Introduction
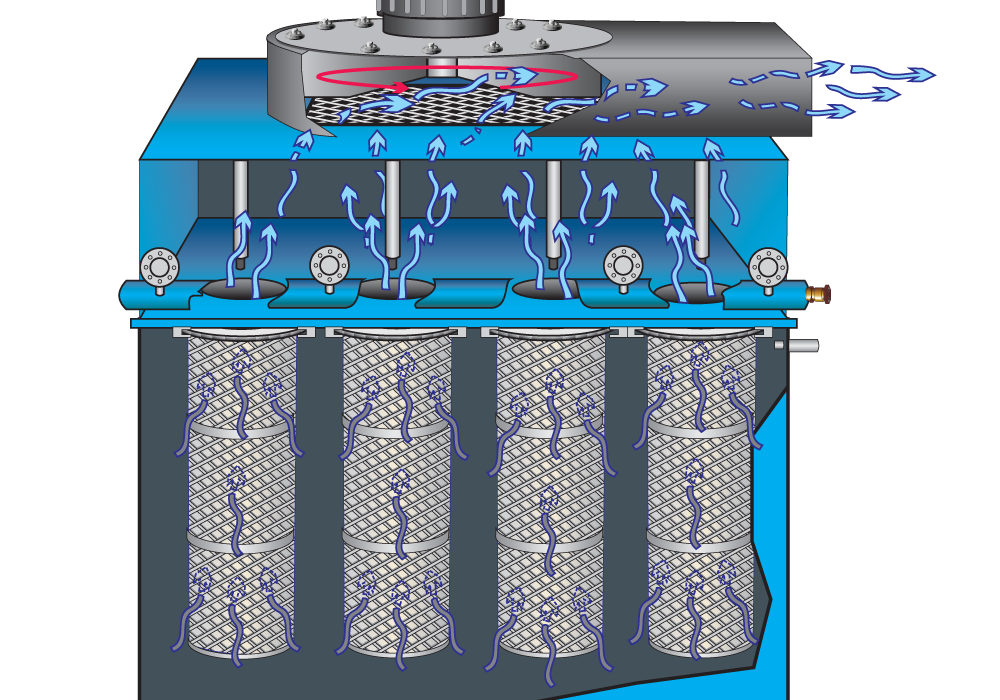
Dust collection equipment plays a crucial role in maintaining a safe and healthy workplace. It is designed to remove harmful particles from the air, protect workers from respiratory diseases, and reduce the risk of fire or explosion caused by dust accumulation.
However, choosing the wrong dust collection equipment can have serious consequences. It can lead to the inefficient collection, increased maintenance costs, and even pose a safety risk to workers. Therefore, it is essential to understand the common mistakes that people make when choosing dust collection equipment and learn how to avoid them.
We will discuss ten common mistakes to avoid when selecting dust collection equipment. In the end, you will have a better understanding of what to look for when choosing dust collection equipment, and how to ensure that you select the right equipment for your needs.
Not knowing your needs
One of the most common mistakes when selecting dust collection equipment is not knowing your specific needs. This can lead to selecting a dust collector that is too small or too large for your workspace, or that is not efficient in collecting the type of dust that you are dealing with leading to fine dust exposure. You may find yourself having a single stage dust collectors instead of two stage dust collectors for proper dust collection.
Therefore, it is essential to determine your requirements before making any purchasing decisions.
Some factors to consider when determining your dust collection needs include the type of material you will be collecting, the size of your workspace, the type of equipment you will be using, and the number of workers in the area. For example, a woodworking shop may require different equipment than a metalworking shop due to the different types of dust that are generated.
If you are unsure about your needs, it is recommended to consult with a dust collection expert or a representative from the dust collector manufacturer. They can help you evaluate your workspace, identify the type of dust that you will be collecting, and recommend equipment that is appropriate for your needs. They can advise better on where you need to use blast gates to control vacuum pressure.
For example, a company may have a large production facility with multiple workstations that generate different types of dust. By consulting with a dust collection expert, they may find that a centralized good dust collection system with multiple collection points is more efficient and cost-effective than individual collectors at each workstation.
By understanding your needs and selecting the appropriate equipment, you can ensure that your dust collection system operates efficiently and effectively, protecting your workers and your workplace from the harmful effects of dust accumulation by ensuring they do not breathe dirty air.
Choosing the wrong type of collector
Another common mistake when selecting dust collection equipment is choosing the wrong type of collector. There are several different types of collectors available, including;
- Baghouses
- Cartridge collectors
- Cyclones
- Wet scrubbers
Each type has its own advantages and disadvantages, and selecting the wrong type can result in the inefficient collection, more fine dust exposure, or increased maintenance costs.
Baghouses, for example, are commonly used in industrial settings and are designed to remove dust using fabric filter bags. Cartridge collectors are similar, but use pleated filter cartridges instead of bags.
Cyclones, on the other hand, use centrifugal force to separate dust particles from the air stream. Wet scrubbers are used in applications where the dust particles are too fine to be captured by dry dust collectors, and instead, use water or other liquids to capture and remove the particles.
Selecting the wrong type of collector can have a significant impact on the effectiveness of your dust collection system. For example, if you select a baghouse collector for an application that generates fine wood dust particles, the filter bags may become quickly clogged, reducing the efficiency of the collector and increasing maintenance costs. Similarly, if you select a cyclone collector for an application that generates wet dust or liquid droplets, the centrifugal force may not be effective in separating the particles from the air stream.
To avoid this mistake, it is important to understand the characteristics of the dust you will be collecting, as well as the advantages and disadvantages of each type of dust collector. Consulting with a dust collector system expert can also be helpful in selecting the appropriate type of collector for your specific application.
For example, a foundry that generates large amounts of fine dust particles may benefit from a cartridge collector, as the pleated filter cartridges can provide a large surface area for efficient collection without becoming clogged too quickly. On the other hand, a woodworking shop that generates large chips or shavings may benefit from a cyclone collector, as the centrifugal force can effectively separate the larger particles from the air stream before they reach the filter.
Selecting the appropriate type of collector for your specific application, you can ensure that your dust collection system operates efficiently and effectively, reducing maintenance costs and protecting the health and safety of your workers by ensuring good air quality.
Failing to consider the size of your workspace

Dust collection equipment is designed to provide efficient collection for a specific amount of air volume, and selecting equipment that is too small or too large for your workspace can result in the inefficient collection or increased energy costs.
It is important to consider the volume of air that needs to be filtered in your workspace when selecting dust collection equipment. This can be calculated using the air volume formula, which is the total cubic feet per minute (CFM) of air in your workspace divided by the number of air changes per hour (ACH) that you require. ACH is typically determined based on the type of activity and the level of airborne contaminants.
For example, a woodworking shop with a volume of 10,000 cubic feet and a recommended ACH of 6 may require a total CFM of 60,000 (10,000 x 6) for efficient dust collection. If the dust collection equipment selected only provides 30,000 CFM, it may not provide efficient collection and may need to be run for longer periods of time, increasing energy costs.
Another factor to consider when selecting dust collection equipment is the layout of your workspace. If your workspace is large and spread out, a centralized dust collection system may be more efficient than individual collectors at each workstation. However, if your workspace is small and compact, individual collectors may be more appropriate.
By considering the size of your workspace and the volume of air that needs to be filtered, you can select dust collection equipment that provides efficient collection without wasting energy or increasing costs. Consulting with a dust collection expert or a representative from the equipment manufacturer can also be helpful in selecting the appropriate equipment for your specific workspace.
For example, a metalworking shop may have a large workspace with multiple workstations and a recommended ACH of 8. By consulting with a dust collection expert, they may find that a centralized system with multiple collection points and a total CFM of 96,000 (12,000 x 8) is more efficient than individual collectors at each workstation.
Failure to factor in the type of dust you will be collecting
One of the most critical factors to consider when selecting dust collection equipment is the type of dust you will be collecting. Different types of dust can require different collection methods and equipment, and failing to consider the type of dust can result in the inefficient collection, increased maintenance costs, and potential health hazards.
For example, some types of dust are explosive and require specialized equipment to prevent ignition and protect workers. Combustible dust, such as sawdust, metal powders, or certain chemicals, can ignite if they come into contact with an ignition source, such as a spark or heat. In these cases, specialized equipment such as explosion-proof dust collectors, spark detection systems, and explosion suppression systems may be required.
Other types of dust may be hazardous to the health of workers and require specialized equipment to prevent exposure. Fine dust particles, such as those generated in woodworking or certain manufacturing processes, can cause respiratory issues if inhaled over extended periods of time. In these cases, specialized equipment such as HEPA filters may be required to capture the fine particles and prevent them from being released into the air.
It is important to consult with a dust collection expert to determine the type of dust you will be collecting and select the appropriate equipment. The expert can also help you determine the regulatory requirements for your specific application, such as OSHA’s National Emphasis Program for combustible dust.
For example, a chemical manufacturing plant may generate combustible dust and require specialized equipment to prevent ignition and protect workers. A dust collection expert may recommend an explosion-proof dust collector, spark detection system, and explosion suppression system to ensure worker safety.
Factoring in the type of dust you will be collecting, you can select dust collection equipment that provides efficient and safe collection, reducing the risk of health hazards and protecting the safety of your workers.
Failing to consider the level of filtration required

Another critical factor to consider when selecting dust collection equipment is the level of filtration required. Depending on the type of dust you will be collecting, you may need to use different types of filters to ensure efficient collection and prevent the release of hazardous dust particles into the air.
There are several types of filters available for dust collection equipment, including fabric filters, cartridge filters, and bag filters. The type of filter you select depends on the type of dust you will be collecting and the level of filtration required.
For example, fine dust particles generated in woodworking or certain manufacturing processes may require HEPA (High-Efficiency Particulate Air) filters to capture particles as small as 0.3 microns. HEPA filters are able to remove up to 99.97% of particles from the air and are commonly used in applications where fine dust particles can pose a health hazard.
On the other hand, larger particles generated in metalworking or other applications may be captured using bag filters or cartridge filters. These filters are less expensive than HEPA filters and can capture particles as small as 1 micron.
It is important to consider the level of filtration required when selecting dust collection equipment as choosing the wrong type of filter can result in the inefficient collection or potential health hazards. Consulting with a dust collection expert can help you determine the appropriate type of filter for your specific application.
A case in point, a metalworking shop may generate large particles that can be captured using bag filters or cartridge filters, while a woodworking shop may generate fine particles that require HEPA filters for efficient collection.
Overlooking the safety features
When selecting dust collection equipment, it is very important to prioritize safety features. Dust collection equipment can pose a significant risk to worker safety if not operated properly or if safety features are overlooked.
One important safety feature to consider is the use of explosion-proof equipment for applications where combustible dust is present. Explosion-proof equipment is designed to prevent sparks or other sources of ignition from igniting the dust, which can cause an explosion or fire.
Another important safety feature is the use of spark detection and suppression systems. These systems are designed to detect sparks in the ductwork and quickly extinguish them before they can ignite the dust. This can prevent fires and explosions from occurring.
It is also important to consider the use of interlock systems, which ensure that the dust collection system is shut down when other equipment, such as a saw or sander, is not in use. This can prevent unnecessary buildup of dust and reduce the risk of fires and explosions.
For example, a woodshop may use a dust collection system with an explosion-proof motor, spark detection and suppression system, and interlock system. These safety features help to ensure that the dust collection system operates safely and reduces the risk of fires and explosions.
Not factoring in the maintenance requirements
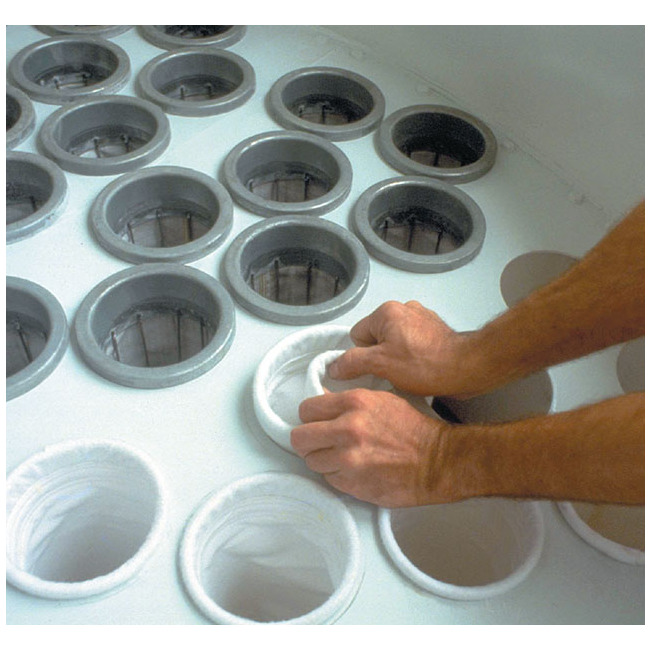
Another important factor to consider when selecting a dust collection equipment is the maintenance requirements. Dust collection systems require regular maintenance to ensure efficient operation and to prevent breakdowns and malfunctions.
Different types of dust collection equipment have different maintenance requirements. For example, baghouse filters require periodic cleaning to prevent buildup of dust on the filters. Cartridge filters may require replacement after a certain amount of usage, and cyclone separators may require regular inspection and cleaning to prevent buildup of dust and debris.
Failure to properly maintain dust collection equipment can result in decreased efficiency, increased energy consumption, and even equipment failure. This can lead to costly repairs and downtime for your operation.
It is important to factor in the maintenance requirements of the equipment when making a selection. This can include regular cleaning and inspection of the equipment, as well as routine replacement of filters and other components.
For example, a manufacturing facility may require regular replacement of cartridge filters on their dust collection system to maintain efficient operation. Failure to replace the filters on a regular basis can result in decreased efficiency and increased energy consumption, as well as potential equipment failure.
By factoring in the maintenance requirements when selecting dust collection equipment, you can ensure efficient operation and prevent costly breakdowns and repairs. This can help to minimize downtime and maximize the productivity of your operation.
Failing to consider noise levels
When you are selecting a dust collection equipment, it is important that you consider the noise levels that your equipment generates. Dust collection equipment can be loud, and prolonged exposure to high levels of noise can cause hearing damage and other health issues for workers.
Some dust collection equipment can generate noise levels above the recommended levels set by regulatory agencies, such as OSHA in the US. This can result in fines and penalties, as well as increased risk of worker health issues.
There are several factors that can contribute to the noise levels generated by dust collection equipment, such as motor size, fan speed, and the design of the ductwork.
To avoid excessive noise levels, it is important to select equipment with low noise levels or to take steps to mitigate the noise generated by the equipment. This can include selecting equipment with larger motors or fans that operate at lower speeds, or adding sound attenuation to the ductwork.
For example, a metalworking facility may select a dust collection system with a large motor and a low-noise fan to minimize the noise generated by the system. They may also add sound attenuation to the ductwork to further reduce noise levels.
Considering noise levels when selecting dust collection equipment, you can help protect the hearing and health of your workers, as well as avoid potential fines and penalties for exceeding recommended noise levels.
Not factoring in cost of ownership

When selecting dust collection equipment, it is important to consider the cost of ownership over the lifetime of the equipment. The initial cost of the equipment is only one part of the equation – ongoing costs such as energy consumption, maintenance, and replacement parts can add up over time.
By factoring in the cost of ownership, you can make a more informed decision about which equipment is the most cost-effective over the long term. This can help you save money and maximize the return on your investment.
For example, a facility may be considering two different dust collection systems – one with a higher initial cost but lower energy consumption and maintenance costs, and another with a lower initial cost but higher ongoing costs. By considering the total cost of ownership over the lifetime of the equipment, the facility can determine which system is the most cost-effective.
Factors to consider when factoring in the cost of ownership include energy consumption, maintenance requirements, and expected lifespan of the equipment. It is also important to consider any warranties or guarantees that come with the equipment, as well as the availability of replacement parts.
By making an informed decision based on the total cost of ownership, you can ensure that you are getting the most value for your investment and avoiding costly surprises down the road.
Overall, it is important to avoid the mistake of solely focusing on the initial cost of the equipment and neglecting ongoing costs. By factoring in the cost of ownership, you can make a more informed decision and save money in the long run.
Failure to do proper research
One of the biggest mistakes when selecting dust collection equipment is not doing proper research before making a purchase. Without proper research, you may end up with equipment that does not meet your needs or is not cost-effective over the long term.
Proper research includes not only gathering information on the equipment itself, but also on the manufacturer and their reputation in the industry. You should also consider reviews and feedback from other users of the equipment.
By doing proper research, you can ensure that you are selecting the right equipment for your needs and that you are working with a reputable manufacturer who can provide support and service when needed.
For example, a woodworking shop may be considering a dust collection system from a particular manufacturer. By researching the manufacturer, the shop may discover that the manufacturer has a history of poor customer service and that other users have experienced issues with the equipment. Based on this research, the shop may decide to look for a different manufacturer with a better reputation.
Proper research can also help you identify potential issues or challenges with the equipment, allowing you to address them before making a purchase. For example, you may discover that a particular type of dust collection equipment is not suitable for the type of dust you will be collecting or that the equipment requires specialized installation or maintenance.
Overall, it is important to avoid the mistake of not researching well when selecting dust collection equipment. By gathering information on the equipment, the manufacturer, and other users, you can ensure that you are making an informed decision and avoiding costly mistakes down the road.
Conclusion

Choosing the right dust collection equipment is essential for maintaining a safe and healthy work environment while also maximizing productivity and efficiency. However, there are many common mistakes that can be made when selecting this equipment, which can result in costly mistakes and suboptimal performance.
By avoiding these mistakes and following best practices for selecting dust collection equipment, you can ensure that you are making an informed decision that meets your needs and is cost-effective over the long term.
By avoiding these common mistakes and following best practices for selecting dust collection equipment, you can ensure that you are making an informed decision that meets your needs and is cost-effective over the long term.
For example, a manufacturing facility may have previously made the mistake of choosing a dust collection system without properly considering the type of dust being produced, resulting in poor performance and safety issues. By following best practices and avoiding this mistake, the facility can select a system that meets its specific needs and ensures a safe and healthy work environment for its employees.
Sofilt has been in the dust collection bag manufacturing industry for over 20 years and can help you select the right dust collection equipment to meet your needs. Our team of experts is here to help you make an informed decision and save money in the long run. Contact us today to learn more about our solutions.