensions can also impact the efficiency of the filtration system. If the filter bag is too small, it may not capture all of the particulate matter in the air, leading to decreased filtration efficiency. Conversely, if the filter bag is too large, it may impede airflow and cause a drop in system efficiency.
It is also important to consider the depth of the filter bag when selecting the appropriate dimensions. A deeper filter bag can increase the surface area available for filtration, which can improve the overall efficiency of the system.
Consider the cost
High efficiency filter bags can be more expensive than standard filters. Consider the cost of the filter bags over time, including maintenance and replacement costs, to determine the overall cost-effectiveness of the filters. While it may be tempting to simply choose the most expensive option on the market, this is not always the most cost-effective choice. Some of the key points to keep in mind when considering the cost of high efficiency filter bags include:
Initial cost
The cost of the filter bags themselves is obviously an important consideration. However, it is important to look beyond just the sticker price and consider other factors such as the lifespan of the bags and their efficiency in filtering out particles. A more expensive filter bag may actually be more cost-effective in the long run if it lasts longer or filters out more particles than a cheaper alternative.
Maintenance cost
In addition to the cost of the filter bags, it is important to consider the cost of maintaining them. This includes things like the cost of labor to change the bags, the frequency of bag changes, and any equipment needed to change the bags. Choosing a filter bag that requires less frequent changes or is easier to change can help reduce maintenance costs over time.
Energy cost
Another important cost to consider is the energy cost associated with running the air filtration system. High efficiency filter bags may require more energy to operate than less efficient options. It is important to weigh the increased energy cost against the potential cost savings from improved filtration and longer bag life.
Environmental cost
Finally, it is important to consider the environmental cost of using high efficiency filter bags. While these bags may be more effective at filtering out particles, they may also be made from materials that are more difficult to dispose of or recycle. It is important to consider the environmental impact of the filter bags as well as their cost.
Generally, when choosing the right high efficiency filter bags for industrial air filtration needs, it is important to consider the cost from all angles. By taking a comprehensive approach to cost analysis, it is possible to make an informed decision that balances cost-effectiveness with optimal filtration performance.
Check the manufacturer's specifications
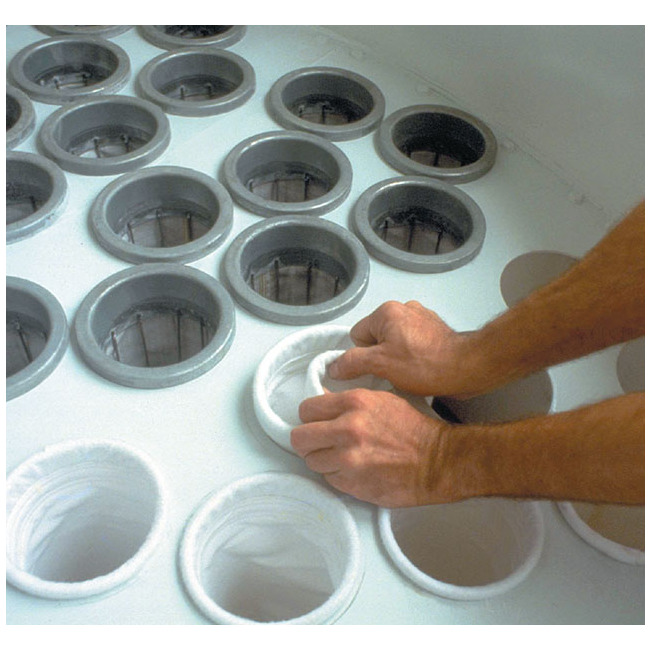
Finally, make sure to check the manufacturer’s specifications to ensure that the filter bags meet the system’s requirements and are appropriate for the specific application. This means carefully reviewing the technical data and performance characteristics provided by the manufacturer for the filter bags you are considering.
Here are some key reasons why this guideline is important:
Efficiency
The manufacturer’s specifications will tell you the filtration efficiency of the filter bags. This is critical because it determines how effectively the filter bags will remove contaminants from the air. You want to choose filter bags with a high efficiency rating to ensure that your air quality is properly maintained.
Capacity
The manufacturer’s specifications will also tell you the maximum capacity of the filter bags. This is important because it determines how long the bags can be used before they need to be replaced. Choosing filter bags with the appropriate capacity can help you optimize your maintenance schedule and reduce downtime.
Pressure drop
The manufacturer’s specifications will also provide information on the pressure drop across the filter bags. This is important because it determines how much energy will be required to move air through the bags. Choosing filter bags with a lower pressure drop can help you reduce energy consumption and save on operating costs.
Compatibility
The manufacturer’s specifications will also provide information on the compatibility of the filter bags with different types of air filtration systems. Choosing filter bags that are designed to work with your specific system can help you ensure optimal performance and avoid compatibility issues.
Checking the manufacturer’s specifications is a critical guideline for choosing the right high efficiency filter bags for industrial air filtration needs. By carefully reviewing the technical data and performance characteristics provided by the manufacturer, you can ensure that you select the filter bags that will best meet your specific requirements and provide the most efficient and effective air filtration.
Conclusion
When it comes to choosing the right high efficiency filter bags for industrial air filtration needs, there is a lot to consider. From cost and environmental factors to performance characteristics and compatibility, it is important to take a comprehensive approach to selection. Checking the manufacturer’s specifications is essential for ensuring that you get the best possible filter bags for your system.
By following these guidelines, you can make an informed decision and select filter bags that will provide the optimal filtration performance for your specific needs. If you have any questions regarding the selection of your filter bags, it is important to consult a professional in the industry who can provide expert advice and guidance. Sofilt is the most experienced and reliable filter bag supplier in the industry, so please feel free to contact us if you have any questions.
