Introduction
Dust filters are essential components of industrial and commercial operations where dust and particulate matter are generated. These filters help maintain clean air quality and protect workers from harmful dust particles. Filter bags, on the other hand, are a critical part of dust filters. They capture the dust and particulate matter that passes through the filter and prevent it from contaminating the air.
Selecting the right filter bag for your dust filter is crucial to ensure the optimal performance and efficiency of your dust filtration system. The right filter bag will not only increase the lifespan of the filter but also save you time and money in the long run.
Today, we will provide an overview of the top considerations you should keep in mind when selecting the perfect filter bag for your dust filter. We will discuss the different types of filter bags available, the materials used to make them, and the applications they are suitable for. Additionally, we will provide tips for maintaining and caring for your filter bag to ensure its longevity and optimal performance. By the end of this article, you will have a comprehensive understanding of the factors you need to consider to select the right filter bag for your dust filter.
Types of Filter Bags
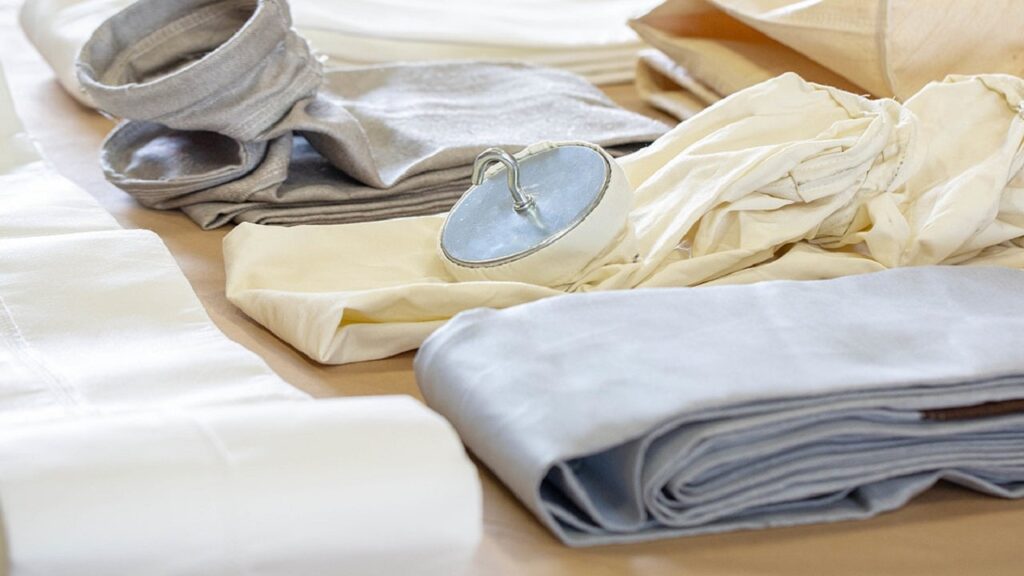
When it comes to selecting the right filter bag for your dust filter, one of the most critical decisions is choosing the right material. There are various filter bag materials available in the market, each with its unique advantages and disadvantages. In this section, we will discuss some of the most common filter bag materials and their applications.
Polyester
Polyester filter bags are one of the most popular filter bag materials due to their excellent resistance to chemicals and abrasion. These bags are commonly used in industries that generate dry, non-aggressive dust such as woodworking, cement, and pharmaceuticals. Polyester filter bags are also ideal for high-temperature applications as they can withstand temperatures up to 275°F (135°C).
Advantages
Durable, resistant to chemicals and abrasion, and suitable for high-temperature applications.
Disadvantages
Not suitable for moist or oily environments.
Polypropylene
Polypropylene filter bags are commonly used in applications that generate moist or oily dust such as food processing, chemical processing, and wastewater treatment. These bags have excellent resistance to water and oil and can withstand temperatures up to 200°F (93°C).
Advantages
Resistant to water and oil, suitable for moist and oily environments.
Disadvantages
Not suitable for high-temperature applications.
Nylon
Nylon filter bags are known for their exceptional strength and durability, making them ideal for applications that generate sharp and abrasive dust. These bags are commonly used in industries such as metalworking, mining, and foundries. Nylon filter bags can withstand temperatures up to 300°F (149°C).
Advantages
Strong and durable, suitable for abrasive dust, and can withstand high temperatures.
Disadvantages
Not suitable for moist or oily environments.
Polyphenylene Sulfide (PPS)
PPS filter bags are ideal for applications that generate acidic and alkaline dust. These bags are commonly used in industries such as coal-fired power plants, waste incineration, and cement manufacturing. PPS filter bags can withstand temperatures up to 375°F (190°C).
Advantages
Resistant to acidic and alkaline dust, suitable for high-temperature applications.
Disadvantages
Limited resistance to hydrolysis.
Choosing the Right Material

When choosing the right filter media material for your needs, it is essential to consider the type of dust your operation generates, the temperature of the process, and the chemical composition of the dust. It is also crucial to consider the filtration efficiency required and the expected lifespan of the filter media.
For example, if you are operating in a woodworking facility, polyester bag filters may be the best option due to their resistance to abrasion and chemicals. However, if your operation generates moist or oily dust, polypropylene filter bags may be a better option.
Ultimately, selecting the right filter bag material for your needs will depend on a range of factors specific to your operation. It is essential to consult with a filtration expert to help you determine the best filter bag material for your needs.
Filter Bag Size and Design
Selecting the right size and design for your filter bag is crucial to ensure the optimal performance of your dust filtration system. The size and design of your filter bag will impact the filtration efficiency and airflow, as well as the lifespan of your dust collector filter. Let’s find out the importance of selecting the right size and design, the factors to consider when selecting size and design, and how to choose the right size and design for your needs.
Importance of Selecting the Right Size and Design
The importance of selecting the right size and design of your filter bag for your dust filtration system cannot be overstated. It is crucial to the overall effectiveness and efficiency of the system. The size and design of the baghouse filter determine the amount of dust and other particles that can be captured, the airflow rate of the system, and the lifespan of the filter bag.
The size of the filter bag should be proportional to the size of your dust collector. A bag filter that is too small will not effectively capture all the dust particles generated by your operation. This leads to reduced air quality and increased maintenance costs. Conversely, if the filter bag is too large, it can cause restricted airflow, leading to reduced efficiency of the filtration system.
The design of the filter bag also plays a critical role in its effectiveness. A poorly designed bag filter can cause dust particles to become trapped and clog the bag, leading to reduced airflow and increased maintenance. The design should take into account the type of dust generated by your operation, the airflow rate, and the expected lifespan of the filter bag.
Additionally, the size and design of the filter bag will impact the overall efficiency of the filtration system. If the filter bag is not properly sized or designed, it can lead to reduced filtration efficiency, resulting in increased operating costs, decreased production, and reduced overall system performance.
Selecting the right size and design for your filter bag is essential to ensure the optimal performance of your dust filtration system. It will impact the filtration efficiency, airflow, and lifespan of your filter bag, and ultimately the overall efficiency of your system. By consulting with a filtration expert and taking into consideration the specific needs of your operation, you can select the right size and design to maximize the effectiveness and efficiency of your dust filtration system.
Factors to consider when selecting size and design
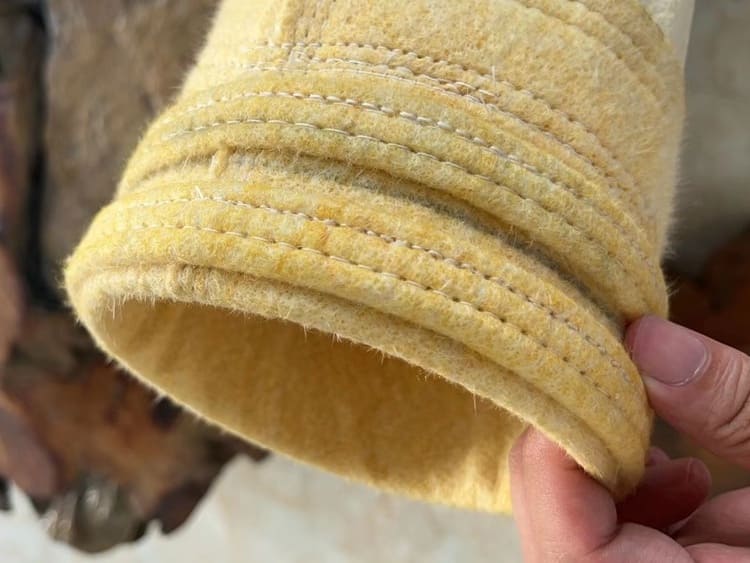
When selecting the size and design of your filter bag, there are several factors to consider. These include the size and shape of your dust collector, airflow rate, type of dust generated by your operation, expected filter life of your filter bag, and filtration efficiency required.
Size and shape of your dust collector
The size and shape of your dust collector will determine the size of the filter bag required. If the bag filter is too small, it may not capture all of the dust particles generated by your operation, leading to reduced air quality and increased maintenance costs. Conversely, if the filter bag is too large, it can cause restricted airflow, leading to reduced efficiency of the filtration system and the formation of dust load.
Airflow rate
The airflow rate of your system will also determine the size of the dust collectors required. A high airflow rate may require a larger filter bag to ensure optimal performance. If the airflow rate is too low, the filter bag may not capture all of the dust particles, leading to reduced air quality and increased maintenance costs.
Type of dust generated by your operation
The type of dust generated by your operation will impact the design of the filter bag required. If your operation generates large or heavy dust particles, a larger filter bag with a more robust design may be required. Similarly, if your operation generates fine or lightweight dust particles, a smaller filter bag with a more delicate design may be appropriate.
The expected lifespan of your filter bag
The expected lifespan of your filter bag will impact the material and design of the filter bag required. If you are operating in a high-volume environment, you may need to replace your filter bag more frequently. In this case, a more durable filter bag with a longer filter life may be necessary.
Filtration efficiency required
The filtration efficiency required will impact the design of the filter bag required. If you require high levels of filtration efficiency, a filter bag with a more complex design and finer filter media may be required.
For example, if you are operating in a woodworking shop, you will generate large amounts of sawdust. You would need to consider a filter bag with a large surface area to ensure that all of the sawdust is captured. Additionally, if the airflow rate is high, a larger filter bag with a more robust design would be necessary to handle the higher volume of sawdust.
On the other hand, if you are operating in a pharmaceutical manufacturing facility, you would require a higher level of filtration efficiency. In this case, a filter bag with a more complex design and finer filter media would be necessary to capture the smaller particles generated by the operation.
It is essential to consider various factors when selecting the size and design of the correct filter media to ensure optimal performance of your dust filtration system. By taking into account the specific needs of your operation, you can select the right size and design to maximize the effectiveness and efficiency of your dust filtration system.
How to choose the right size and design for your needs

To choose the right size and design for your dust collection systems, there are several steps you can take:
- Determine the size and shape of your dust collector: Measure the dimensions of your dust collector to determine the size of the filter bag required. If your dust collector is an irregular shape, consider using a custom filter bag.
- Calculate the airflow rate of your system: Determine the airflow rate of your system in cubic feet per minute (CFM) to determine the appropriate size of the filter bag. You can use a flow meter or consult with a dust collection specialist to determine the airflow rate.
- Identify the type of dust generated by your operation: Different types of dust require different filter media and designs. Consider the size, weight, and shape of the dust particles generated by your operation.
- Determine the expected lifespan of your filter bag: Estimate how frequently you will need to replace your filter bag based on your operating conditions and budget. This will impact the material and design of the filter bag required.
- Determine the filtration efficiency required: Consider the level of filtration efficiency required for your operation. This will impact the design and filter media and inform the filter bag performance.
For example, if you are operating a small woodworking shop with a dust collector that measures 20 inches in diameter and 30 inches in height and an airflow rate of 500 CFM, you would require a filter bag with a diameter of 19 inches and a height of 27 inches. Additionally, if the dust generated by your operation is primarily sawdust, you would need a filter bag with a design that can handle a high volume of large, lightweight particles.
On the other hand, if you are operating a large pharmaceutical manufacturing facility with a dust collector that handles an airflow rate of 10,000 CFM, you would require a much larger filter bag. You would also need to consider a filter bag with a high filtration efficiency to ensure that the smaller particles generated by your operation are captured. In this case, a filter bag with a pleated design and finer filter media may be necessary.
Selecting the right size and design for your filter bag requires careful consideration of several factors, including the size and shape of your dust collector, airflow rate, type of dust generated, the expected lifespan of the filter bag, and the filtration efficiency required. By taking the time to assess these factors and consult with a dust collection specialist, you can select the right size and design to optimize the performance of your dust filtration system.
Filtration Efficiency
Filtration efficiency is the measure of a filter’s ability to capture and retain particles of a certain size. It is typically expressed as a percentage, with higher percentages indicating greater efficiency. Filtration efficiency is determined by performing a particle count before and after the filter and calculating the percentage of particles captured.
There are several standards for measuring filtration efficiency, including the European Norm (EN) and the American Society of Heating, Refrigerating, and Air-Conditioning Engineers (ASHRAE). The most commonly used standard is the MERV (Minimum Efficiency Reporting Value) rating system, which measures a filter’s ability to capture particles ranging in size from 0.3 to 10 microns.
Importance of selecting the right filtration efficiency
Selecting the right filtration efficiency is crucial for maintaining a healthy and safe working environment, as well as protecting your equipment and processes. If your filter bag does not capture all of the dust and contaminants generated by your operation, they can become airborne and pose a health risk to workers. Additionally, if the dust and contaminants are not properly captured, they can accumulate on equipment and processes, leading to damage and reduced efficiency.
Factors to consider when selecting filtration efficiency
When selecting filtration efficiency, there are several factors to consider, including:
- Type and size of dust: Different types and sizes of dust require different filtration efficiencies. For example, a filter bag with a MERV rating of 10 may be sufficient for capturing larger particles like sawdust, while a MERV rating of 16 may be necessary for capturing smaller particles like metal shavings or pharmaceutical dust.
- Operating conditions: The operating conditions of your facility, such as temperature, humidity, and airflow, can impact the performance of your filter bag. In some cases, a higher filtration efficiency may be necessary to compensate for challenging operating conditions.
- Regulatory requirements: Depending on the industry and location of your facility, there may be regulatory requirements for filtration efficiency. It is important to research and understand any applicable regulations to ensure compliance.
To choose the right filtration efficiency for your needs, you should consider the factors mentioned above and consult with a dust collection specialist. They can help you identify the type and size of dust generated by your operation, assess your operating conditions, and ensure compliance with any regulatory requirements. Based on this information, they can recommend a filter bag with the appropriate MERV rating or other filtration efficiency measurement to ensure that your dust filtration system is effective and efficient.
Compatibility with Dust Type

Different types of dust and how they affect filter bag selection
There are several different types of dust that can be generated by various industrial processes, each of which presents unique challenges for filtration. Some common types of dust include:
- Fine dust: Fine dust is made up of small particles that are less than 10 microns in size. This type of dust can be difficult to capture and requires a filter bag with a high filtration efficiency.
- Coarse dust: Coarse dust is made up of larger particles that are between 10 and 100 microns in size. This type of dust can be easier to capture but may require a filter bag with a larger pore size to prevent clogging.
- Sticky dust: Sticky dust is made up of particles that have a tendency to stick to surfaces. This type of dust requires a filter bag with a low surface tension to prevent buildup and clogging.
- Abrasive dust: Abrasive dust is made up of particles that can be hard and abrasive. This type of dust can cause wear and tear on filter bags and requires a bag with a high abrasion resistance.
Importance of selecting the right filter bag for your dust type
Selecting the right filter bag for your dust type is important for ensuring that your dust collection system is effective and efficient. If the wrong filter bag is used, it may not be able to capture all of the dust generated by your operation, leading to health and safety risks, equipment damage, and reduced efficiency.
Factors to consider when selecting a filter bag for your dust type
When selecting a filter bag for your dust type, there are several factors to consider, including:
- Dust particle size: The size of the dust particles generated by your operation will impact the pore size and filtration efficiency required for the filter bag.
- Dust characteristics: The characteristics of your dust, such as stickiness, abrasiveness, and moisture content, will impact the material and design of the filter bag.
- Operating conditions: The operating conditions of your facility, such as temperature, humidity, and airflow, will impact the performance of your filter bag.
How to choose the right filter bag for your dust type
To choose the right filter bag for your dust type, you should consult with a dust collection specialist who can help you identify the temperature and chemical characteristics of your dust and assess your operating conditions. Based on this information, they can recommend a filter bag material and design that is compatible with your dust type and operating conditions. Some examples of filter bag materials for specific dust types include:
- Polyester felt: Polyester felt is a popular choice for capturing fine dust particles and is resistant to moisture and most chemicals.
- Polypropylene felt: Polypropylene felt is a good choice for capturing coarse dust particles and is resistant to high temperatures.
- PTFE membrane: PTFE membrane is a good choice for capturing sticky or oily dust particles and is resistant to most chemicals and high temperatures.
- Aramid felt: Aramid felt is a good choice for capturing abrasive dust particles and is highly resistant to wear and tear.
Overall, selecting the right filter bag for your dust type is essential for maintaining a safe and efficient workplace. By considering factors such as dust particle size, characteristics, and operating conditions, and working with a dust collection specialist, you can ensure that your filter bag is compatible with your specific dust type and effectively captures all dust particles.
Maintenance and Cost
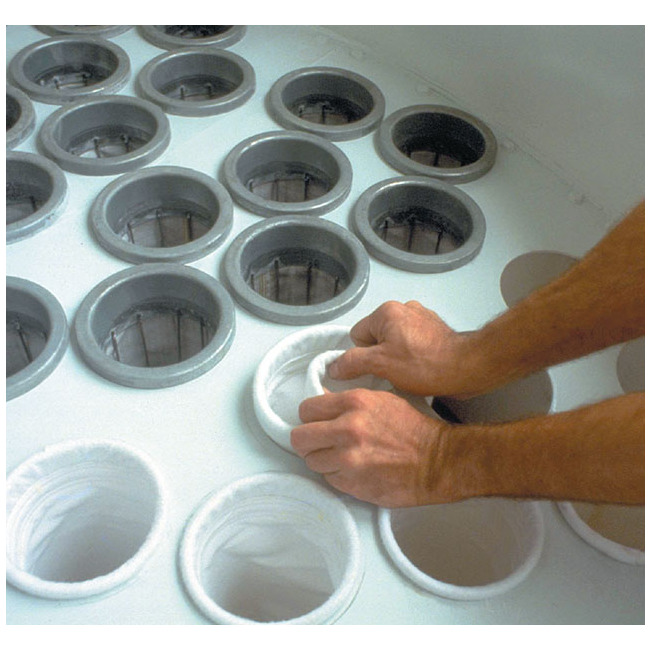
The importance of maintenance and cost
The selection of a filter bag for dust filtration not only depends on the material and filtration efficiency but also on maintenance and cost. Regular maintenance is necessary to ensure the longevity and efficiency of the filter bags. At the same time, the cost of the filter bag is also an important consideration, as it can significantly impact the overall operating cost of the dust collection system.
Factors to consider when selecting a filter bag based on maintenance and cost
When selecting a filter bag based on maintenance and cost, the following factors should be taken into consideration:
- Durability: A filter bag with a longer lifespan will require less frequent replacements and maintenance, thus reducing overall costs.
- Cleaning requirements: Some filter bags require more frequent cleaning and maintenance than others, which can impact the cost of labor and downtime.
- Ease of installation: A filter bag that is easy to install and replace can help reduce labor costs and downtime during maintenance.
- Price: The initial cost of the filter bag should be considered, as well as the overall cost of ownership, which includes maintenance, replacement, and disposal costs.
How to choose the right filter bag based on maintenance and cost
To choose the right filter bag based on maintenance and cost, the following steps can be taken:
- Determine the expected lifespan of the filter bag based on the operating conditions and the specific dust type.
- Compare the cleaning requirements of different filter bag materials to determine the most cost-effective option.
- Consider the ease of installation and replacement when selecting a filter bag.
- Evaluate the initial cost of the filter bag, as well as the overall cost of ownership, including maintenance, replacement, and disposal costs.
- Choose a filter bag that offers a balance of durability, cleaning requirements, ease of installation, and cost-effectiveness to meet the specific needs of the dust collection system.
Conclusion

In conclusion, selecting the right filter bag is crucial for the efficient and effective operation of a dust collection system. The choice of filter bag material, size and design, filtration efficiency, compatibility with dust type, and maintenance and cost all play important roles in the selection process.
Choosing the wrong filter bag can result in poor filtration efficiency, increased maintenance and replacement costs, and reduced overall performance. Therefore, it is important to carefully consider all of these factors when selecting the perfect filter bag.
We encourage anyone facing challenges in selecting the right filter bag to consult with experts in the field. Consulting with experienced professionals can provide valuable insights into the unique needs of a dust collection system and help ensure the selection of the perfect filter bag for optimal performance and efficiency.