Introduction

Baghouses are a type of air pollution control equipment that uses filters to remove particulates from the air stream. These filters can become clogged or damaged over time, leading to reduced airflow and a decrease in efficiency. In some cases, this can lead to baghouse filter failure and even complete system shutdown.
In this article, we will discuss the common causes of baghouse filter failure and what steps should be taken to prevent it. There are many potential causes of baghouse filter failure, which can include the following:
Abrasion
Abrasion is the wearing away of a material due to rubbing against another surface. If the particulates being filtered are highly abrasive, they can wear down the filters over time, causing them to fail. This is often the case when filtering coal or other heavy particulates, as these materials tend to be harder and more abrasive than others. This can cause the filters to wear down over time, leading to failure.
There are several factors that can contribute to abrasion:
- Abrasive particulates: If the particulates being filtered are highly abrasive, they can wear down the filters over time.
- High dust load: If the baghouse is used to filter a high volume of particulates, the filters may experience more abrasion.
- High air flow rate: If the air flow rate through the baghouse is too high, the particulates may impact the filters with more force, increasing the amount of abrasion.
- Incorrect bag selection: Using the wrong type of filter bag can lead to abrasion. For example, if the bags are not designed to handle abrasive particulates, they may wear down more quickly.
To prevent abrasion from causing filter failure, it is important to use filters that are designed to handle abrasive particulates and to operate the baghouse within its design parameters, including the air flow rate. It is also important to follow proper maintenance procedures, including cleaning the filters and replacing them when needed, to ensure that they are able to function properly.
Chemical Attack
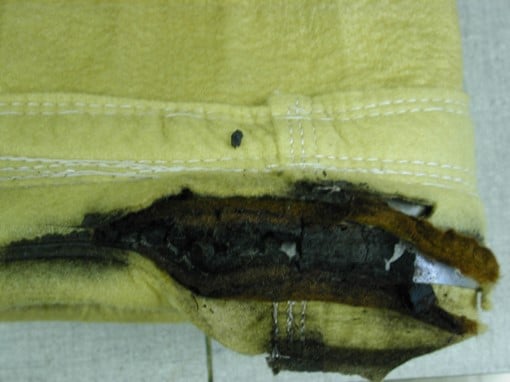
Some particulates can react chemically with the filters, causing them to break down or become less effective. This is often the case when filtering hazardous materials, such as acids, solvents, and other chemicals. The filters may also degrade over time if they are exposed to moisture, humidity, or other environmental conditions.
Some of the factors that can contribute to a chemical attack:
- Incompatible materials: If the filters are made of a material that is not resistant to the chemical composition of the particulates being filtered, they may corrode or break down over time.
- Corrosive particulates: Some particulates, such as acidic or basic substances, can be corrosive and can react with the filters, causing them to break down or become less effective.
- High humidity: High humidity can contribute to chemical attack by increasing the likelihood of corrosion or chemical reactions.
To prevent chemical attacks from causing filter failure, it is important to use filters that are made of materials that are resistant to the chemical composition of the particulates being filtered. It is also important to ensure that the filters are not exposed to high humidity, which can accelerate chemical reactions. In addition, it may be necessary to use special coatings or treatments on the filters to protect them from chemical attacks.
Wrong bag selection
Using the wrong type of filter bags can lead to premature failure. For example, if the filters are not designed to handle the size or chemical composition of the particulates being filtered, they may break down or become less effective. It is important to select the correct type of filter bag for a given application so that it can effectively and reliably filter the desired particulates.
Some of the factors to consider when selecting filter bags include:
Size and shape of particulates: The type of bag needed will depend on the size and shape of the particulates being filtered.
Chemical composition of particulates: The bag should be able to handle any chemical components in the particulates so that they do not degrade or break down over time.
Operating conditions: As mentioned above, the operating conditions of the baghouse, such as air flow rate and temperature, should be taken into account when selecting the filter bags.
Environmental conditions: The bag should be able to handle any environmental factors that may affect its performance, such as humidity and temperature.
Finally, it is important to ensure that the baghouse is properly maintained by following manufacturer instructions and performing regular inspections of the filters and bags. Regular maintenance will help ensure that the baghouse
Incorrect installation
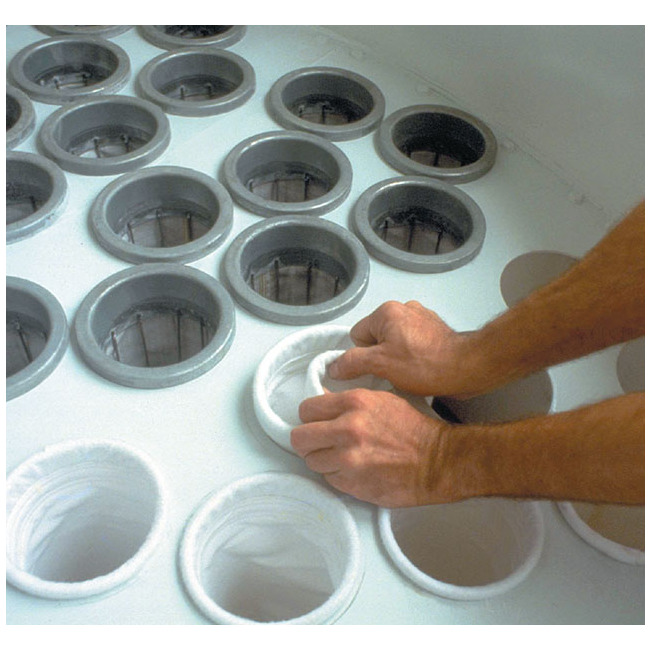
If the filters are not installed correctly, they may not function properly. For example, if the filters are not properly sealed to the baghouse housing, air may leak through, reducing the effectiveness of the baghouse.
Factors that can contribute to incorrect installation include inadequate sealant, incorrect placement, improper alignment of the filters and baghouse housing, or insufficient tensioning of the filter bags. If the filters are not placed in the correct location within the baghouse, they may not function properly.
Also if the filters are not properly sealed to the baghouse housing, air may leak through, reducing the effectiveness of the baghouse. In case the filters are not oriented correctly or properly aligned within the baghouse, they may not function properly. Failure to tighten the filters to the proper torque means that they may not be held securely in place and may not function properly.
To prevent the incorrect installation from causing filter failure, it is essential to carefully follow the manufacturer’s instructions for installing the filters. This may include ensuring that the filters are placed in the correct location, properly sealed, oriented correctly, and tightened to the proper torque. It is also essential to properly train and supervise any personnel who are responsible for installing the filters.
Poor maintenance
Proper maintenance is essential for ensuring that the filters are able to function properly and achieve their expected lifespan. Failure to properly maintain the baghouse, including cleaning the filters and replacing them when needed, can cause them to fail.
There are several specific ways in which poor maintenance can lead to filter failure:
- Clogging: If the filters are not cleaned regularly, they may become clogged with particulates, which can reduce their effectiveness and eventually cause them to fail.
- Aging: As filters age, they can become less effective and eventually fail. If the filters are not replaced when needed, they may continue to be used beyond their useful lifespan, leading to failure.
- Damage: If the filters are not handled carefully during maintenance, they may become damaged, leading to failure.
- Incorrect cleaning: If the filters are not cleaned properly, they may become less effective or fail completely. This can include using the wrong cleaning methods or chemicals, or not thoroughly cleaning the filters.
- Incorrect replacement: If the filters are not replaced when needed, they may fail. This can include using the wrong type of replacement filters or using filters that are past their useful lifespan.
Proper maintenance is critical to ensuring the long-term functioning of baghouse filters. It is important to follow the manufacturer’s recommended maintenance procedures in order to prevent filter failure and extend the lifespan of the filters.
Clogging

If the filters become clogged with particulates, they will not be able to function properly. Clogging is a common cause of baghouse filter failure. It occurs when the filters become so filled with particulates that they are unable to function properly. This can lead to reduced efficiency and eventually to filter failure.
There are several factors that can contribute to clogging and reducing the effectiveness of the baghouse filters. These include:
- High dust load: If the baghouse is used to filter a high volume of particulates, the filters may become clogged more quickly.
- Fine particulates: Fine particulates, such as those smaller than 10 microns, can be more difficult to filter and may clog the filters more easily.
- Incorrect bag selection: Using the wrong type of filter bags can lead to clogging. For example, if the bags are not designed to handle the size or chemical composition of the particulates being filtered, they may become clogged more easily.
- Incorrect operating conditions: If the baghouse is not operated within its design parameters, the filters may become clogged more easily. For example, if the airflow rate is too high, the filters may not have enough time to effectively filter the particulates, leading to clogging.
- Poor maintenance: Neglecting to properly maintain the baghouse, including cleaning the filters, can lead to clogging.
To prevent clogging, it is important to use the correct type of filter bags for the application, operate the baghouse within its design parameters, and follow proper maintenance procedures. If clogging does occur, it is important to clean the filters to restore their effectiveness.
Overloading
If the baghouse is used to filter more air than it is designed for, the filters may become overwhelmed and fail. This can occur if the airflow rate is too high, or if the particulate levels are higher than expected. Overloading can lead to filter failure as the filters become overwhelmed and unable to function properly. To prevent overloading, it is important to ensure that the baghouse is operated within its
There are several factors that can contribute to overloading:
- High dust load: If the baghouse is used to filter a high volume of particulates, the filters may become overloaded more quickly.
- Incorrect bag selection: Using the wrong type of filter bags can lead to overloading. For example, if the bags are not designed to handle the size or chemical composition of the particulates being filtered, they may become overloaded more easily.
- Incorrect operating conditions: If the baghouse is not operated within its design parameters, the filters may become overloaded more easily. For example, if the airflow rate is too high, the filters may not have enough time to effectively filter the particulates, leading to overloading.
- Poor maintenance: Neglecting to properly maintain the baghouse, including cleaning the filters, can contribute to overloading.
To prevent overloading, it is important to use the correct type of filter bags for the application, operate the baghouse within its design parameters, and follow proper maintenance procedures. If overloading does occur, it is important to address the issue as soon as possible to prevent filter failure. This may involve reducing the air flow rate, cleaning the filters, or replacing the filters if necessary.
High temperatures
Some filters are sensitive to high temperatures and can fail if the baghouse is operated at too high of a temperature. This is especially true for filters made from synthetic materials, as they may become deformed and weakened by high temperatures. To prevent this, it is important to consider several factors that can contribute to high temperatures in a baghouse:
- Ambient temperature: If the ambient temperature around the baghouse is high, it can contribute to elevated temperatures inside the baghouse.
- Process temperature: If the process being filtered generates high temperatures, it can contribute to elevated temperatures inside the baghouse.
- Air flow rate: If the air flow rate through the baghouse is too high, it can increase the temperature inside the baghouse.
- Incorrect bag selection: Using the wrong type of filter bags can lead to high temperatures. For example, if the bags are not designed to handle high temperatures, they may fail.
To prevent high temperatures from causing filter failure, it is important to operate the baghouse within its design parameters, including temperature limits. This may involve reducing the air flow rate, using a different type of filter bag, or implementing other measures to reduce the temperature inside the baghouse. It is also important to follow proper maintenance procedures, including cleaning the filters and replacing them when needed, to ensure that they are able to function properly.
Poor filter design

If the filter design is not adequate for the application, the filters may fail due to inadequate performance. This may include:
- Inadequate filtration efficiency: If the filters are not designed to effectively remove the particulates being filtered, they may fail.
- Incompatible materials: If the filters are made of a material that is not compatible with the particulates being filtered, they may break down or become less effective over time.
- Incorrect size: If the filters are not the correct size for the application, they may not function properly. For example, if the filters are too small, they may become overloaded more easily.
- Poor construction: If the filters are poorly constructed, they may fail prematurely.
In order to ensure that a poor filter does not cause filter failure, it is important to use filters that are designed for the specific application and made of materials that are compatible with the particulates being filtered. It is also important to ensure that the filters are the correct size for the application and are constructed properly.
Poor filter material
If the filter material is not of high quality, it may break down or become less effective over time. There are several factors that can contribute to poor filter material:
- Incompatibility with the particulates being filtered: If the filter material is not compatible with the chemical composition or physical properties of the particulates being filtered, it may break down or become less effective over time.
- Poor durability: If the filter material is not durable, it may break down or become less effective more quickly.
- Poor quality control: If the quality control procedures for the filter material are not followed, the filters may be made of inferior material that is prone to failure.
To prevent the issue of poor filter material causing filter failure, it is important to use high-quality filter material that is compatible with the particulates being filtered. It is also important to follow proper quality control procedures to ensure that the filter material meets the necessary standards. In addition, it may be necessary to use special coatings or treatments on the filters to protect them from degradation over time.
Aging
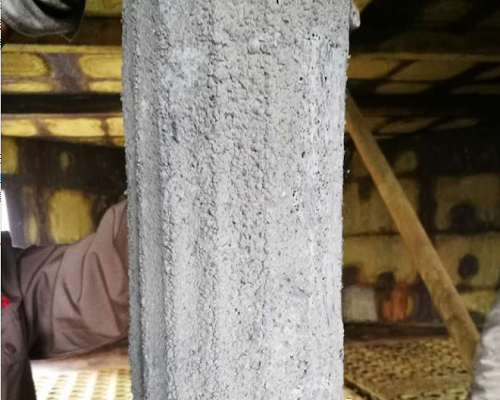
Aging is a natural process that can lead to baghouse filter failure. As filters age, they can become less effective and eventually fail. Aging can be caused by a number of factors, including:
- Wear and tear: Over time, the filters may experience wear and tear due to the constant exposure to particulates and the mechanical forces involved in the filtration process.
- Environmental factors: The filters may be exposed to environmental factors, such as temperature and humidity, that can contribute to their degradation over time.
- Chemical attack: Some particulates can react chemically with the filters, causing them to break down or become less effective over time.
In order to prevent aging from causing filter failure, it is important to follow proper maintenance procedures, including cleaning the filters and replacing them when needed. It is also important to use filters that are designed to withstand the environmental conditions and chemical compositions of the particulates being filtered. In addition, it may be necessary to use special coatings or treatments on the filters to protect them from degradation over time.
Poor filter cleaning
If the filters are not cleaned properly, they may become less effective or fail completely. There are several factors that can contribute to incorrect filter cleaning:
- Incorrect cleaning method: If the wrong cleaning method is used, it may not effectively remove the particulates from the filters.
- Wrong cleaning frequency: If the filters are not cleaned frequently enough, they may become clogged or otherwise impaired. On the other hand, if they are cleaned too frequently, they may become damaged or less effective.
- Wrong cleaning chemicals: If the wrong cleaning chemicals are used, they may damage the filters or leave a residue that can impair their performance.
- Poor cleaning techniques: If the filters are not cleaned thoroughly or if they are handled improperly during the cleaning process, they may become damaged or less effective.
To prevent incorrect filter cleaning from causing filter failure, it is important to follow the manufacturer’s recommendations for cleaning the filters.
This may include using the correct cleaning method, frequency, and chemicals, and handling the filters carefully during the cleaning process. It is also important to properly train and supervise any personnel who are responsible for cleaning the filters.
Poor filter installation
If the filters are not installed correctly, they may not function properly. This can be caused by a number of factors, including:
- Incorrect placement: If the filters are not placed in the correct location within the baghouse, they may not function properly.
- Incorrect sealing: If the filters are not properly sealed to the baghouse housing, air may leak through, reducing the effectiveness of the baghouse.
- Incorrect orientation: If the filters are not oriented correctly within the baghouse, they may not function properly.
- Wrong tightening: If the filters are not tightened to the proper torque, they may not be held securely in place and may not function properly.
To prevent incorrect filter installation from causing filter failure, it is essential to carefully follow the manufacturer’s instructions for installing the filters. This may include ensuring that the filters are placed in the correct location, properly sealed, oriented correctly, and tightened to the proper torque. It is also essential to properly train and supervise any personnel who are responsible for installing the filters.
Conclusion

Filter failure can have serious consequences, including reduced efficiency and increased emissions. To prevent filter failure, it is important that the filters are selected and maintained properly, cleaned correctly, and installed correctly.
This is why at Sofilt, we strive to provide our customers with the best filter products, maintenance, and installation services. Our experienced team can help you choose the right filters and ensure that they are installed and maintained correctly so that you can have peace of mind knowing your system is functioning properly.
A well-functioning filter system is essential for efficient operation and compliance with environmental regulations. Contact us today to learn more about how we can help you ensure your filter system is operating correctly.